It’s funny sometimes how when you reach a medium milestone it feels like you got more done in less time. Today was a decent sized layup, with about 5 hrs total time in the shop, but it felt like I got over the hump and onto the next phase of the build. I guess that is what happens when you work on all of the little things in preparation that lead up to a milestone, and then everything goes well when you take that step.
Anyway, started today by sanding the redo of the filler at the transition between the hatch edge sealing lips and the bumper; street side first then curb side.
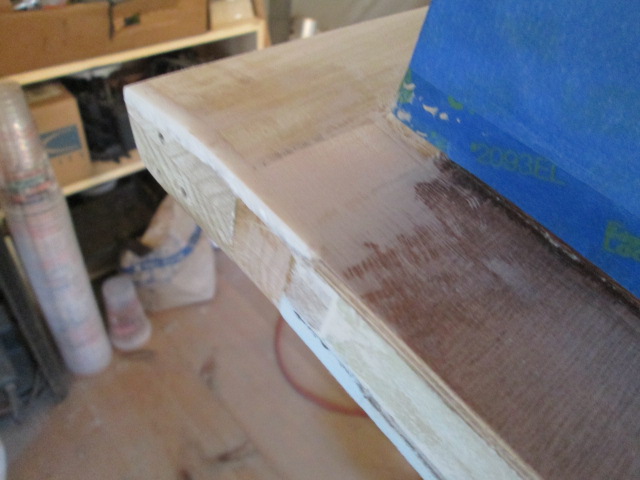
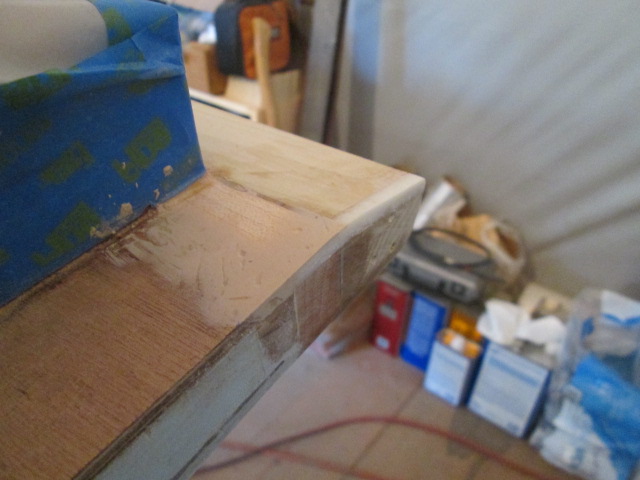
BTW, I have been meaning to apologize for the lighting in some of these recent pics. The floor lamp really helps me to see what I am doing, but it tends to cast shadows or glare when I’m taking pictures. I’ll try to be better about shading and/or moving the lamp.
The dregs in the pot from the failed filler episode were a little firmer today, but were still quite pliable compared to what they should have been. The stuff in the gap at the hinge spar to hatch inner skin rabbet joint seemed even firmer, but was still softer than what would have made me happy. Not wanting to take any risks, I drilled out the screw holes and used the cheap steak knife to dig out the gap. Flipping the knife up and using the tip to chisel and pry the gum up worked okay but was subject to slipping, so I wrapped the blade to protect myself.
