That’s it. That’s the best I got. I’m at the limit of my fiberglass layup skills. It just doesn’t get any better than this for me, at least not without doing like the airplane builder guys and using a filler slurry for the base wet coat.
I have to put in a special thank you to Karl for sticking with me today and assisting. There were several instances where having a second person really helped keep things moving promptly, and I just wouldn’t have been able to place a sheet this big as accurately or neatly as we did.
Thanks to Michael/Atomic, too, for the tip about using two people to stretch and place larger sheets.
But I am getting ahead of myself. Today the weather was much cooler, about 50 degs F, so I could still use the fast hardener. It was a little drizzly out, but the hygrometer in the loft said 40/ct so I wasn’t worried about humidity.
After playing cobbler and gluing the heel pad back onto one of Yvette’s work shoes, I rearranged the bench so that I could get to both sides w/o the table saw getting in the way. Here you can see all of the support equipment for glassing at the near end of the bench and the PMPP for the front wall all laid out and taped down at the far end. It has actually been a while since I have done one of these, so I completely spaced out and had the larger 2nd ply on top, which would put it against the cabin first; whereas it should have been laid down first so that it would overlap the edges of the smaller first ply for a neater layup. Not to worry, I caught it in time to make a correction, but not until after starting to wet it out.
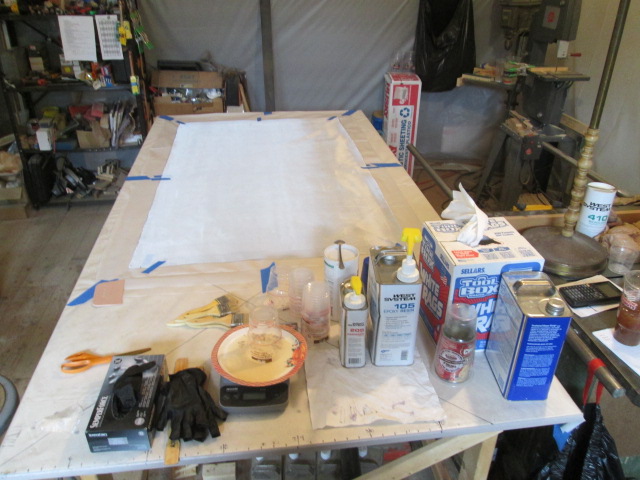
Another thing I forgot to do was fold a corner on each of the pieces of blue tape temporarily holding the glass plies in place. That made it really difficult to peel them back off of the glass once I had most of it wetted out and well stabilized. How quickly we forget.
Another little prep thing was to lay cardboard drip catchers on the floor around the work area. I didn’t drip that much this time, but there was one really big goober that I was glad landed on the cardboard.
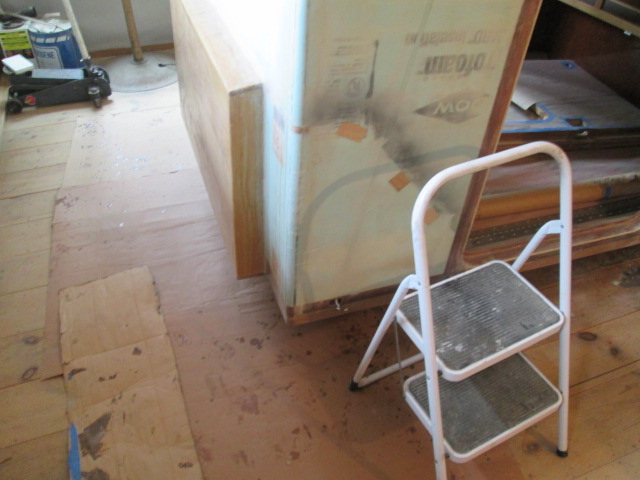
Once the epoxy started flowing the gloves were on and the camera lay dormant. This is where having Karl at hand really paid off. He was able to get out another piece of plastic, cut it down to size and squeegee it out on top of the PMPP; while I was able to stay focused and continue wetting out the cabin front. That allowed us to invert the sheets before peeling what started out as the bottom piece of plastic, so that the larger ply would be on the outside as planned, and saved time. It was a big help having Karl help peel the plastic off, too, while I tended the edges and made sure that none of the loose strands pulled away with it.
To wet the front I used a brush some, but mostly just poured the cup onto the brink of the radius and used the squeegee to trowel it fluidly down and across the front. The brush was useful along the edges, across the top of the locker, and along the inside corner of the fillet.
