Well it has been a little bit since my trailer came back from the shop. It now has tabs for the new floor layout. Two weeks ago I was going to start but realized that I didn't have a router or a couple other tools needed to start. Then the honey do list was given. So that week was out for getting some work done.
Then last week Texas had Snowageddon which halted the progress.
Yesterday I went to the wood shop to look at prices compared to big box stores. That is where I met Lee. He has been working with wood for over 70 years. In the hour he spent with me I learned so much about wood working, more than I have by videos and research. After I explained what I was looking at doing (tongue and groove the floor plywood) he told me that a rabbit joint would be easier. He explained how it would be difficult to get everything to line up. He then explained how easy the rabbit joint was and how to accomplish it. After he explained everything I was sold but was still worried about the joint holding up to weight without a support under the joint. Lee told me not to worry because he was confident that it would hold. Then I told him that I was also thinking about placing pocket holes down the joint for better support and he said that it would make the joint stronger. After the time spent learning I was ready to get the ball rolling. I ended up getting a router on sale ($50 off), a kreg jig master kit (came with a free box of 1000 screws), and the router bit needed to start the build.
So I went home and looked at everything I purchased and noticed that the bit would not work with the router. The bit has a max RPM of 16000 and the router was a 1 speed (27000rpm) router.

So I called up to the store and talked to Lee and he apologized. He said that he knew that but forgot with all the talking we did. I told him that I noticed at the store but didn't think twice because i was absorbing all his information. He told me to come back and switch out the routers for a variable speed router. I am glad I caught that because it would of been a big mistake. I really don't want to have to see my coworkers and ride in an ambulance on my day off. Plus I would never hear the end of it from them.
This morning I went back to the store and switched the router out for a variable speed router. I also bought the pin head kreg screws and titebond II glue I forgot yesterday. Then I headed home to get the party started.

On the way home I realized that I needed to get a scrap piece of wood to get the correct cutting depth on the router. So I stopped at the lumber warehouse to see about a scrap piece. So I met with Mel (don't want to give her name out so we will call her Mel) and explained what I wanted. Unfortunately they did not have a scrap piece of 1/2 baltic birch. But Mel stepped up and found a piece of scrap that matched up perfect to what I was looking for. All I have to say is that Mel always comes through for me. Thanks again Mel.
When I arrived back home I adjusted the frame so that it was level. After using a socket wrench I realized that I need to get a wireless impact driver. My arm was sore after leveling out the back 2 scissor jacks.
Well I started by rabbiting the scrap wood to get everything dialed in. And then it was time. It was time to really cut the wood for the floor. After the first cut I was good and made the passes on the other 2 sheets. All I have to say is the sawdust went flying and it was great. I now have the flooring cut and laid out over the trailer frame. I was curious how well the joint would work so I walked across them and I was surprised. With out supports under the joint the 1/2" was just fine. Next I have to cut each piece of plywood down to size and then glue it up which will have to happen another day. I also will add a pocket screw down the joint every 6 inches or so for added support which I know is over kill. Either before I glue and pocket screw the joints I will cut out the drop floor for the water tank. But before I do that I need to get a flush cut router bit.
Here are some pictures of the progress.
The trailer with the added anchor tabs.
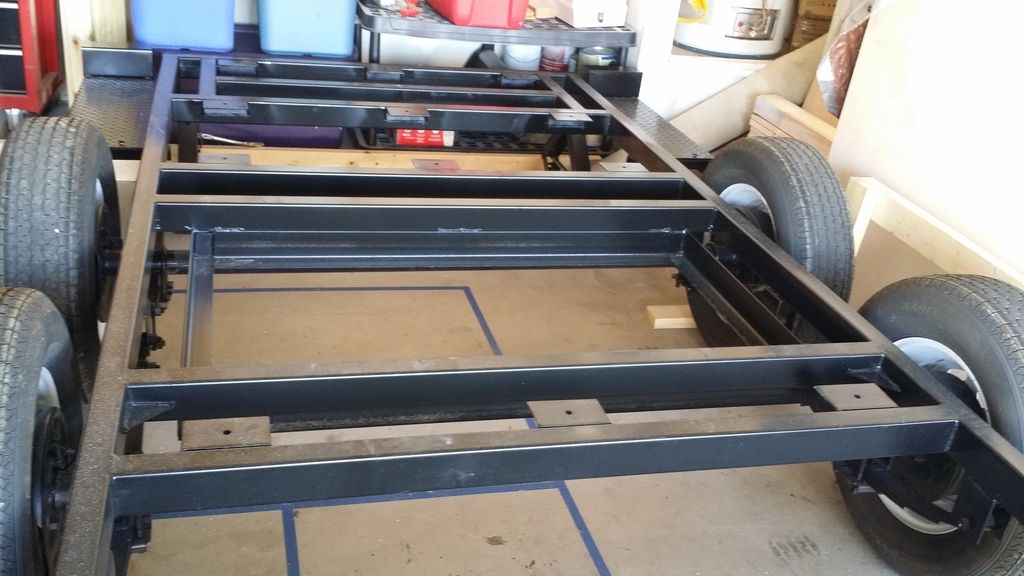
A close up of the anchor tab. I think 21 bolts will hold the floor down.