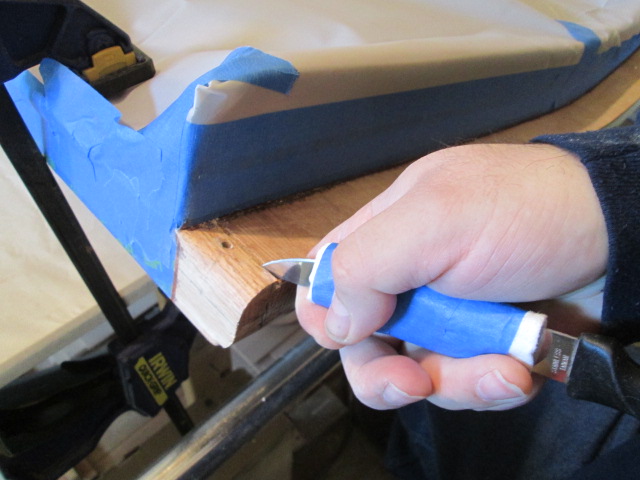
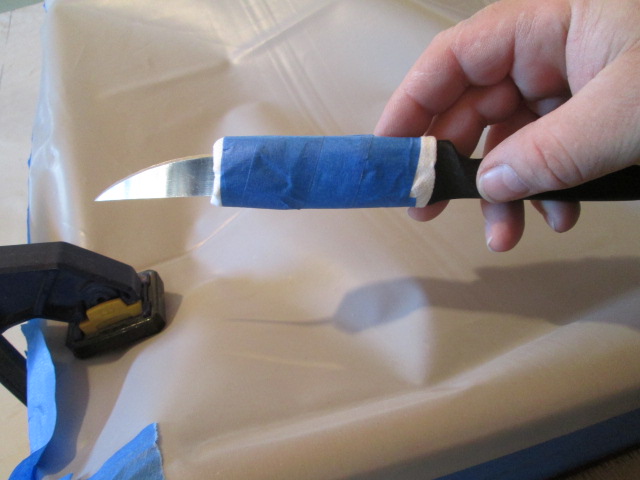
Once plowed out, dragging the tip of the blade back got down into the corners nicely.
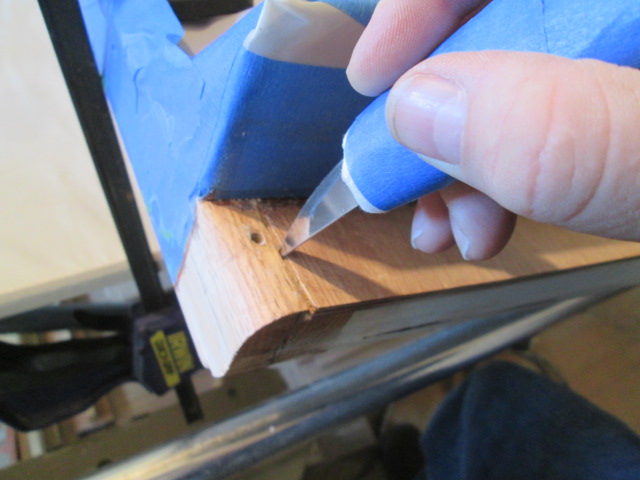
Here they are ready to try again; curb side first, then street side.
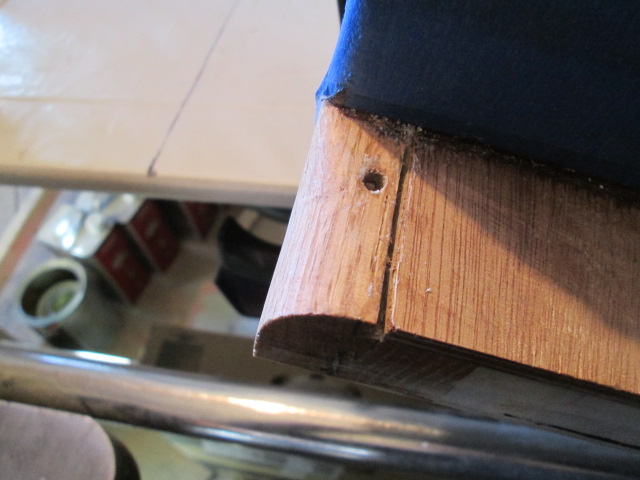
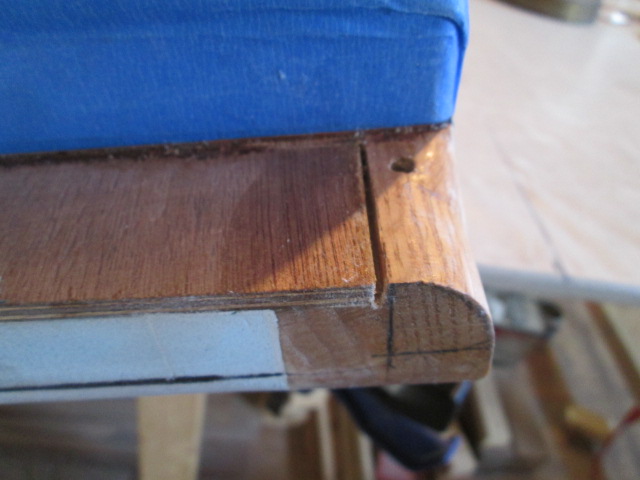
Again, wanting to keep things moving, I used about inch long squirts of the 5-minute epoxy and a dash of the 403 filler to fill this back in again successfully.
