I did make it out to the shop on Friday for a couple of hours, so let’s get caught up.
Here’s that trim router setup with the guide fence.
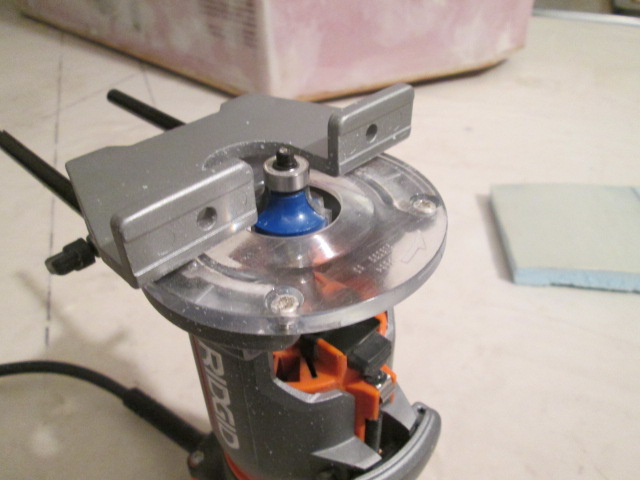
I sanded the test piece back square again and ran the router putting the shoe on the glass side and the fence along the foam edge. It worked much better.
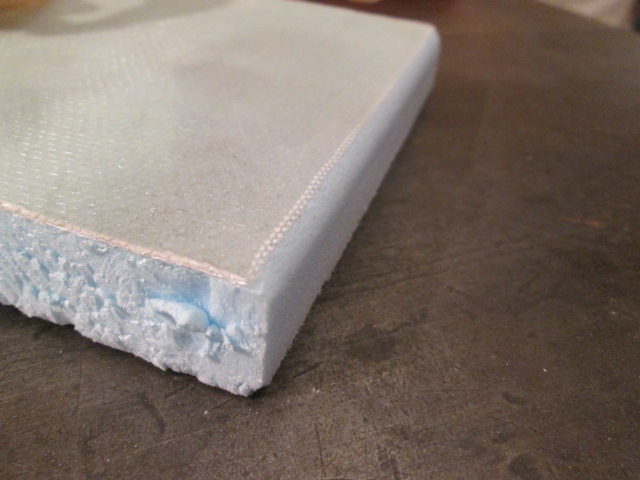
However, when I tried it on the real deal it didn’t take a full cut.
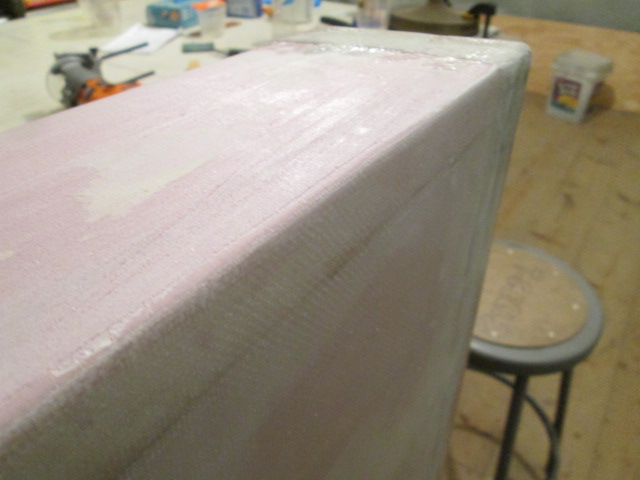
Still not sure what was going on here, perhaps the glass has a little wave to it keeping the router shoe “average” above the local, or maybe the corner isn’t exactly 90 deg (although I didn’t check it and don’t think that is it). No matter, the next logical thing to do is to step up to the 3/8 round over bit.
Unfortunately, the 3/8 bit won’t fit in the handy trim router because the outside diameter of the cutter is too big for the opening in the base plate, and I don’t have a guide fence for the larger routers. After looking thru all of my router jigs I found a small makeshift circle cutting jig that already fit the base of the 1/4 inch Ryobi.
The flat head screw heads stuck up above the face of the 5mm luan. I didn’t want to wallow out the holes by countersinking thru the thickness of the ply, so I added some of the leftover wooden washers to the back side. I also had to open up the clearance hole for the bit, which I did crudely on the jigsaw table.
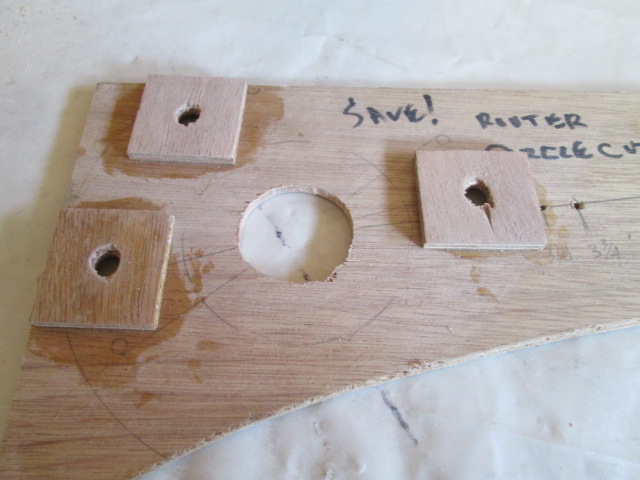
Once that was done, Saturday morning I could open up the holes and countersink them deeper.