With Karl’s help, we got the glass with plastic placed exactly where I wanted it, squeegeed down and the plastic peeled off. After some more squeegee work, he ran the disc roller over it while I stippled with the cut down brush. Once we were pretty happy with it, we placed a strip of plastic (that I had cut earlier) along the stepped edges at the top and across the top of the locker. I figured that at the top this would help minimize how much sanding and/or secondary fairing fill would be needed for the next lap, and anything I can do to avoid sanding between cured glass and soft foam is a plus.
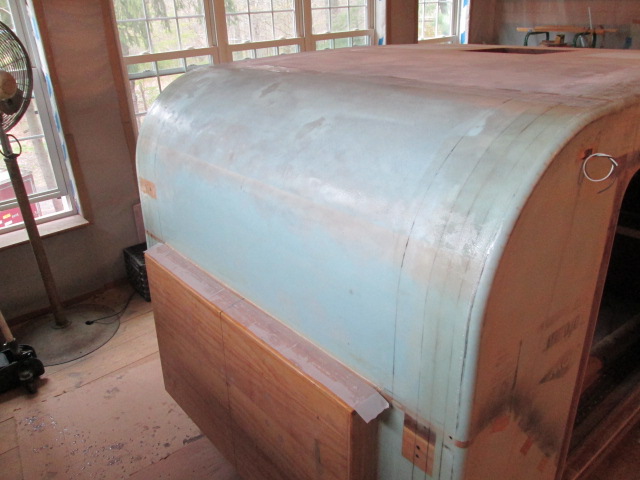
The 403 filler always seems to end up a little pock marked, kind of lumpy like potato salad, so despite having sanded the fillet between the front wall and locker top, I had gone back and forth trying to decide between having this layup extend down onto the locker top, or not. I had held the locker top glass back from the fillet and had the option of using the 2 inch tape in a separate operation. I could have also just mixed a little filler into the wet out here to help the flap bed in, but I’ve had problems with that pushing around and causing lumps. In the end I decided to let the wall layup run down and have the plies stagger on the top of the locker where it would be relatively easy to sand fair later. In hindsight I could have let this run all the way to the front edge, making it easy to sand back to the radius edge (more Atomic advice), but instead I decided to use another strip of the plastic peel ply technique.
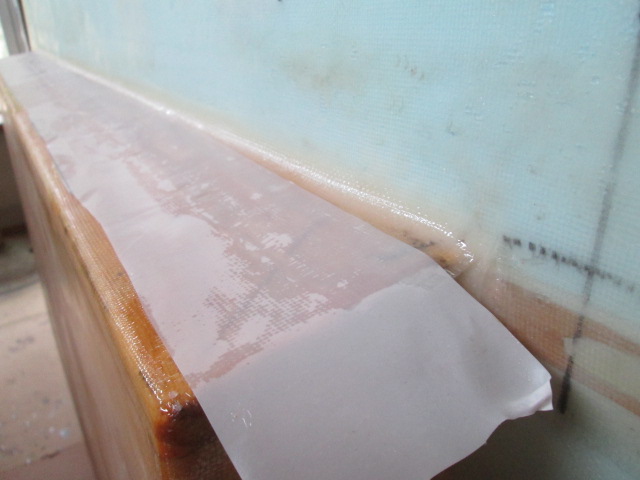
Here you can just barely see how the plies run just below the side sparette and are staggered by about an inch. Also, the peel ply interfered with adding the little patch to the corner of the locker, so I will do that another time.
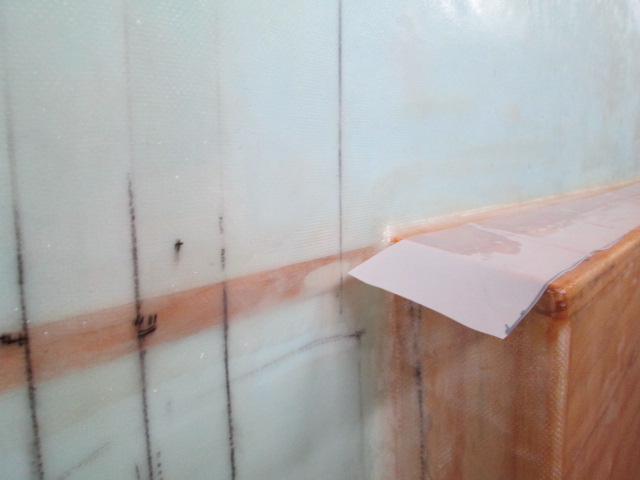
I couldn’t be happier with how the fillet turned out.