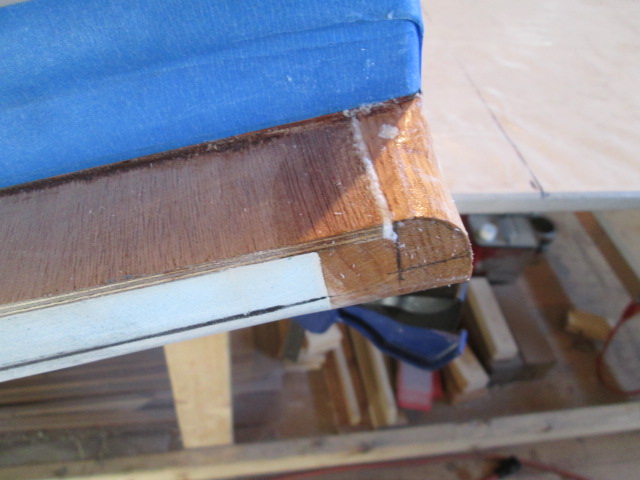
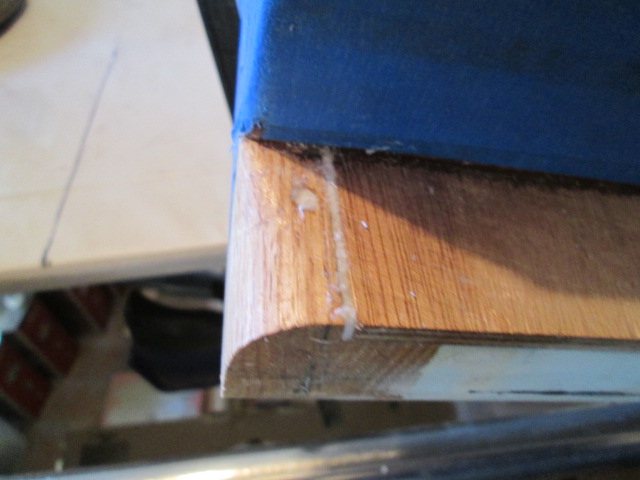
I’ll apologize again for not documenting the bigger layups better, but it’s hard enough to stay focused and work at a consistent pace without having to stop for photo op’s. The clock is ticking once the hardener hits the resin.
I’ll try to walk you thru it. First I pushed the hatch as far to the left of the bench as I could, even turning it slightly to get a long enough stretch along the front of the bench to string out the PMPP setups for the sealing lips and bumper. I had originally thought that I would wet out both then interweave the plies where they met at the ends of the bumper; but that meant that I would have to wet out both setups all at the same time and get them all cut out before any of them could be applied. So instead I decided to do the sides first, and then lap the bumper section over them. It just simplified things to where I felt a lot less rushed.
After taping the bottom sheets of plastic to the bench and laying the glass pieces out in position, I didn’t think and wet the three plies for the side lips all at once. With just two plies this has not been a problem, but with the third ply I had to work a lot harder in some areas. If it comes to this again I think I might do the two first plies together then lay the third on top. Not that it ended up being a problem, I just think it would have gone quicker and easier.
Wet out was with a credit card squeegee and cut down 2 inch chip brush. Then the top piece of plastic was put down and the medium Bondo spreader was used to press that down. Out came the scissors, cutting around the perimeter, then a clean cut down the middle to get the two strips, one for each side.
Set those aside for a minute and mixed up a one pump batch to wet the surface on the hatch, painting it on thinly with the chip brush and making sure to get it into the corners between the tape and hatch ribs.
