When we discovered we couldn't buy 3/4" thick foam from the big box stores here, but had to use 1", I decided to build a hot wire cutter that is long enough to trim the thickness. Place called Jacobs Online sells wire and transformers. This thing uses a light dimmer control and transformer to take 120 vac house power to something up to 48 vac.
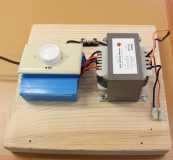
Since our requirements are for a ~6 foot long wire (much longer than most of the home made units I've seen online) I used something called Rene 41 wire, rather than nichrome. Rene 41 is supposed to be stronger and stretches less when hot. It sure is springy! It's a good idea to wear safety glasses when working with it, in case it gets away from one. I made a bow out of scrap wood
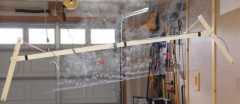
(The smoke is from a recent cut. I have little doubt the smoke is carcinogenic. At my age, it'll probably kill me when I'm 135. We opened the garage doors when we realized our peril.)
The wire gets longer as it heats, so to keep tension, I cut some slippery washers out of an old plastic coffee creamer jar, and used rubber bands to keep tension on the bow.
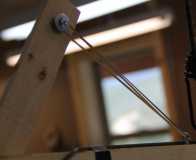
Shelly and I each got on one side of the bow. I'd previously marked inches on the frame on each side of each foam panel and called them off, so we stayed more or less straight across. The wire did drag a bit, and next time I'll make a point of going much slower. However, it did create a flat cut (not concave, which would have been a disaster).
It did a pretty good job!
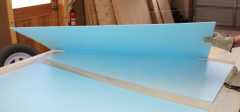
Unfortunately, our frame is not perfectly flat, and wire drug along the high points. I should have clamped it down to the bench before each cut. The result is that the foam was still slightly proud of the frame. I used 60 grit sand paper (finer clogs right up) to remove the difference. Hand sanding took it down faster than my palm sander; both made one heck of a mess!
Backing up a bit to when I'd cut the foam panels to fit in the frame in the first place, I wasn't satisfied that I could make a perpendicular cut with a knife, so I cut the foam large, and then trimmed it with a band saw. That works fine, so I'll continue to do it that way. An alternative would be to make another hot wire cutter, with the wire vertical and mounted on a table like a scroll saw. A short length of wire like that wouldn't need the big and pricey transformer, but could use a brick from some old electronics, or possibly a battery.
Next step is to try and find a place to store the hot wire cutter until it's next needed. Then to glue the frame and foam to the top of the floor skin. The less than perfectly flat frame worries me a little. We will have to weigh it down a lot to try and make it conform to the floor skin. We will also use Titebond III, which should be more forgiving of slight gaps than the PL product.
Steve Fredrick warns against leaving gaps in between the frame and foam, as condensation could get trapped in and cause rot. But how small of a gap is acceptable? I have a few on the order of 1/16" or so. No matter how well we did, there would be microscopic gaps. And then, there are knot holes missing from the C side of the plywood skins that leave gaps. Anyway, one thing I know about New Mexico is that it is less humid than the Adirondacks (where Steve built his teardrops). I'm hoping we'll get away with it.
Tom