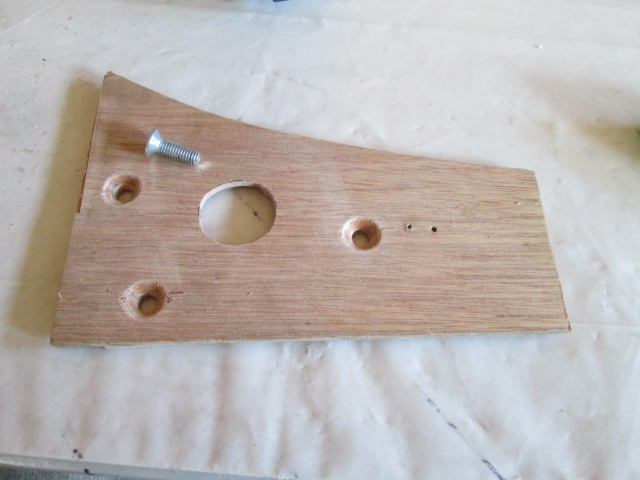
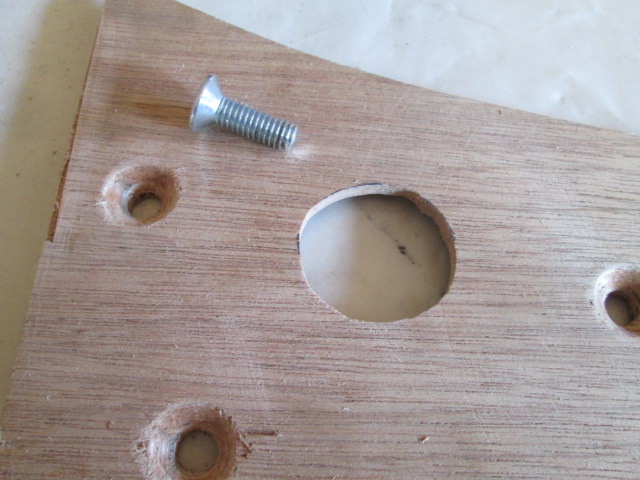
This gave me a base to attach a fence to. That required some crafty positioning and an extra hole to maintain access to the base screws. Once I had it figured out I used another straight piece of wood to align the reference surface of the fence to the roller.
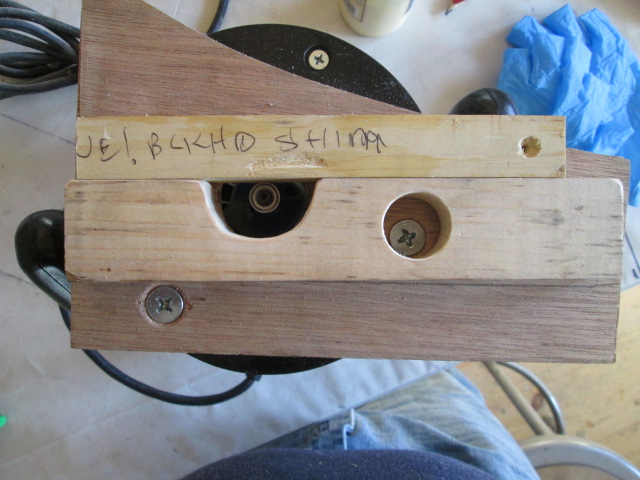
Then I glued the fence down with a couple of spring clamps at the edges to hold it. I wanted to use this right away so I left the clamps on, unscrewed the jig, flipped it over and sank a couple of FH screws thru to pin the fence to the ply.
From there it was back on the router to confirm the roller alignment and get to work.
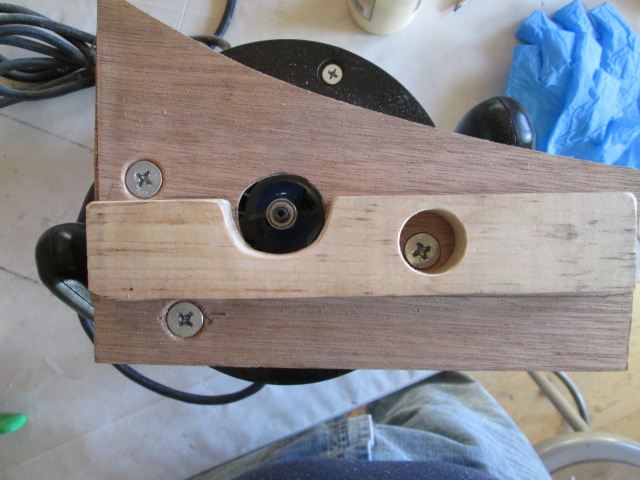
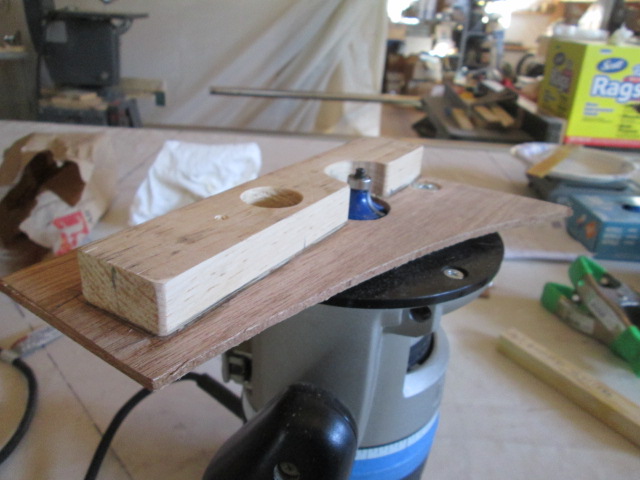
Back to the test piece for a nice fat round over.
