To update on Frankie, apparently she (?) wandered off after I left, then came back the next day for a while and wandered off again.
On the build, as mentioned previously, I bought a bunch of the 60 inch wide 6oz glass cloth, enough for 2 plies all over the cabin, hatch and to do the doors separately and then some; but have been trying to get the TB out of the 38 wide that Karl donated, and the smaller piece of 60 wide that I bought for reinforcing the ceiling front radius. Those smaller stocks are running out so I am trying to maximize the yield by doing careful layouts.
I could break into the bigger stash, but I would have to figure out a way to roll out enough of it to prioritize the larger sections before taking smaller bits here and there. I may even buy some more of the narrow stuff to complete the TB and do the first ply on the hatch on the bias, since I think there would be less waste using the narrower stuff this way.
Anyway, I had one piece big enough to do the underside of the TB, which I decided could get away with one ply (since it is over plywood… with 2 separate bias plies over the stiffening rib). I decided to use the PMPP technique on the underside because the slot for the stiffening rib would destabilize the cloth running lengthwise, so I cut that piece to length, prepared the plastic, traced out the template and rolled it up for safe keeping until I get to the layup (no pics).
I had hoped to get all of the bias strips for the TB rim out of the other 38 x 36 inch piece, but couldn’t quite stretch it (not literally) that far. At first I figured all I would have to do would be to lay out 5 inch wide bands on the plastic, I even made some marks directly on the cloth; but those will likely just confuse me and I wished I hadn’t done it. In the end, with the templates I realized that all of the little tucks and darts on the smallish pieces were going to make them pretty fragile in the layup stage, so decided that wetting them all out as one using the PMPP process (again) would be the most efficient, meaning that there would be less waste by having common cut edges and that the plastic would hold the parts stable while applying.
So I cut the cloth along the diagonal and flipped one piece back on the other. I wasn’t able to get the long back rim piece to fit comfortably, so that will have to come from somewhere else, but I did fit all of the other pieces. Since there is symmetry from right to left I only had to flip the templates over to get right and left. (Even though I could have just peeled the top or bottom plastic off to get the same thing, I decided it would fit the cloth better and avoid confusion to do it this way.) Also, I didn’t bother cutting longer strips of the rosin paper for the front and rear rim pieces; I just templated one end to the centerline, then flipped this pattern over to get the other end, making sure to double check overall dimensions before marking the patterns on the plastic. Here is the bottom plastic with two triangles of cloth and the templates, just checking to see if it would all fit. Note the 45 deg lines drawn on the big plastic sheet covering the worktable below. The template on the right is the half pattern of the front rim; the one in the middle is the longer curb side; and the one on the upper left is the small rear side and corner.
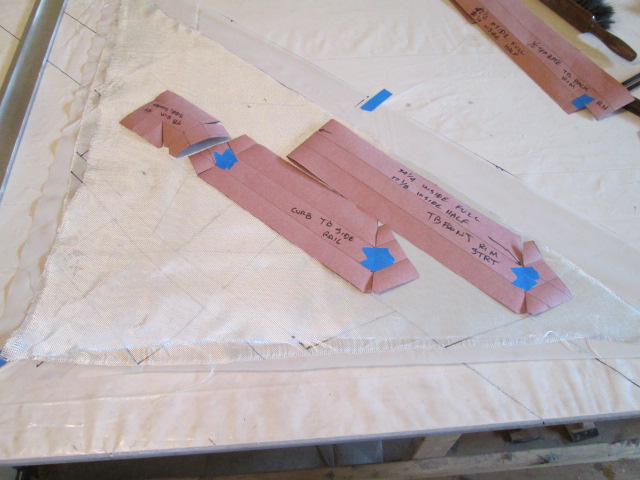
Now they are flipped and repositioned to see that I could get the other half.