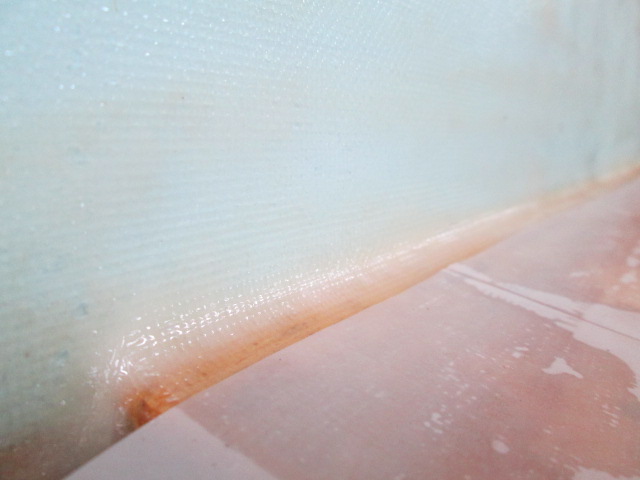
Here’s a better look at the plastic strip across the top of the front radius.
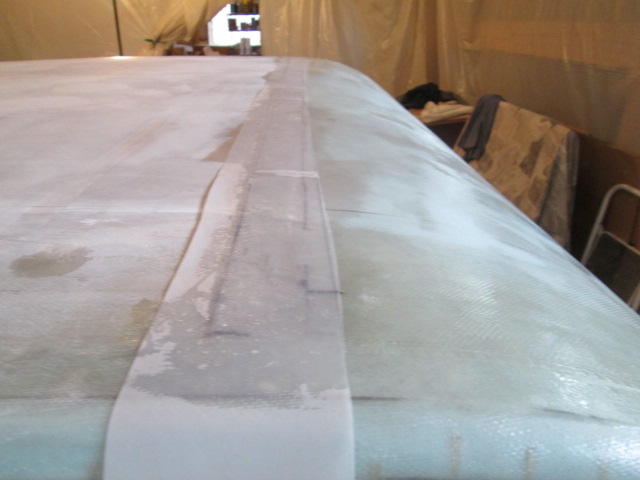
And a little closer overall shot. I stayed on the stipple brush for about an hour trying to get a few pesky air pockets (I like to call them “fisheyes”) to stay away, and probably got most of them; but once things start to really tack up that’s all she wrote and you have to walk away. I’m extremely happy with how this looks like it will finish up.
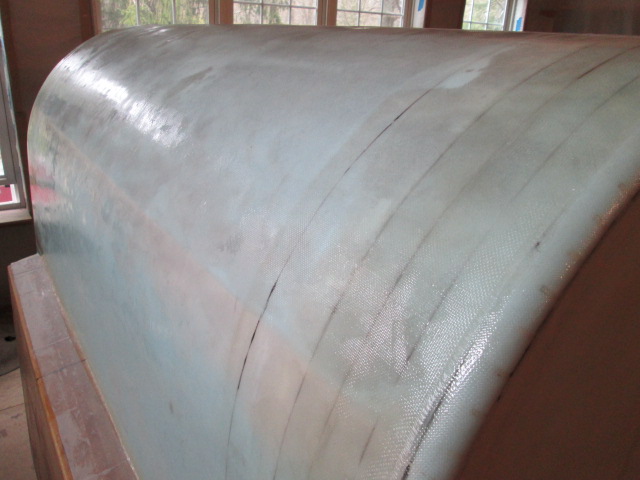
Again, my math said that this much cloth needed about 17oz of resin, plus hardener. Thinking back IIRC I did (2) at 6oz, (2) at 4-1/2oz, and (1) at 3oz for the bench top work; then another 2 or 3 at 3.5oz to wet the cabin. The math says that’s awfully rich by a factor of 2x, but when I look at the finished result it doesn’t seem to be; so I’m still good with it.
Later this evening the rain had picked up and the online weather said the humidity was up to 80/ct, but it usually stays drier in the loft, and it was well into kicking when I left, so I think it will be okay.
Choo choo train kept rollin’.