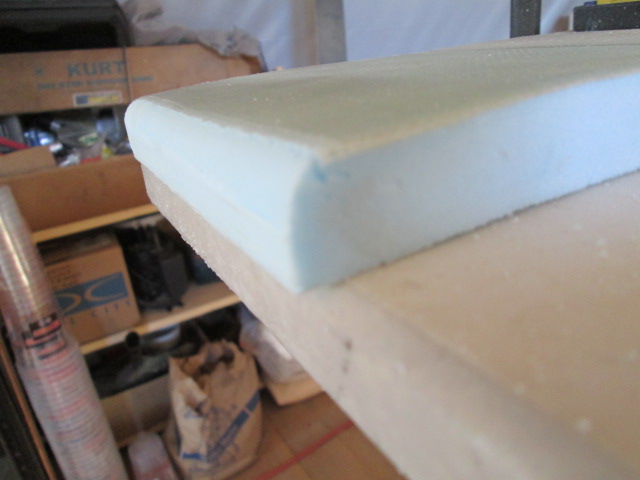
Back to the real deal and the resulting cuts ended up just like I had intended in the first place.
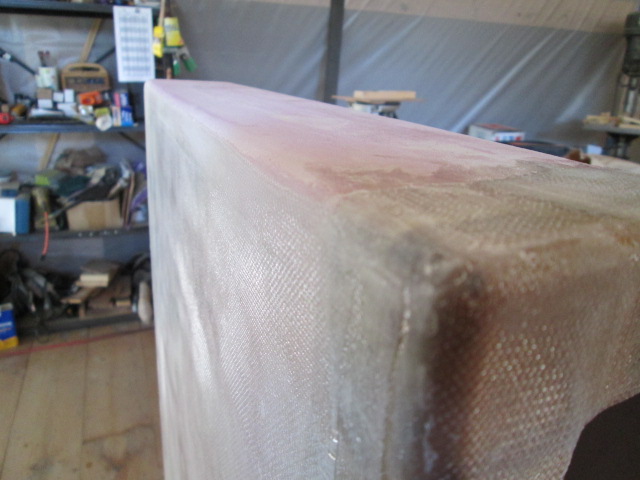
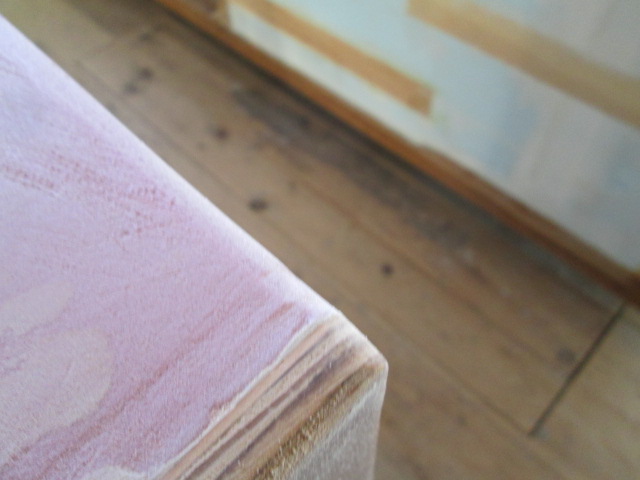
That got me back to glass prep. Whipped up a couple of patterns for the bias strips for the jamb and sill of the battery box. First pic is both, second pic is just the rear jamb.
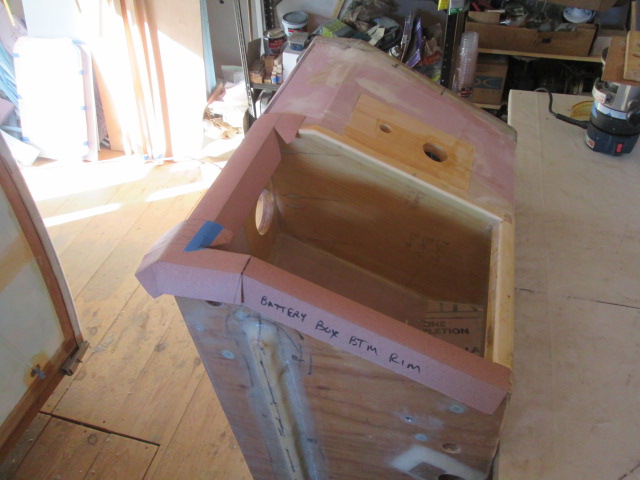

Getting smarter now, for the inside corners of the battery box opening I went into my bag of scrap glass bits and pieces and pulled out some bias bits to cut these corner fillers from. That way if the relief cuts and darts in the main layup don’t cover it all these will.