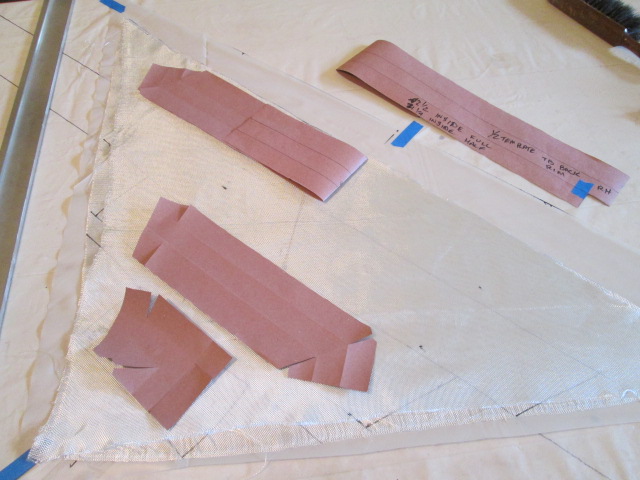
With that settled, and after finding that I had screwed up on the length of the front piece… fortunately leaving it too long, not too short… I started tracing templates onto the bottom sheet of plastic.
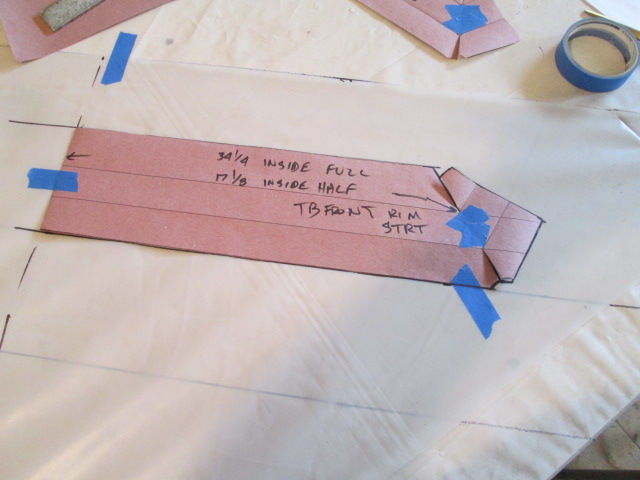
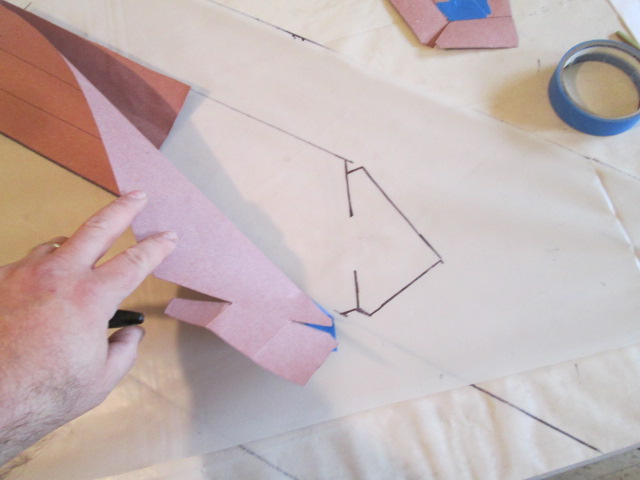
Now you can see how this should save both cloth and epoxy by having common cut lines and doing the wet out as one operation; less extra border will be wasted. Note the centerline shift on the larger top pattern, and the dashed lines that will help me line the pieces up with the edges of the rim when I go to lay them on.
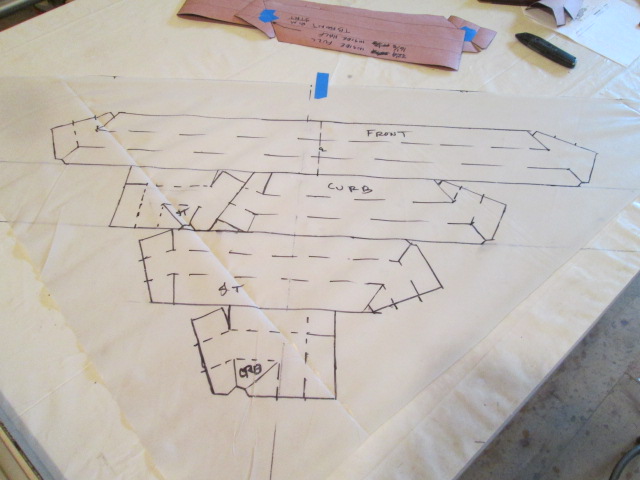
I also put sharpie lines on the front and rear rims of the box to mark the center lines, thinking that this will also help get the wet pieces in their proper locations.