Backing up a minute, when I started mixing the first batch of epoxy today I paid particular attention to the pumps and check weighed everything. What I found was that the hardener pump wasn’t coming up all the way by itself, so I made sure to pull it up the last bit by hand on each stroke, and checked all batches on the scale. (This could not have been the cause of the problem with that little filler batch, though, because that was a weighed batch and wasn’t even a full pump stroke anyway.) I’m getting toward the end of this first gallon, so I will be watching this closely lest I run out and not get a full stroke. That will also be a convenient time to clean the pumps and make sure they are both running freely (… if not before).
Okay, then I peeled one layer of the plastic off. Starting at the bottom of the hatch while holding the tag end up like a snake, I placed the end of the strip just above the lower radius of the bumper and started pressing it down. When I realized it was sticking to my glove, I noticed that I had started putting the plastic side down. DOH! No harm, no foul. Peeled it right back up no problem, flipped it around and started again all the way to the top. With the top plastic still on it was pretty easy to position and shove the edge of the glass right up neatly to the rib. At the top I wrapped straight around the front of the hinge spar and trimmed most of the excess off. I had to be careful peeling the plastic. First, with the multiple strips required for the length, when I got to one of the butt seams the next piece would want to come with the plastic. It is better to go slowly and catch that right away, peeling the lifting ply off of the plastic and laying it back down before too much comes away; it stays neater that way. Second, sometimes there are little scissor jags along the edge of the plastic and if these catch a string of glass along the edge it can try to pull a thread and lift the edge of the glass. If you go slow and steady and pull the plastic as straight back on itself as you can, you can catch these small things and keep the wet cloth down were you want it to be.
Here is the street side of the hinge spar with the glass lying down very nicely over that transition area I spent so much time blending. Nice!
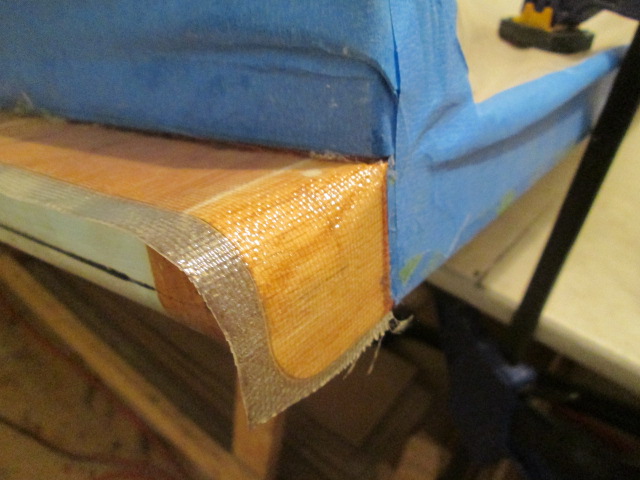
The second side was a repeat of the first.
Once I had the bumper PMPP wet and cut out, but before peeling any plastic, I could fold it up and make room to position the hatch so that I could walk around the bumper end again. Another one pump batch of wet painted on the bumper and it was time to peel the first layer of plastic. I started at one end and laid it according to my reference marks pushing the edge up to the maple sill. The credit card squeegee was used to press against the outer plastic ply to bed it down into the wet on the front and underside of the bumper. At this point I repositioned the hatch again, rolling it up on the upper part of the radius and away from the end of the bench enough that I had a place to stand. I didn’t really clamp it down hard because I was concerned about damaging the foam, but rather just hooked the clamps under the edge of the bench and over the spar, letting gravity and rocker do the rest. (I had already seen some signs of the creases in the sheet I had placed underneath as a cushion causing dent marks.)
Then I used the step stool to climb up on the end of the bench and wrap the rest of the layup onto the back of the bumper. Once it was all squeegeed down I peeled the top plastic ply off. In this ‘C’-shape, some areas pulled up a little, but it was easy enough to tamp them back down with the brush. I used the scissors to trim the outside edge of the front plies flush to the flox corner, made a triangular dart cut to fold the side end down (“up”), then wrapped the remainder forward from the back radius to the flox corner again. I’m pretty happy with how that worked out. There will be some final trimming and a little sanding after the cure, but I think it worked out very well.
