KCStudly wrote:Hey, I get more replies from my mothers cooking and my eating habits than I do from my build!
I'm keeping it clean.

You won't find any food porn in this thread. Unless you post it for me.

You do seem to eat well.
Meanwhile, back at the build...
The day started with the UPS guy dropping off a long cardboard tube.
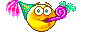
My molding arrived from Vintage Technologies.

Everything arrived in good condition, and I was ready to go to work.
They (whoever "They" are) say you should pre-bend your trim before you go to actually apply it. Sounds perfectly sensible to me. So I got with it. I got two kinds of trim molding,
their HT09 and the HT11. The HT09 will cover the outer gutter wall trim and the top of the galley walls. The HT11 trims the length of the roof/wall corners.
Since "trimming" seemed to be the theme of the day, I first trimmed those areas around the hatch that I had to built up before (dramatic re-enactment).

The router bit is a CMT 806.690.11 flush trim bit with a 2" cut length. I used the insert plate for my router table as a base, to give me more stability.
Results were good! The wall comes up flush to the hatch skin on both sides. Right:

Left:

Trying to bend the trim to the wall profile wasn't very productive as the trim springs back pretty much to where I started. I needed something with tighter curves. Just happened to have...

That is an offcut piece of the ply I cut my hatch spars from. Roughly the same profile only a tighter curve. This worked pretty good, and I was able to further curve the trim by running the trim piece over a corner while applying moderate pressure.
Here's the rough bend for the left side of the Tear:

Kinda looks like one of those "chalk around the dead body" drawings.
I've been wanting a nice bend on both ends of the roof skin. One to tuck under the front end, and one in back to transition the roof into the top galley gutter. The trouble is, the Tear is 5 feet wide, and most bending brakes apparently only go up to 4 feet. At least, the one at Tech Shop does. (Danger ahead) So I got to thinking...

could I make a quick and dirty brake that would work good enough for 3 or 4 bends in .032 Al? I had everything I needed: 3 2x4s and 3 good door hinges. Why not try? The bend on the front end doesn't really show, so it can go first. I get the strong feeling that I'm about to learn something.
Here goes:
Laying out the hinge-y part:

Rout a space for the hinge pin to go:

Screw the hinges on, and assemble:

Clamp the ... uh ... Clamper board so it clamps the work piece along the bend line:

OK. The first thing I learned is that even .032 Al needs more muscle than I have here on my knees with bare hands and no leverage. Let's raise it up a little and bring out the XL Super Bar:

That wasn't much better. Let's put it up on the sawhorses. Only a little bit better. Oops, game delayed on account of rain:

It was a nice little shower, about a tenth of an inch according to the official CapnTelescope electronic wireless rain gage. This gave me a chance to think.
What if I turned it upside down?

Hey, that looks like I'm halfway there already!
Success!

close-up:

Not bad. It's OK for the front end bend, but I want better for the back. I guess I'll have to find a sign shop or something.
Thanks for stopping by!