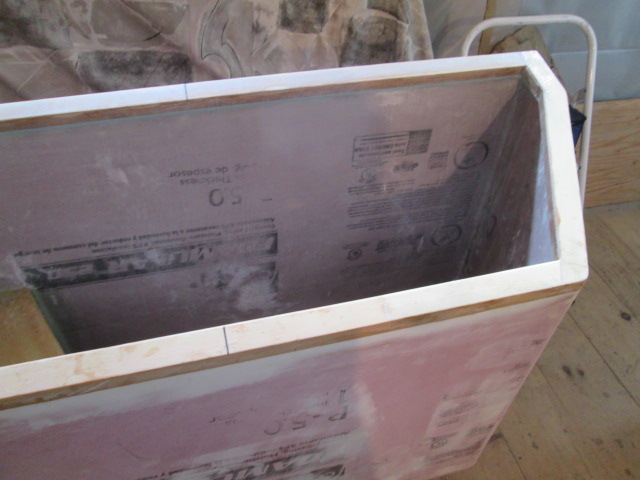
Double checking to see that everything fit under the glass before topping with the other sheet of plastic and rolling it up for safe keeping.
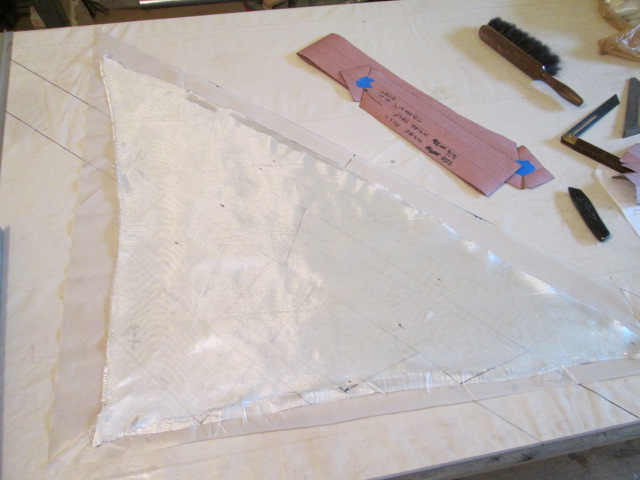
Shifting gears a little, I used the router template for the rock guard blocking and added a square cut for the TB latch blocking. By positioning the cut at the correct distance from the long edge it was a simple thing to align the edge of the template with the top of the rim and clamp it to the lip. I ended up using a few more clamps than shown here (to make sure the template wouldn’t slip) and moving the near side clamp down to make sure there was enough room for the router base.
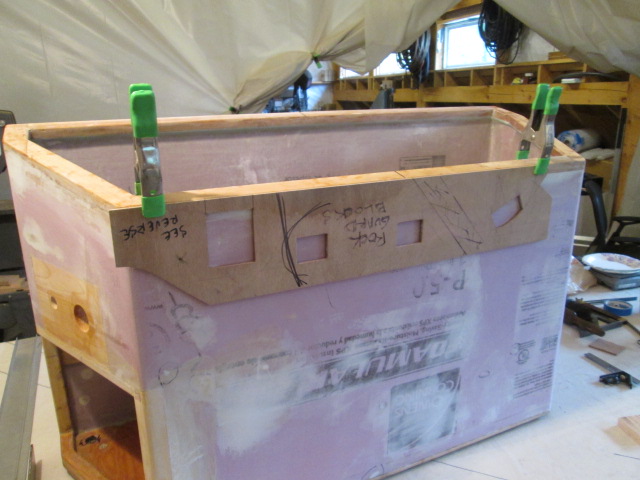
After extending the template lines up and matching them to marks I had measured on the top surface of the rim, I eyeballed things again with the block to be sure I was happy with the location.