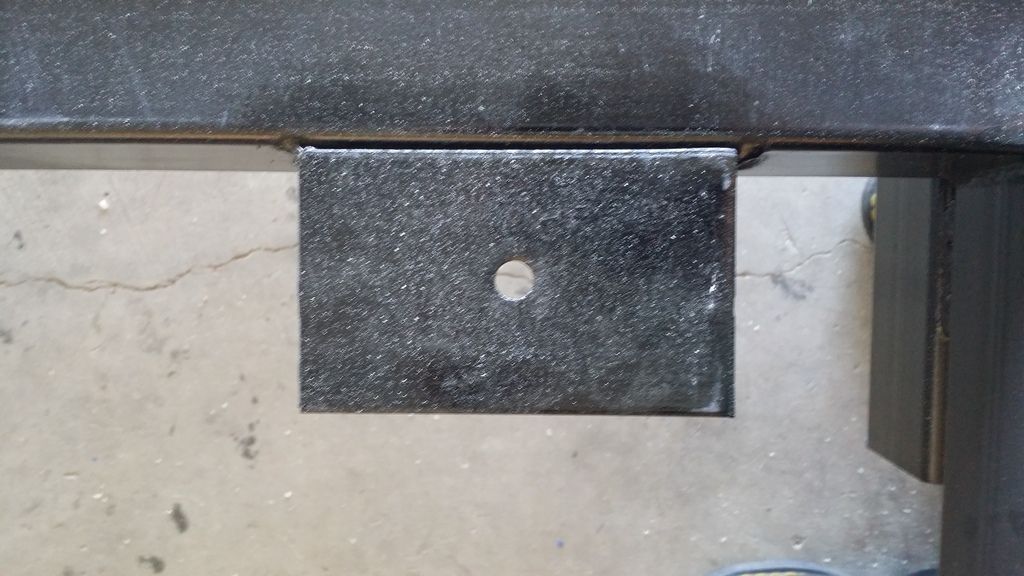
Here is the scrap wood that I was able to use. It was the perfect thickness and matched the thickness of the baltic birch. I cut the piece into 6 inch lengths for testing.
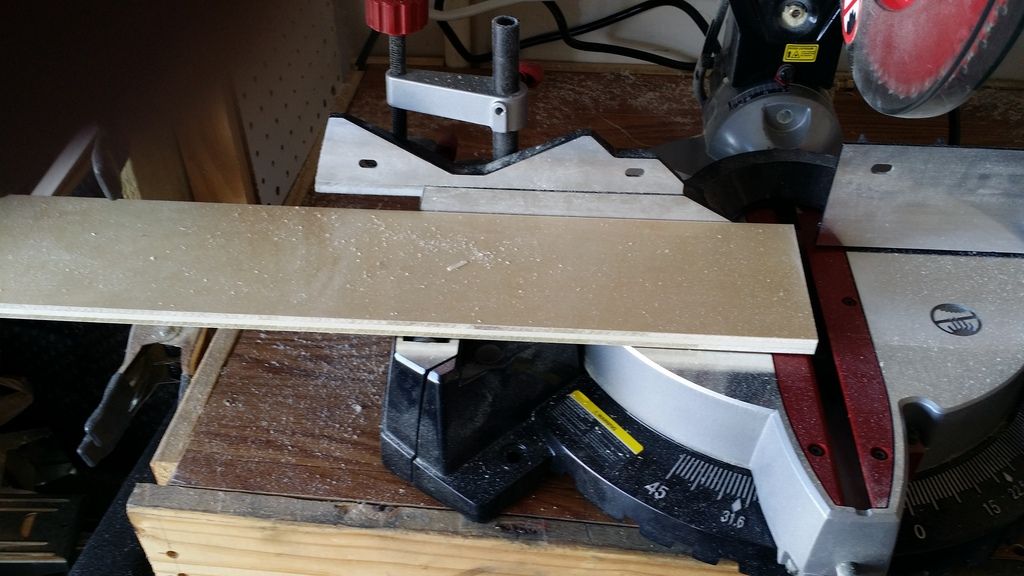
After several passes and utilizing all sides until I was able to find the correct depth.
