I’m not sure, but I may have developed a new technique for working with foam. Chinking, yes chinking like how you would pack the spaces between logs in a log cabin. I guess it isn’t really a new concept; you can buy foam backing rod at any hardware store in the weather stripping aisle, but I was still pretty pleased with myself for finding a solution to my little problem.
You may recall that when I stuck the first layer of foam on the front roof using the stretcher method it pulled up away from the street side “sparette” (where my rock guards will eventually be attached).
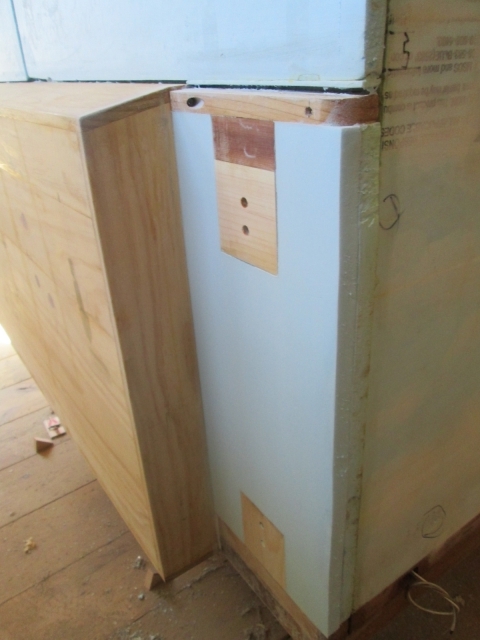
This has been bugging me. My reasoning is that if water were to get in under the canvas it might likely find a way to settle on this ledge. It didn’t make sense to try to carve this back enough to glue a new strip in, and there was some uneven globs of dried PL3 in the gap that would make sliding a sliver in there difficult. Plus the gap was large enough that more PL3 would not bridge it, and it shrinks some as it dries. GS was an option, but I wasn’t confident that I could get it in the narrow areas. I haven't yet mastered its application (be it getting an even application or not making a mess) and it always seems to be hit and miss for me on fairing the stuff back. Either I open up bubble pockets or gouge the surrounding foam when I try to sand it back fair.
Karl had more or less convinced me to just let it be and I had planned to just seal the gap at the side wall end once the next piece of foam went on. So I started dry fitting the next piece here. The locker bump out sits about 3/16 above the sparettes (accounting for the radius on the locker corners) so I had to shave a long thin notch in the bottom of this piece. I did that using the aluminum straight edge and the steak knife, which resulted in a nice thin drop piece of foam. Hmm, maybe I can fit a piece that small in the gap.
So I switched gears and started shaving little wedge shaped strips, but the dried PL3 hung them up when I tried to slide them in. Hmm, got a little block of wood to spread the load out some and my little mallet. Using the block of wood like a wide punch and tapping with the the mallet, I was able to pack the gap pretty well. Whatever was left out I just trimmed neatly with the steak knife. No glue or adhesive, no mess, and no sanding gouges. Basically I have a sound base so that when I stick the next piece down the adhesive will seal any minute gaps that remain.
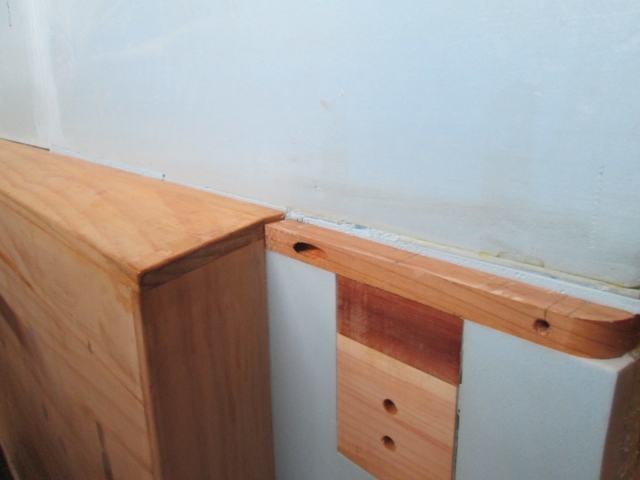
Here is the second layer piece fit over the locker and cut out around the axe head mount blocking.