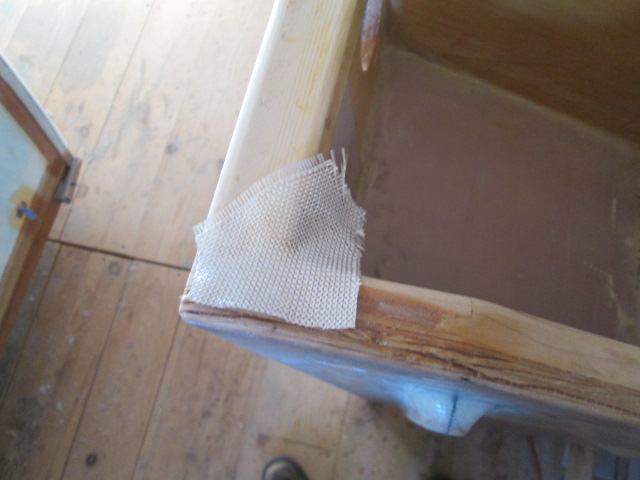
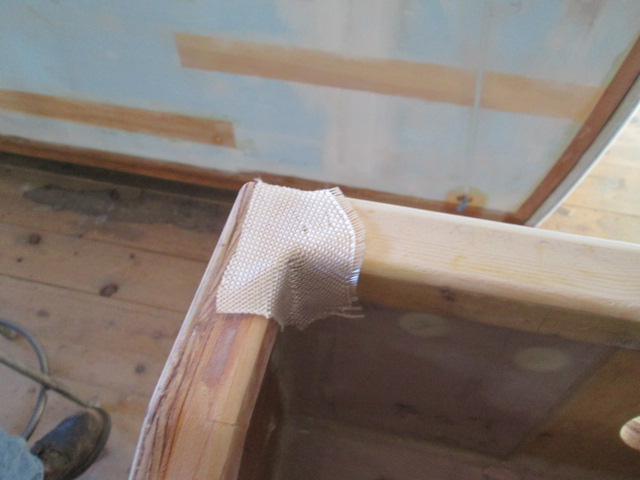
That was still a pretty sharp corner, so I decided to hot glue some foam wedges in. Then just a little work with the small hand sanding block. Nothing too fancy, but it will get the job done.
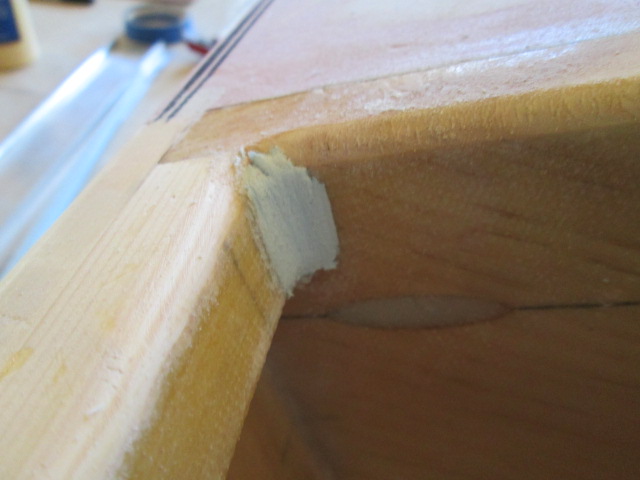
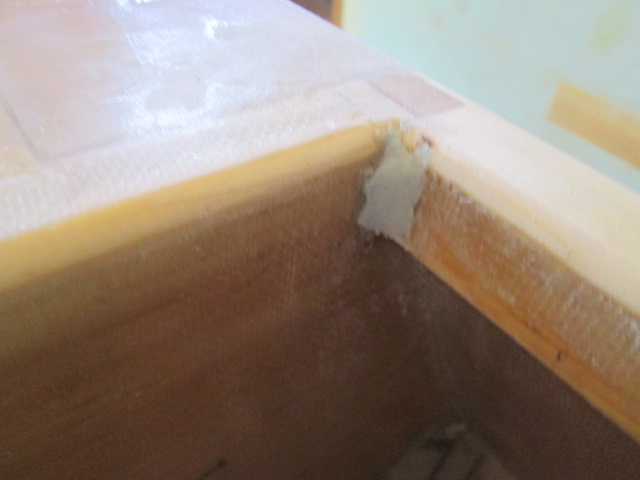
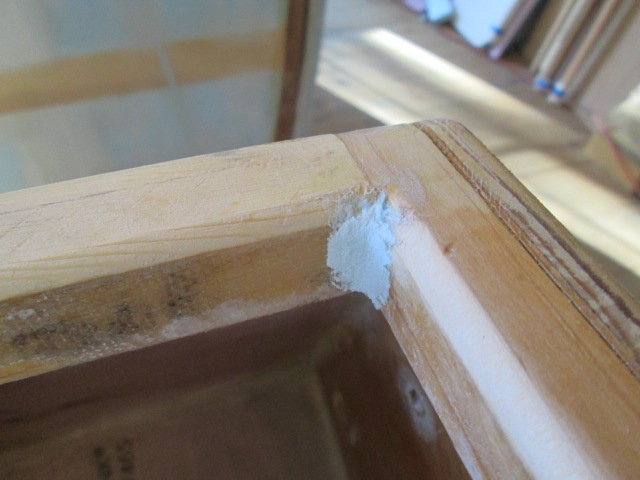
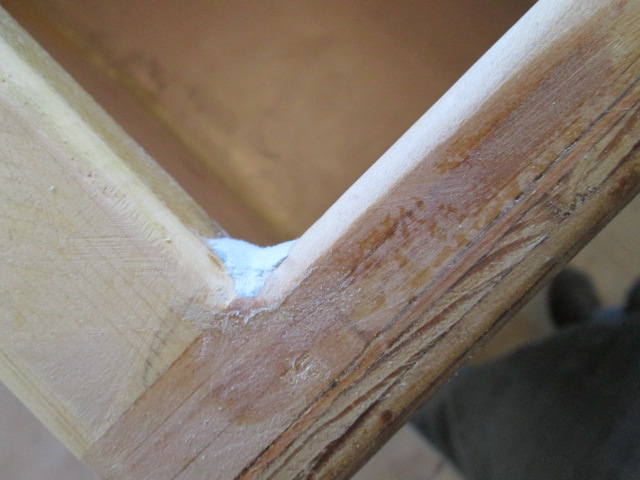
The bias corners dry fit much better now; much more likely to lay down with no bubbles.