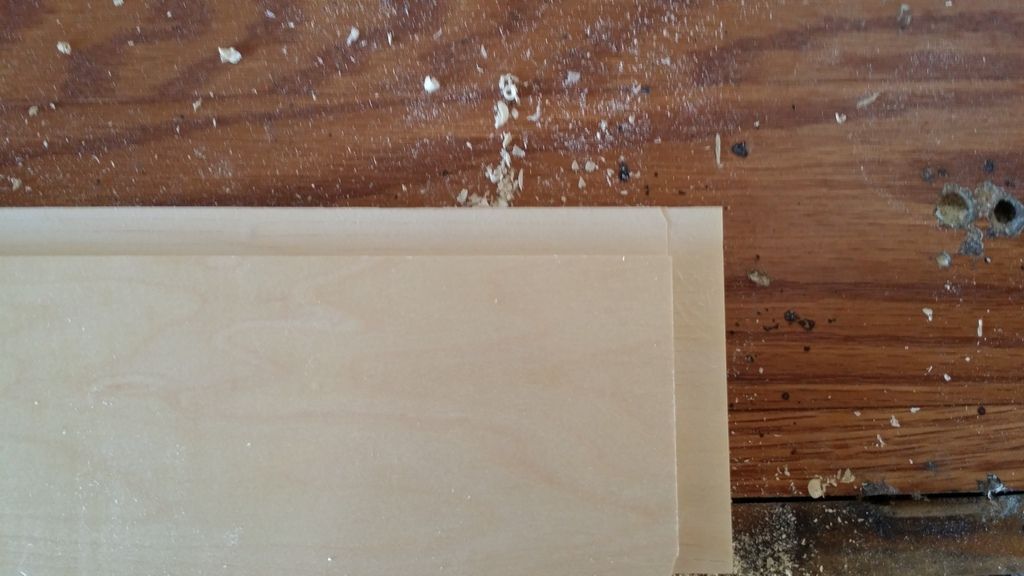
Here is what the joint looked like on the scrap wood.
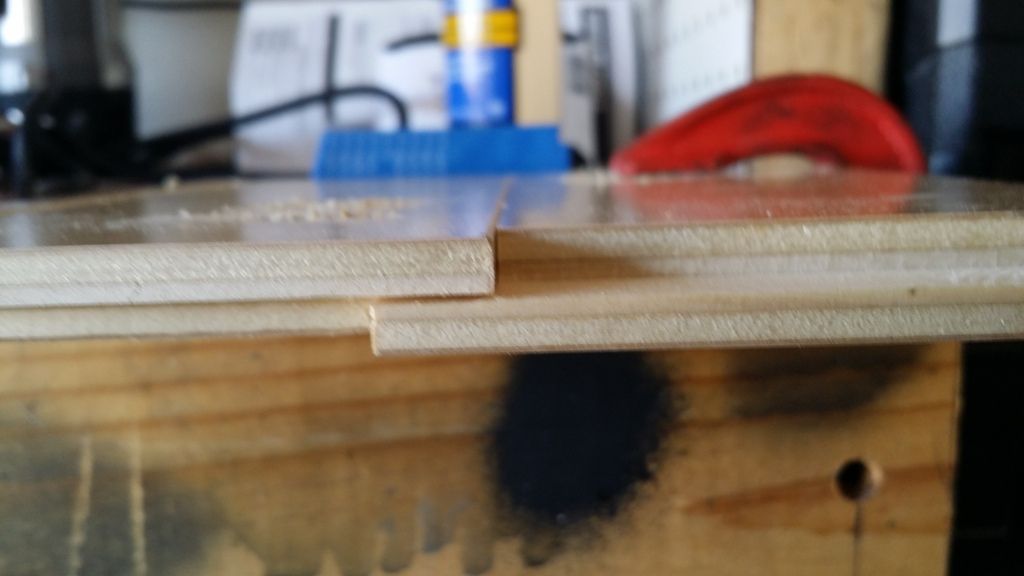
Drilled a couple of pocket holes to find the correct torque with my drill so that the screw didn't go through. It took me several times adjusting the torque. When I finally found the perfect setting the screw wasn't poking through or creating a bulge on the other side. All I have to say is after setting the screws it was a strong joint which makes me happy.