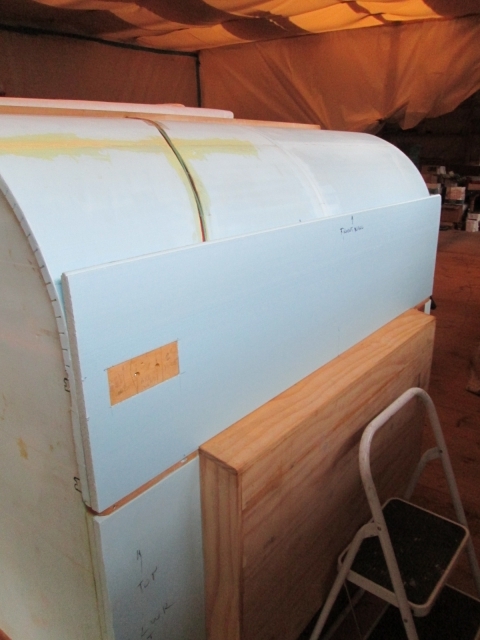
And another shot after kerfing the top portion; still just dry fit with a little packing tape to hold it to the curve.
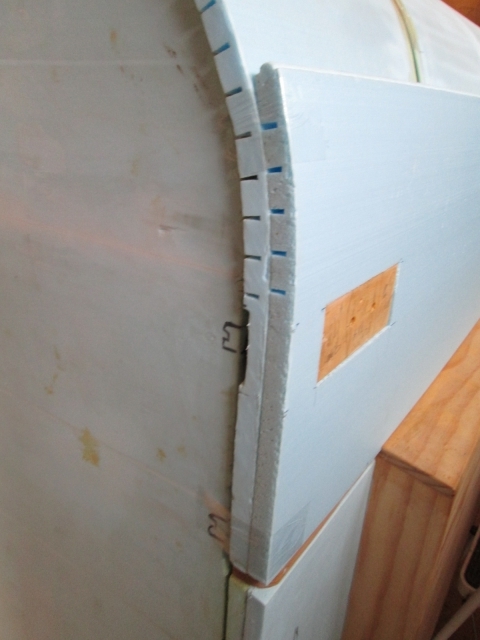
Backing up a little, yesterday I cut the last piece of foam for the top of the hatch. No kerfs needed since it is up on the flatter part of the hatch. It fit just about perfectly on the curb side, but I would have to taper the top edge about 1/8 inch over its length to get it to drop in along the full length of the hinge spar.
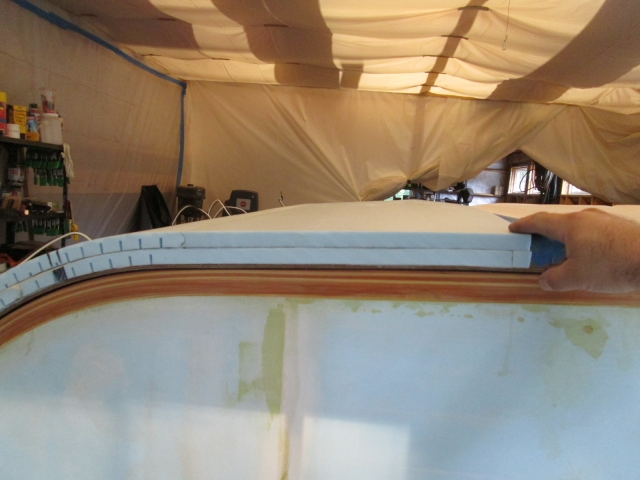
Here’s the factory bead and cove joint along the lower edge of this same panel, still just dry fit.