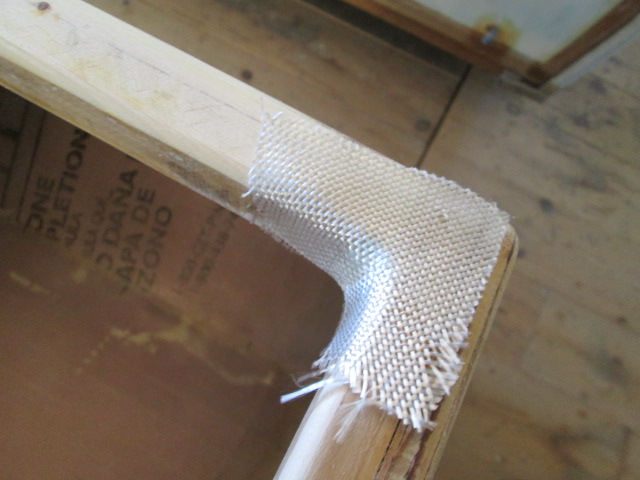
Prepared the plastic to PMPP the battery box rim pieces. I had a piece of plastic that was the perfect size for one of these, so I went with it, only to realize after the fact that I could have saved a little waste if I had paired these up along a common cut line into one wet out. The glass and epoxy cost a lot more than the plastic sheet and should have had the priority. Oh well, next time.
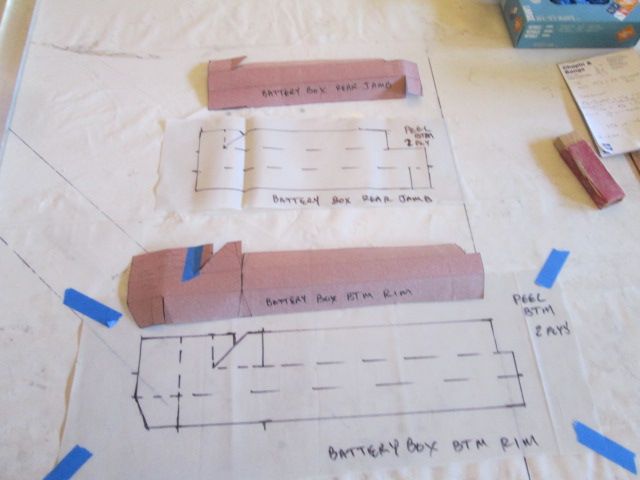
Next step was to add reference lines on the big front/sides cloth for the cutout for the battery box. After laying that out on the bench I rolled the prepped cloth back up and unrolled it again over the box to get a better idea of where I would have to trim and/or add darts.

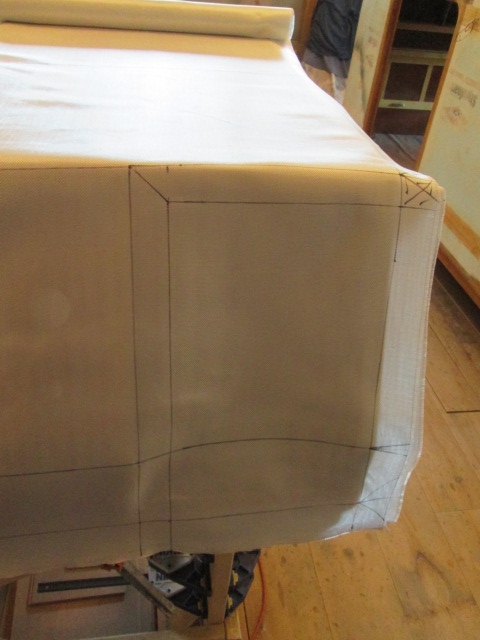
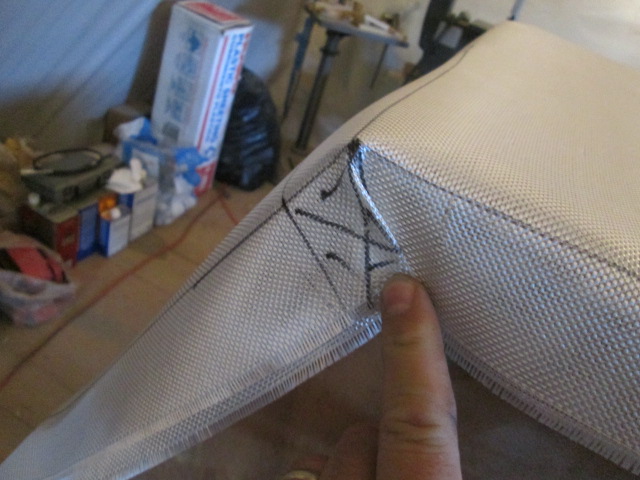
Here in the northeast we have a lot of greenery, including deciduous trees. They are lovely, providing shade in the summer and glorious colors in the fall. But then you have to do something with all of those leaves after they drop, otherwise they will kill your lawn and you won’t have to mow in the summer (!?!). Anyway, having worked for a debris removal equipment manufacturing company we have learned that using power equipment to do these types of chores is much quicker and less blister producing than hand raking. We have used hand held blowers, push blowers, backpack blowers and Karl’s big zero turn mower, but this year Karl got a
Cyclone Rake to attach to the zero turn. Since he is always very generous and helps with our yard, I gave him a hand Saturday afternoon putting it together. Then after he did his large yard in just a few hours, we loaded it up on the trailer to do mine Sunday morning. It worked out great. With the long hose/wand attachment we were even able to suck the leaves up from under the boat and down around by the garage where the tractor would not otherwise be able to reach. I have no affiliation with this company, but I can tell you we were both very impressed with the quality and engineering that had gone into it, and it performed very well.