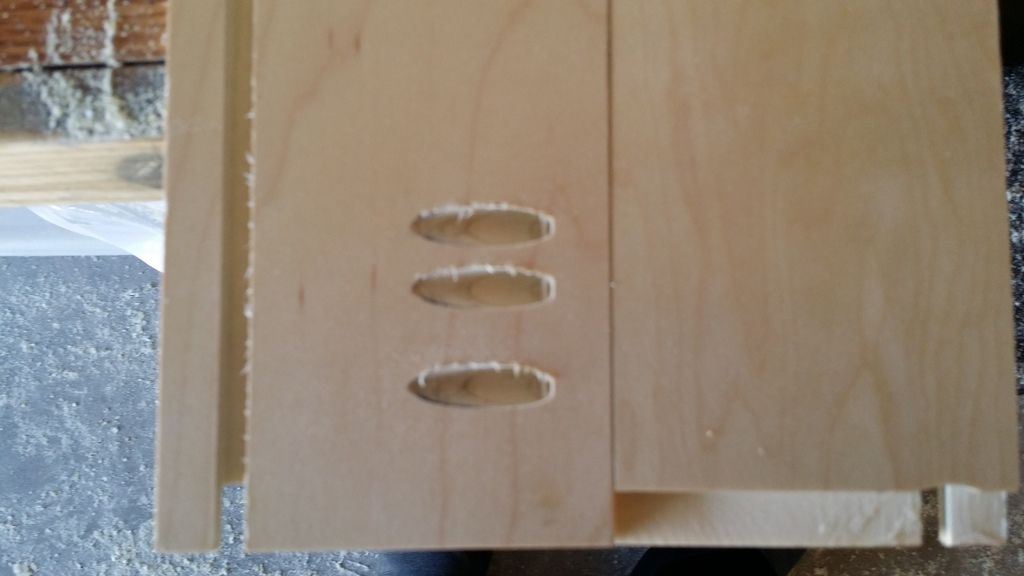
I used the trailer to hold the plywood so that I could cut the rabbit.
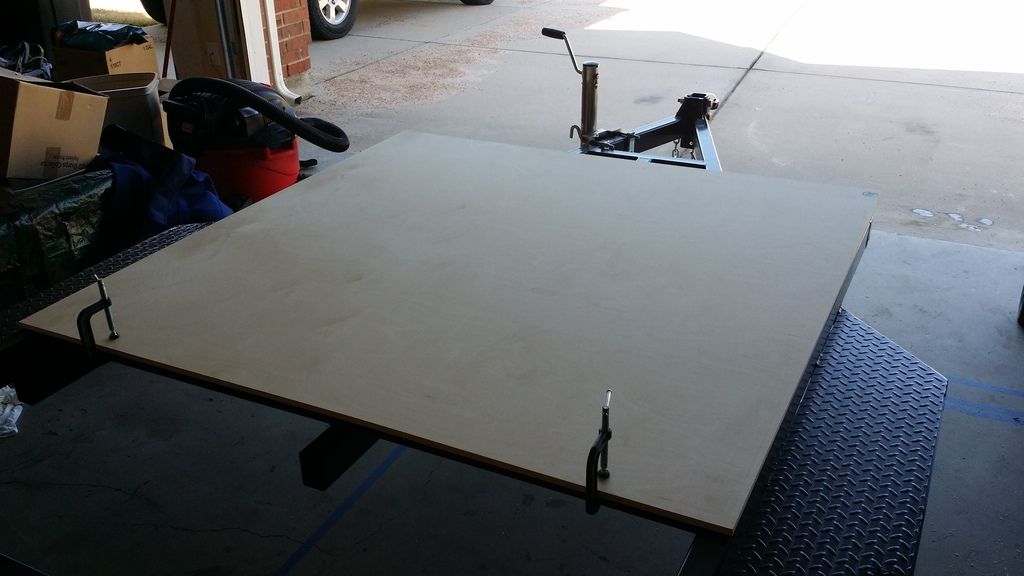
FINALLY, I made some sawdust. I know it sounds funny but I am excited to finally be starting this build.