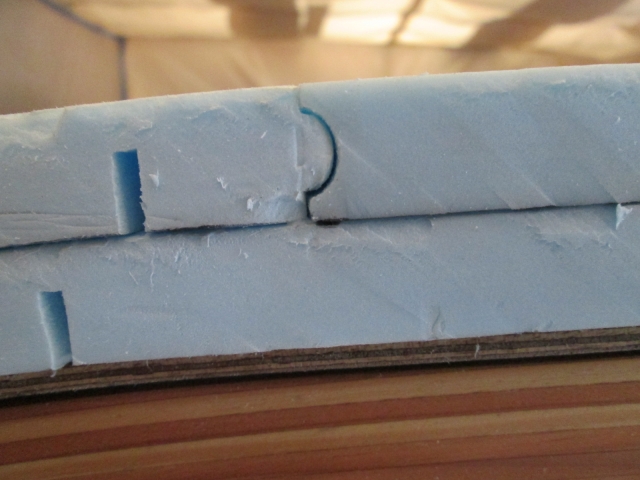
So tonight I used the same technique with the steak knife and aluminum straight edge to slice a thin wedge. Then just a few strokes with the sanding block, some more test fits, repeat, and she fits like a glove.
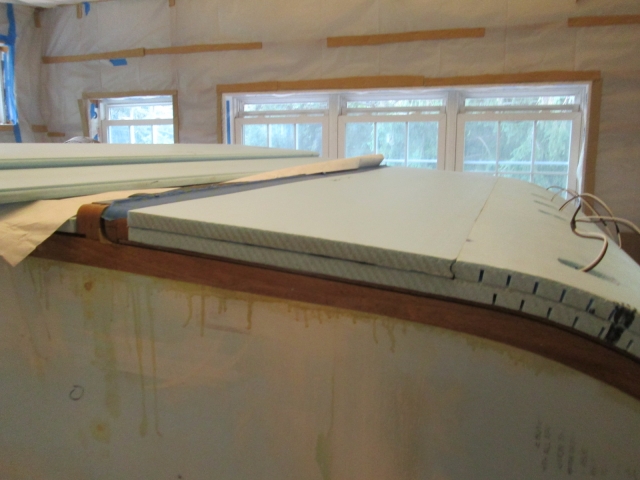
Back to yesterday, I ripped the flattened cove edge off of the stock for the 2nd layer at the upper front radius; kerfed it with fewer shallow kerfs near the top and more deeper kerfs over the tighter radius; and dry fit it.
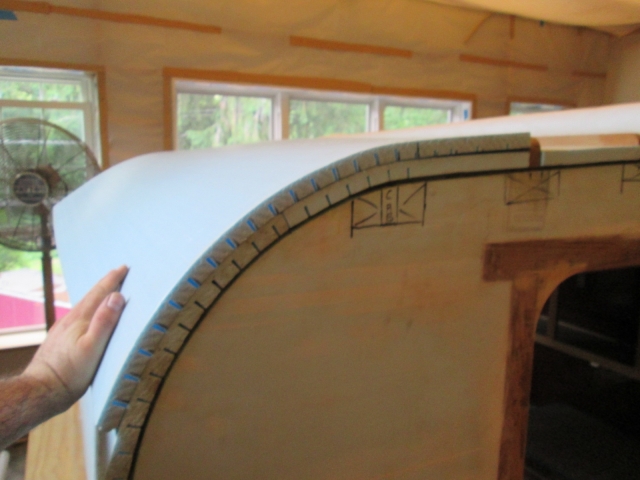
I wanted to start the 2nd layer at the larger top piece to offset the foam seams, figuring that I would cut the lower panel to suit once the top one was stuck down, but then I realized that it would be easier to fit and stick the lower piece first because of the details at the locker and axe mount. So I ripped that lower piece about 1/4 inch wider, figuring that it will give me the margin I need to recut the top edge of this upper piece.
Fortunately the drops off of the lower front and hatch upper panels are just a little wider than a couple of the roof bays, so those will be put to good use, too. In fact it’s looking like I will have several of the 2ft x 64+ inch panels left over.
Not sure how much I will get done tomorrow. Yvette is going to cut my hair and the lawn is up to my knees; need to do spring maintenance on the mower and string trimmer, too.