After doing that and getting cleaned back up, I headed out to the shop to help Karl unload, then set straight into the final layup on the tongue box.
In handling the box it has been virtually impossible to avoid minor dents and dings. That and the slight step at the rim layup meant I would at least be adding some “thick” to start. Also, some of those little spots we got doing the back of the box did turn out to be “dry” spots (I’m thinking small dents where the cloth bridged across, despite being pushed down with the roller… remember that I didn’t bother fully smoothing the rear of the box because it will not be seen). Anyway, this helped me decide to try a dry on wet layup. I figured I would have Karl help me lay the cloth neatly onto the wet, that it would go okay that way, trimming excess and the battery box opening on the fly, and would give me a better feel for if I wanted to use this technique for the hatch and cabin.
This would be a pretty big layup and I had some concerns for how I would be able reach it all to do the thick fill around the top rim, do the three panels (five if you count the front and each of the side facets individually), the battery box rim, and wrap them all under the bottom at the same time. So I walked thru the different positions in a dry run. I would do the battery box rim and a small patch inside the battery box first with the TB standing on end on the floor. Then I wrapped a pair of the cedar 4x4’s in stretch wrap to hold the box up off the bench on its back enough to tuck the flap under onto the bottom. I’d set the box on its back with the rim toward the edge of the bench first so that I could add the thick fairing; turn it around so that the bottom was out; wet out the surfaces; place the cloth (easier said than done, near disaster… Karl had gone inside hours ago), then proceed with the wet out. To get the last flaps wrapped from the sides to the back I would flip the box up with the top rim resting on the plastic wrapped 4x4’s. I figured out the resin requirements for each panel, wrote those down for reference and got down to business.
Other than the difficulty getting the first ply of cloth into position (I had originally tried to position both plies as one, but when I missed on the first attempt I pulled the top ply off… which was still dry… and concentrated on getting the first ply to lay down first), everything went pretty much as planned and I worked steadily along for about 4 hours mixing and spreading epoxy. On the horizontal surfaces I used the credit card to spread, dragging excess over the corners onto the slanted and vertical surfaces (cardboard on floor to catch drips). On the slanted and vertical surfaces I used Michael’s cut down bristle chip brush trick to daub it on from the mixing cup and poke, poke, poke it into the weave. The stiffer bristles of the cut down brush really did work better pushing the epoxy in, and it still worked okay wetting out the foam beforehand, too.
Here are the after pics with the box resting upside down on its rim. I let the top (bottom in pics) of the cloth run long, wetting it out up into the start of the rim radius. I will trim this off and sand the edge to blend it back in after the cure. I have found that to be the neatest way to avoid a ridge or uneven seam.
The curb side with battery box.
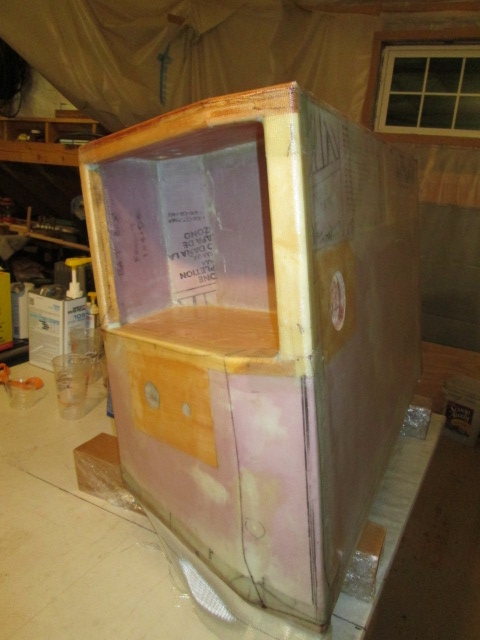
Battery box sill and rear corner.
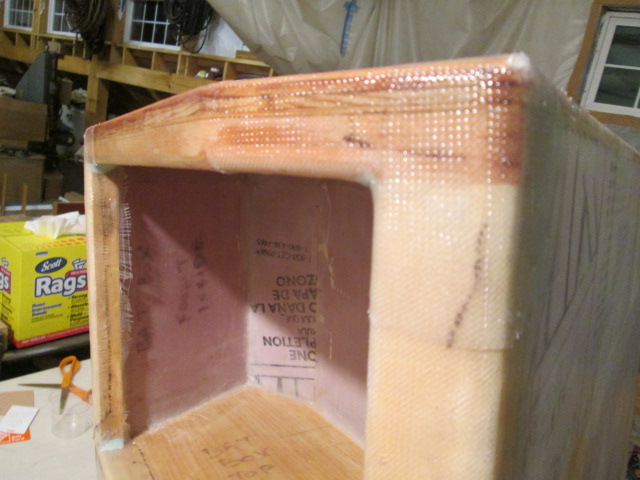
The flap that wrapped into the front jamb of the battery box got a little funky. You can see how the second ply pulled up short of reaching the inside edge, and how that inside edge was too sharp for the first ply to wrap all the way inside, but it covered the exposed wood and can be trimmed off flush later.