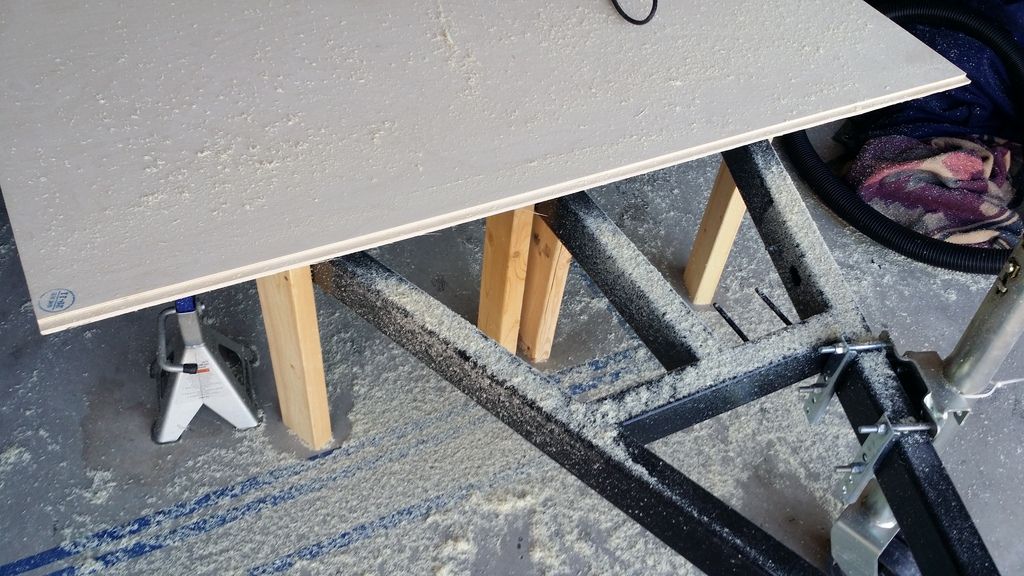
Oops I had a squirrel moment and made a small mistake. Nothing I can't fix or hide.
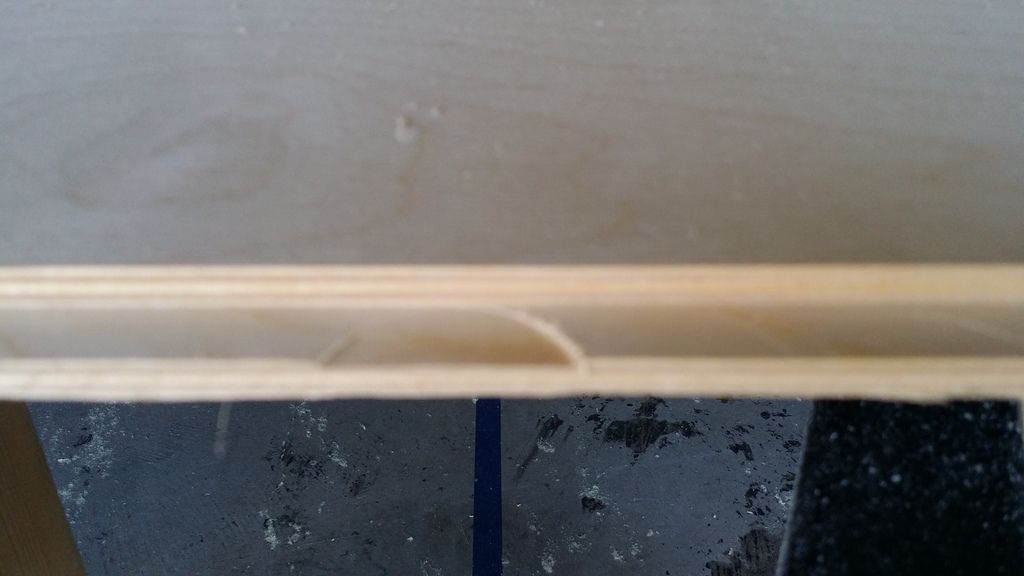
Got the first piece cut.