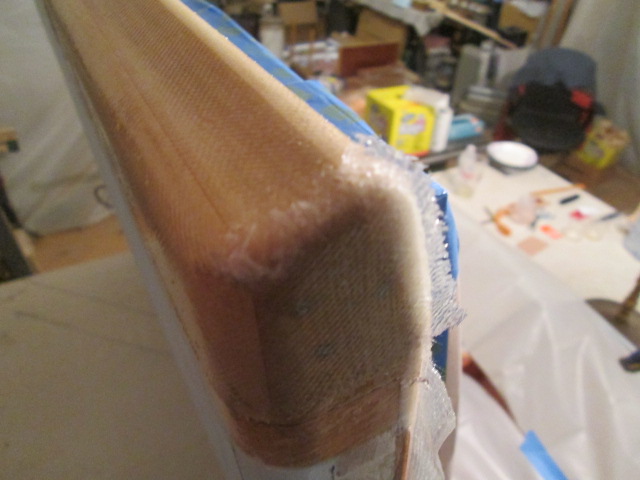
Here’s the front of the street side. You can see were the bumper plies (top) overlap the side strip (on left). In hindsight I probably should have trimmed back a few plies, or just butted the side strip down at the bumper line, so as to keep things more level; but I doubt it will matter much in the end. If needed I can sand and fair a bit with some of the 410.
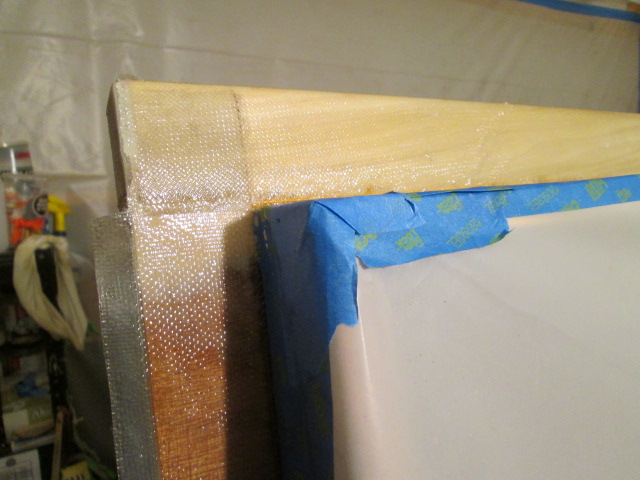
Here’s another look at the edge of the bumper showing the flap that will need to be trimmed later.
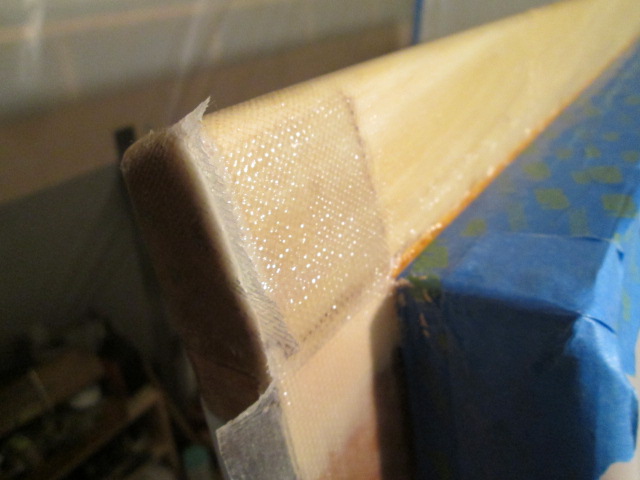
And the curb side.