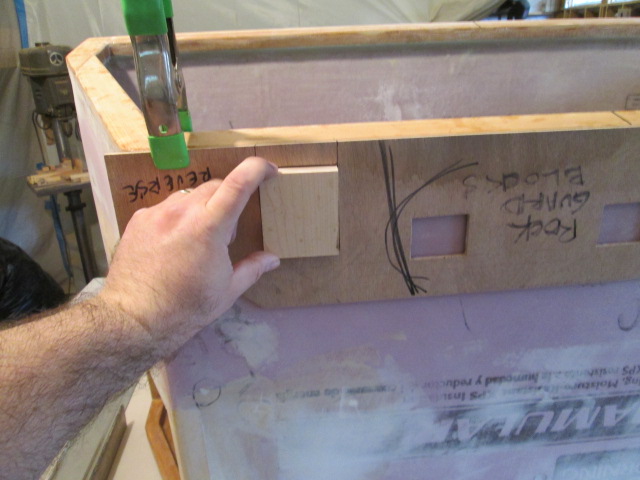
Then I made a shallow test cut to check that the template was a good fit for the blocks. Satisfied with that, I readjusted the router to full depth, made the cuts, and squared up the corners with the steak knife.
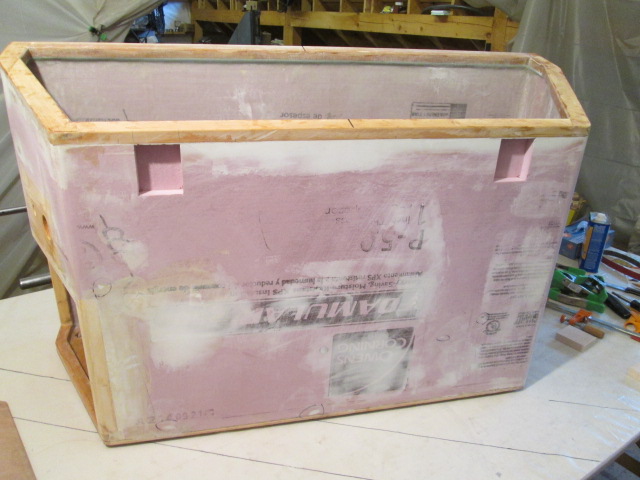
Then a dry fit. Shown here with the blocks just partially inserted to make getting them back out easier. I did check the depth on one by pushing it all the way in, but I had to gently pry it back out with the knife.
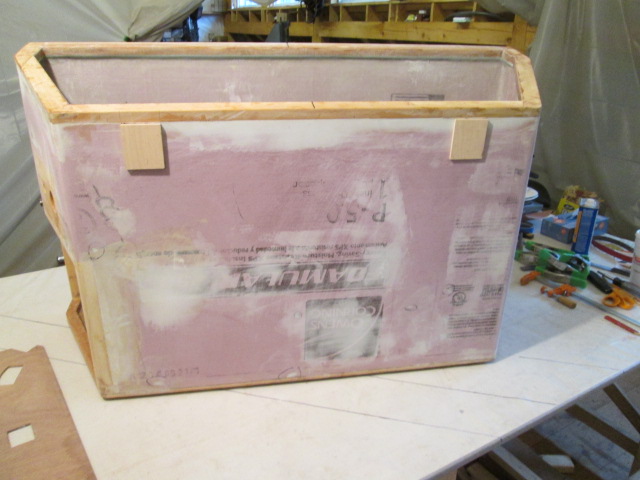
I had completely forgotten to bring my glues and epoxies today (overnight lows have been dipping into the low 40’s), so that is where I left off.
Still, doing this all, plus cleaning out the shop vac and fiddling with the stupid push button retainer cap for the vac filter and finally modifying it to accept the older style plastic nut, took about 4 hrs.
This evening (Saturday) Yvette and I went out for Mexican food and then to the Garde Theater to see Buddy Guy fronted by Quinn Sullivan. Excellent!