Thank you for your thoughts. Every scrap is valuable right now. I am still aiming for an aluminium/foam/ply sandwich though I am pricing fibreglass sheet.
Here is an update:
1. I have bought the 2” foam, below is a pic of it on my trailer.
2. I drove 150 miles to get the foam (our local shops sell teat cream, calving chains and culvert pipe but they don’t sell this) and took Ebi to the zoo while I was there. We camped on mattresses in the back of my suv overnight. Good living.
3. PLYWOOD THICKNESS. I am persuaded to use no larger than ¼” plywood for the internal lining. I haven’t the courage to go to 1/8th on a structure this size (12’x’6’x7.2’). The RV manufacturers are comfortable with 2mm fibreglass on each side of the foam. The internet suggests that a ply or wood strip hull can be half the weight of fibreglass. It turns out that the modulus, etc, of each is adequate but the ply and wood strip are more serviceable because of stiffness. On that view, light ply might suffice. I guess (could be wrong) that flexing is the enemy in a caravan as it will stress the joints; a ballooning side wall would pull the roof joint down and the floor joint up, and not gently. Using both thumbs and all my fingers to count, driving at 50 mph in a 20mph side wind when an semi-trailer passes could generate temporary winds of 80mph putting roughly 1500 to 1800lbs of pressure on the sidewall. (
https://www.physicsforums.com/threads/w ... si.364785/, but I am not joining arguments on this one, though you are welcome to have one).
4. AUMINIUM THICKNESS. The consensus out there seems to be that for stiffness, to equal half inch ply would take quarter inch aluminium ( eg,
http://www.millerwelds.com/resources/co ... s-aluminum). On the other hand the strength-to-weight of aluminium is probably (cannot find conclusive figures just now) the same as that of ply. Aluminium is two to three times denser than ply. I cannot imagine someone skinning outside foam with less than 3mm ply so I see no reason to go below 1mm aluminium (.040” to you) and should probably go above it, to be logical. This aluminum is structural, not decorative.
5. ATTACHING ALUMINIUM. The threat here seems to be heat expansion. the problem is more than “oil canning’ in that there is a danger of breaking the glue line and weakening the structure. The difficulty can clearly be reduced by lowering the temperature (by coating the aluminium in a light colour) and would be helped by using a flexible glue. But I have tested the substrate and the surface flexibility of the foam is plenty to allow the glue to move with the aluminium. On bending and stretching the foam, the compression and tension sides move more an 3/16ths” per 4” relative to the core. I would consider it highly flexible. Quantifying the problem, the long axis here is 3.5m (sorry, I will have to do this in metric), the coefficient of expansion of aluminium is about .000023 m/degreeC . On 3.5m between -30 and +50C there would be approximately 4mm of expansion. (That's over an 80 degrees C range). If I fixed the aluminium to the foam at 20degrees C, going to 60degrees C would expand it by 2mm or about 3/32nds” Thats enough to wrinkle it. If I use 4’x8’ sheets tall side vertical, three will do the width of a wall. A 1.5mm gap at each join should allow for any reasonable expansion across the whole. I can cover the slots with a 3mm thick, 10 mm high “top hat” or “bowler hat” extrusion fixed with VB tape or epoxy. Hopefully that would absorb the movement at its corners and, at the same time, restore some strength to the panel.
The alternative would be a single corrugation in the middle of each sheet. leave the corrugation unglued and movement in it would absorb the expansion. I might look into that. Can anyone think of a good way to put one corrugation into an aluminium sheet at home? Without a sheet metal brake, that is.
Another alternative might be to use galvanised and painted steel in a very light guage. The coefficient of expansion is half that of aluminium, the price is right and steel has a greater tensile strength than aluminium, weight for weight. (Or does it? I must look that up)
6. I am going to do some test panels.
Thanks, everyone.
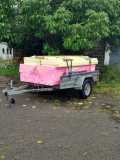
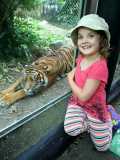
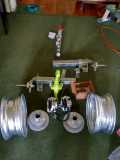
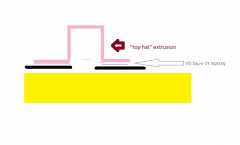