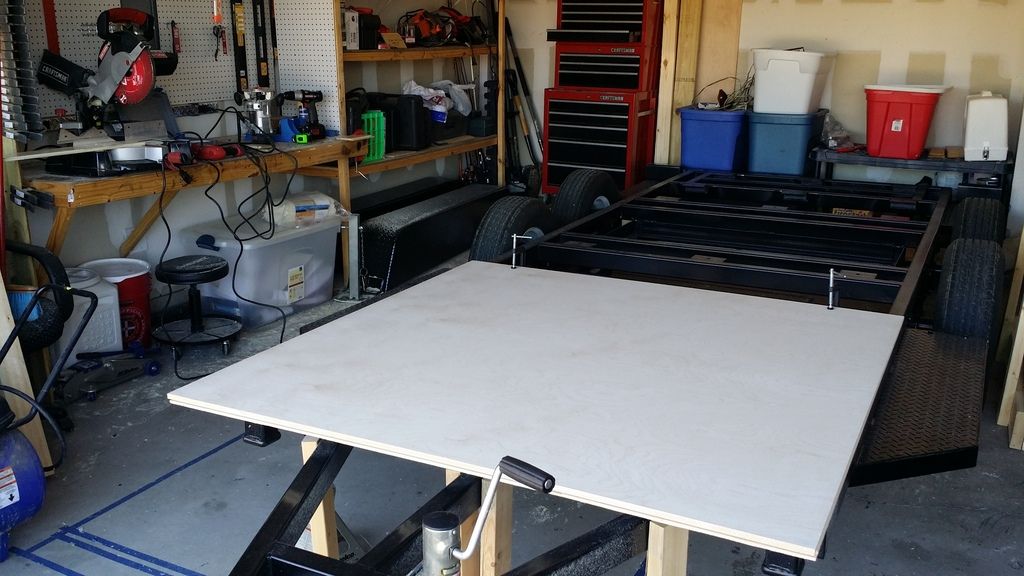
And here is the flooring mocked up. The second piece was bowed slightly so I used sand bags to hold it down. Hope that it will flatten out the bow if not then when I place the elevator bolts it will become that way.
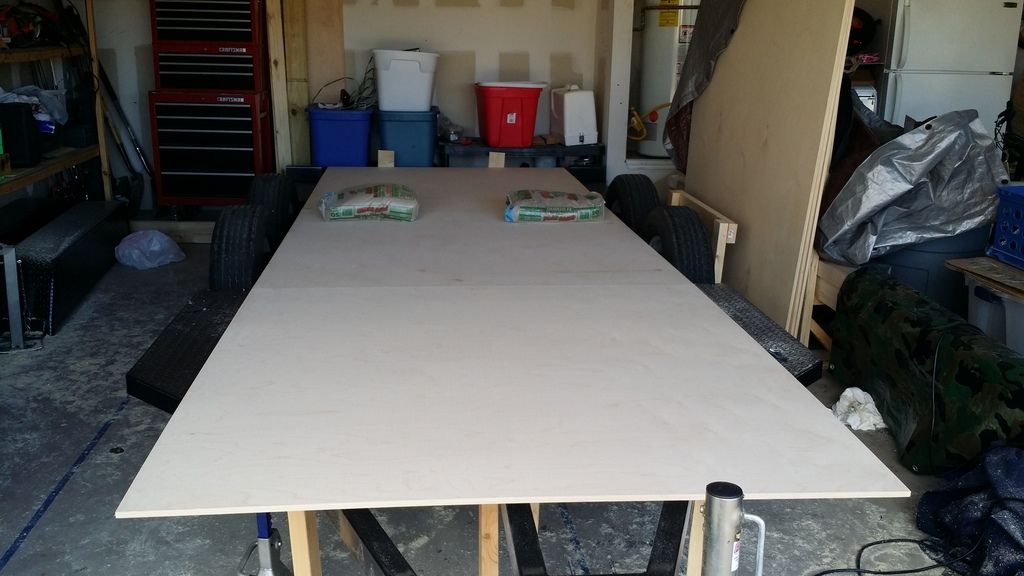

Hope you enjoyed.
Curtis