working on it wrote:from 12-28-13 ...pieces of galvanized steel. Discouraging, sputtering, fuming results at first. Then, I got the feed speed right, and made a couple of lines of practice welds. My first. This is going to be a learning curve type of thing, and like my friends have told me, avoid galvanized steel (none of them will use it). I tried to avoid the fumes, and a stiff breeze helped; I used my auto-darkening helmet, but the combination of a bright outdoor sun and the arc turned the shade too dark for me to see thru (I'll have to figure out the best helmet/shade adjustment, or get a lower number plate). Much like most other things in my experience (at least the ones I wanted to do, and had difficulty doing at first), I will acquire the skill through practice and perseverance (that's my credo, and I'm sticking to it).
After reading this response from
CARS,
CARS wrote:Your friends are right. Don't use gal. metal for practicing. It's horrible enough when you HAVE to weld that crap.Your breeze idea also made your shielding blow away from the weld puddle.Get some clean mild steal and keep practicing!
I figured I would make some progress if I followed his advice. I guess not (since I tried the same, expecting different results). Tried the flux welder again today, again on galvanized steel (pipe fittings this time), plus coated ? mild steel, and a heavily chromed trailer ball. AGAIN windy, but I adjusted the helmet shade where I could almost see OK. The project: piddling around with spare 4x4 treated wood, steel, pipe fittings, and a trailer ball I had bought 25 years ago (for a S-10 I had, to tow a trailer-and boat-I never got) to piece together a makeshift towbar (pusher bar) to move my TTT in and out of the garage. Had a wild hair(hare?) caught in my head to see if I could build a quick-disconnect pushbar out of scraps I had on hand, and a whole afternoon of decent weather to try it. So I did. The almost finished piece needed
welding to secure the ball to the pipe and the pipe to the strapping (and the strapping screwed to the wood, and the hipbone to the....and so on). Well anyway, after last time's galvanizing experience, I tried to grind off the zinc from the pipe, and also the outer chrome from the ball (really thick, made in America back then...) so I could perhaps successfully weld them together. The fumes weren't so bad this time, but the lack of practice and trying to finish in the twilight yielded the same unsatisfactory results. Since I could at least almost see the items (as I was welding), I was able to actually get some penetration into the steel, and the welds held after I tested them with my
BFH, I consider today's effort a minor success. Lots of spatter, uneven spotting, and I never could keep the right distance from the work nor my feed constant. Also, though I shoulda done so, I didn't prepare the mild steel at all (had some type of coating, and I had no degreaser), so it wasn't easy to weld either. Total weld practice time now= 30 minutes. Time needed to become proficient= lots more! No time to clean up the finished piece, since it was becoming dark, and I now had a headache (allergies + zinc fumes; who knows?), so here is a pic of the un-chipped, un-cleaned, un-ground welds on my experimental pushbar:
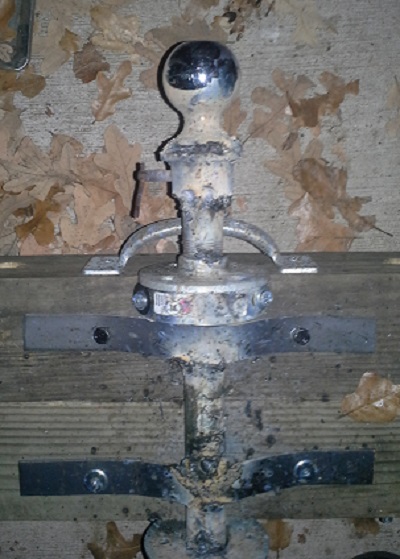
- 20140111_185722.jpg (80.16 KiB) Viewed 22418 times
I'll clean it up and grind it down next weekend, to see if it can be usable. Gonna be a long learning curve.