Boldly lead on!

With no one for you to learn from but your own trials, we'll allow you false paths and mistakes and try to encourage you on!
The methods of "strip planking" in the links seem to more resemble "cold-molding", in that the thickness of the strip is much less than the width of the strip.
Consider this cold-molding technique if the 2" thick-and-narrow strip method becomes impractical. May need no sanding to speak of. I've found cold molding to be faster and simpler than the thick-and-narrow strip method for gentle curves using rather wide, flexible, thin strips to "plank" each layer. But my experience is only at model scale using both methods.
Cold-molding the thin sheets requires a form, and key is clamping the layers; heavy blankets may be enough for the foam? Say four layers of 1/2" foam sheet. Bottom layer from say 8" wide strips run crosswise across the trailer on a foam-form-grid. Next layer from say 8" wide strips running -45 glued over the first layer. Next layer of say 8” wide strips running +45 glued over the prior two layers. Top layer lengthwise carefully fit edge-to-edge by trimming widths of the NEXT installed strip toward the ends, using the edge of the PRIOR installed strip as your guide.
Alternatively, 2” thick-and-narrow strip construction requires kerfs plus some keen and compound angles to be cut along the strip edges?
Finally, (my favorite due to simple construction but difficult shape lay out), three or more cylindric/flat sections (similar to your design before adding conics) butted at say 10 degree crown angle may be easiest? The inside joints aren't too bad, but the flare-out of the sides and the ends are a little dicey to get right...but as drawn, the roof has four identical "edges"; go ahead and kerf/model one "edge", say 3" wide, and hold it up to your beautiful walls and see what goes and what gives?
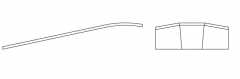
Here is the wikipedia "boat building" explanation for cold molding...
"Cold-Molding is a composite method of wooden boat building that uses 2 or more layers of thin wood, called veneers, oriented in different directions, resulting in a strong monocoque structure, similar to a fibreglass hull but substantially lighter. Usually composed of a base layer of strip planking followed by multiple veneers, cold-molding is popular in small, medium and very large, wooden super-yachts. Using different types of wood the builder can lighten some areas such as bow and stern and strengthen other high stress areas. Sometimes cold molded hulls are protected either inside or out or both with fibreglass or similar products for impact resistance especially when lightweight, soft timber such as cedar is used. This method lends itself to great flexibility in hull shape." You could foam-grid the interior and ply away at thin flexible layers using this method?
I'm out of ideas!