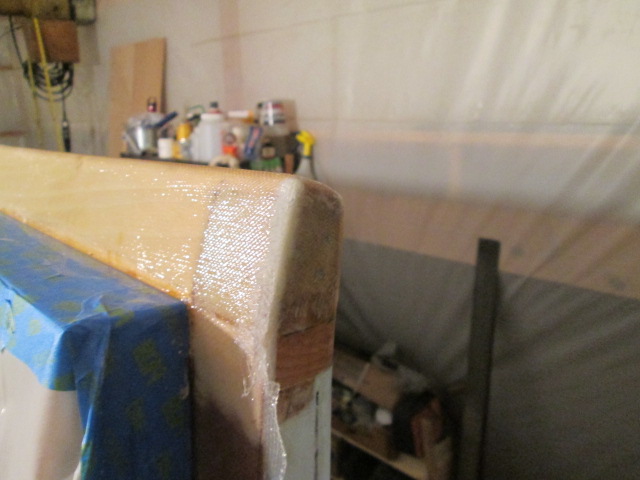
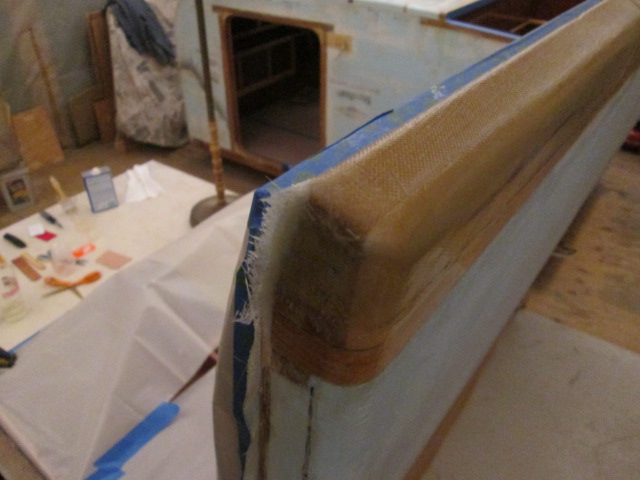
A close-up of the 3 plies on the street side edge.
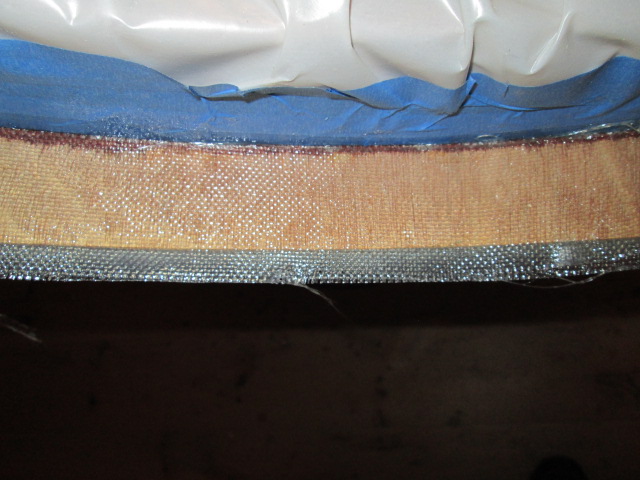
And an overall shot from the curb side for perspective, with the hinge spar on the left and the bumper in the air.
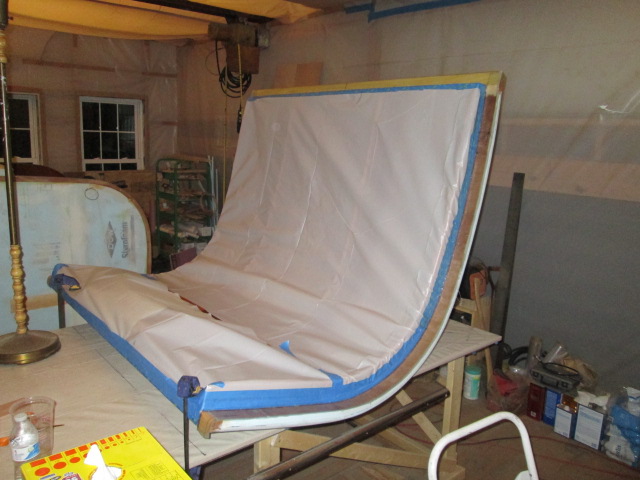
One thing I might have done differently would have been to try and stagger the bumper plies where they wrap up onto the back of the hatch. That way I could have butted the main outer hatch plies in a stagger and still have had some overlap. Now I will have to fair along the edge of this layup to allow the main layup to overlap; but in the end this might work out better because it might be easier to work to the edge of the bumper bottom radius.
I’m pleased with the outcome and it was a good productive day in the shop.
