I spent the first part of Sunday cleaning up the welds and the second putting together the floor. I finished up Kreg Screwing and Titebond III gluing the 3/4 inch poplar. That went pretty quickly. I had to put everything back in storage position so I could get the car into the garage for the week.
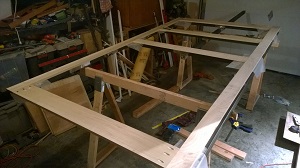
- The teardrop floor
- NA US WA Seattle - Teardrop Floor IMG001.jpg (51.25 KiB) Viewed 2361 times
So more framework is on hold. In the meantime, I started working on the profile. The grid patterns on the back of the wrapping paper actually did help with lining things up. Its not the same as drawing it out on Plywood. I must say that even with a 10ft length it seems like a short mattress. Luckily I have started shrinking and am no longer 6 ft. Maybe if the build takes long enough, I can use the 8 ft profiler. I also bought some parts that will be good to have before I get too far into the build so that I can make sure I don't go down a road that wont support the Fan-tastic Vent and PD4045 Power Center.
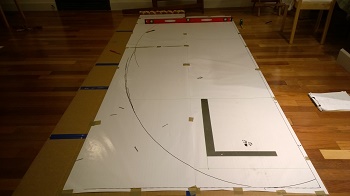
- Laying on the Profile.
- NA US WA Seattle - Teardrop Profile IMG001.jpg (48.29 KiB) Viewed 2361 times
I also started talking to an axle vendor in Seattle. Luckily I ran my design past my welder. He said that over engineering for the axle weight is actually a bad thing. If you purchase a #3500 axle for a #1000 trailer, it will be a rough ride. The weight of the trailer won't be enough to engage the softening mechanisms in the axle. I also found out that delivery time for the torsion axle was 6 to 8 weeks as each is made to order. Got me to thinking that if there was a breakage, I would be out a teardrop for a long time not too mention, a breakdown would surely happen at the remotest possible place.
So I decided to go with a #3500 axle and light duty leaf Springs. In stock and ready for me to pickup along with electric brakes and 2 tires comes out to about $700