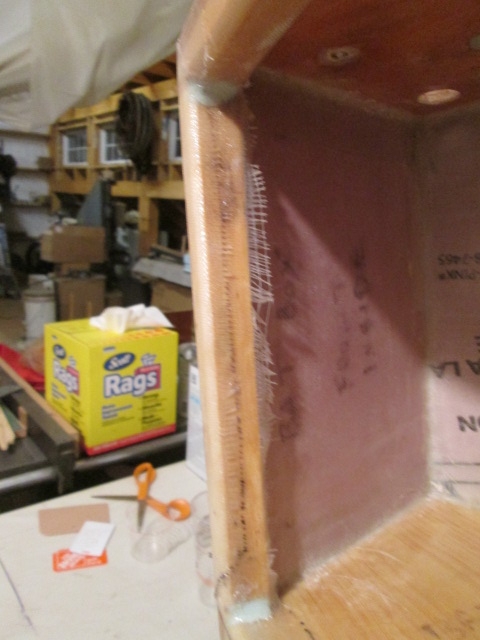
Here at the front on the top rim (down in pic) you can see the 4x4 wrapped in stretch wrap. When I rolled the box onto its rim I made sure to slide it back so that the extra cloth pulled tight underneath and didn’t bunch up or lift. By propping it up this way and limiting the surface area of wet in contact with the plastic I hope it will all come apart easily later, not to mention that this gave me room to let the final back wrap at the sides dangle down until I was ready to fold and stick it.
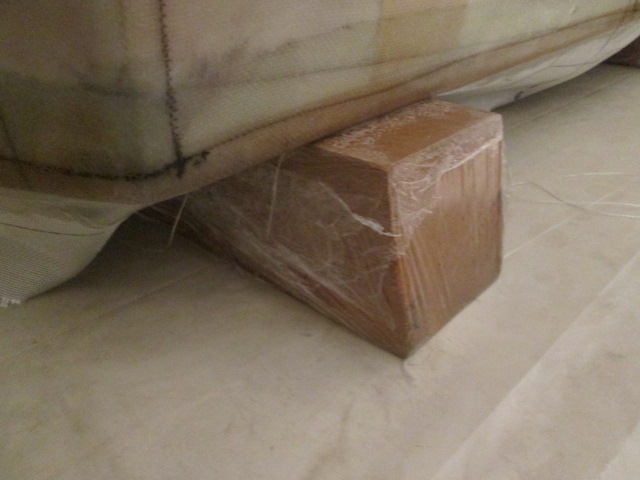
The flaps along the bottom edges ended up a little longer than I had intended, but it was easier just to lay it down than it would have been to try to cut a neat line as I went. This laid around the wire pull hole easily and covered the little spot where I had sanded the fillet thru to the spacer ply. I’ll trim the hole out again after the cure.
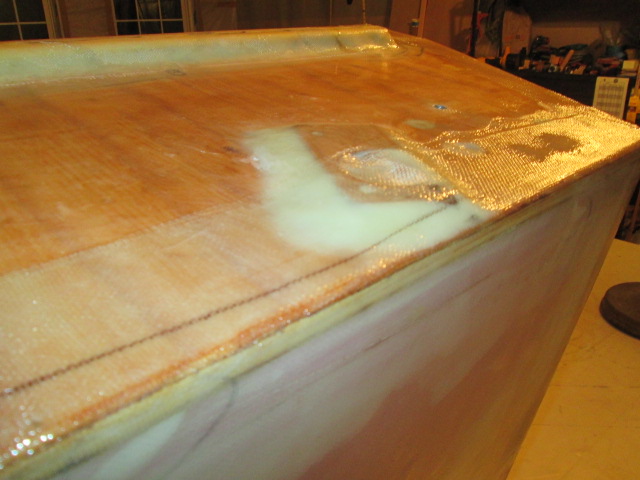
The lap at the corner went nicely.
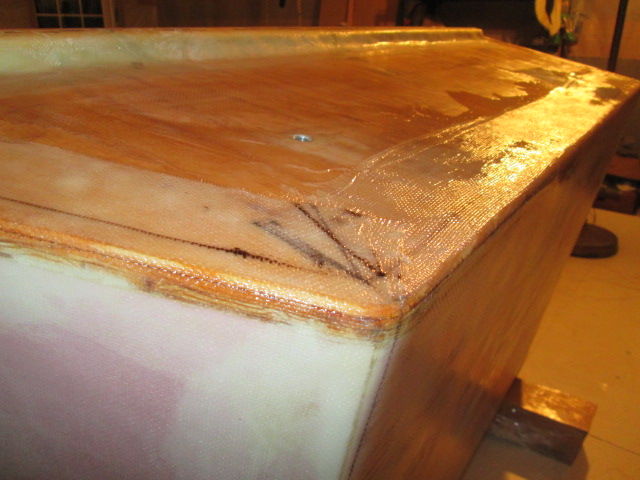
Wetting the foam first seemed to eliminate the small bubbles, or maybe it was the extra time spent fairing the front foam first.
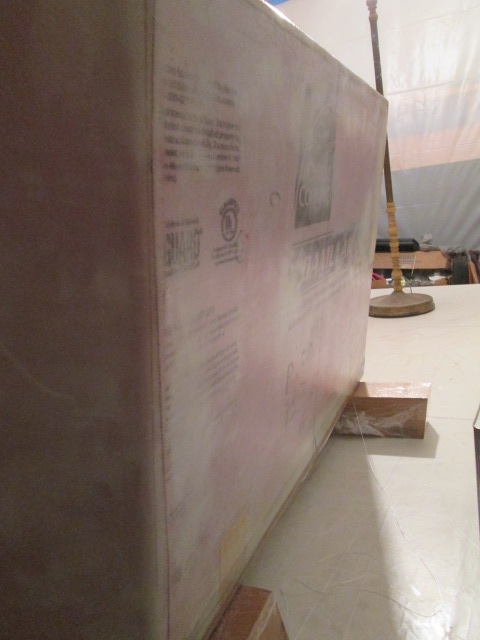
The street side (still upside down).
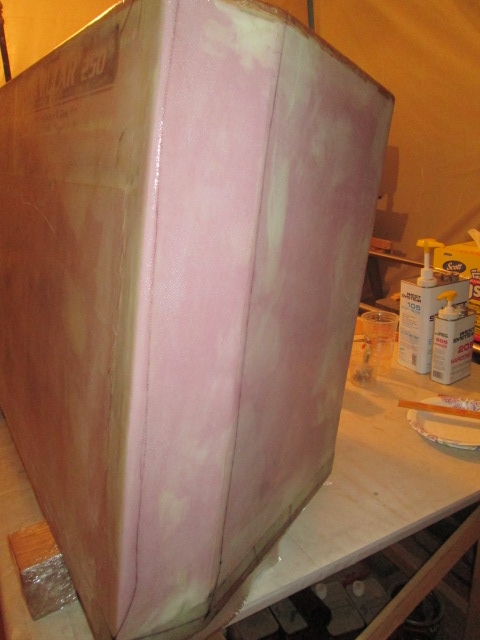
The top of the street side rear corner. My reference lines didn’t line up perfectly everywhere, ...this method is nowhere near as tidy as the PMPP method… but I had plenty of excess cloth around the perimeter that it didn’t create a problem. I know letting the fibers warp like this isn’t the best for panel strength, but I’m mostly concerned with puncture resistance, so let’s not over engineer things, okay?
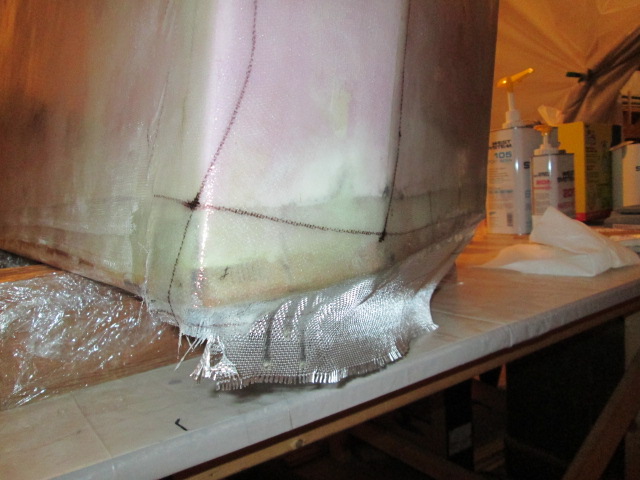
Curb side back corner wrapped (sorry, blurry pic).
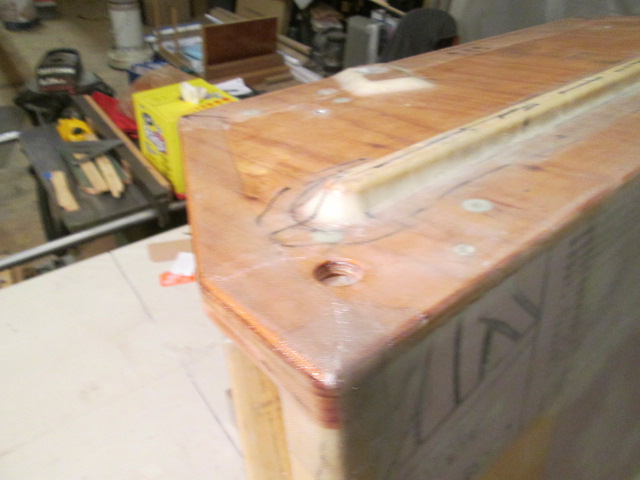
The little foam corner fillers and bias patches at the battery box opening worked great. Also note how you can still see the pencil line center mark for the flox filled Kregg screw hole under the much earlier layup inside of the battery box.
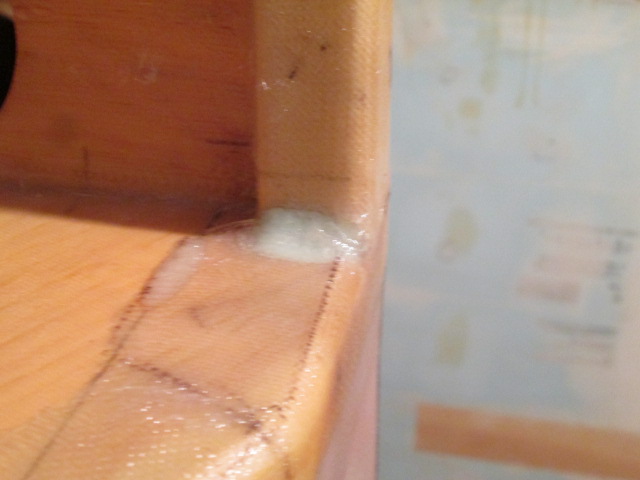
All in all I think it went very well. Hopefully everything will set up the way I left it without too many fixes needed.