We did exactly that on the two we built. We glued the door frames into the walls with clearance gaps (fixed side around wall opening, moving side around door, 1/4 inch gap between them), covered the whole thing with skins interior and exterior, and cut the whole thing apart. We used a 1/4 inch router bit with a plain nose like a bearing. It's a Freud 64-100 cutter. That plain end works fine but be warned it heats up fast and smokes like a chimney. But it followed the gap around the curves and did a good job.
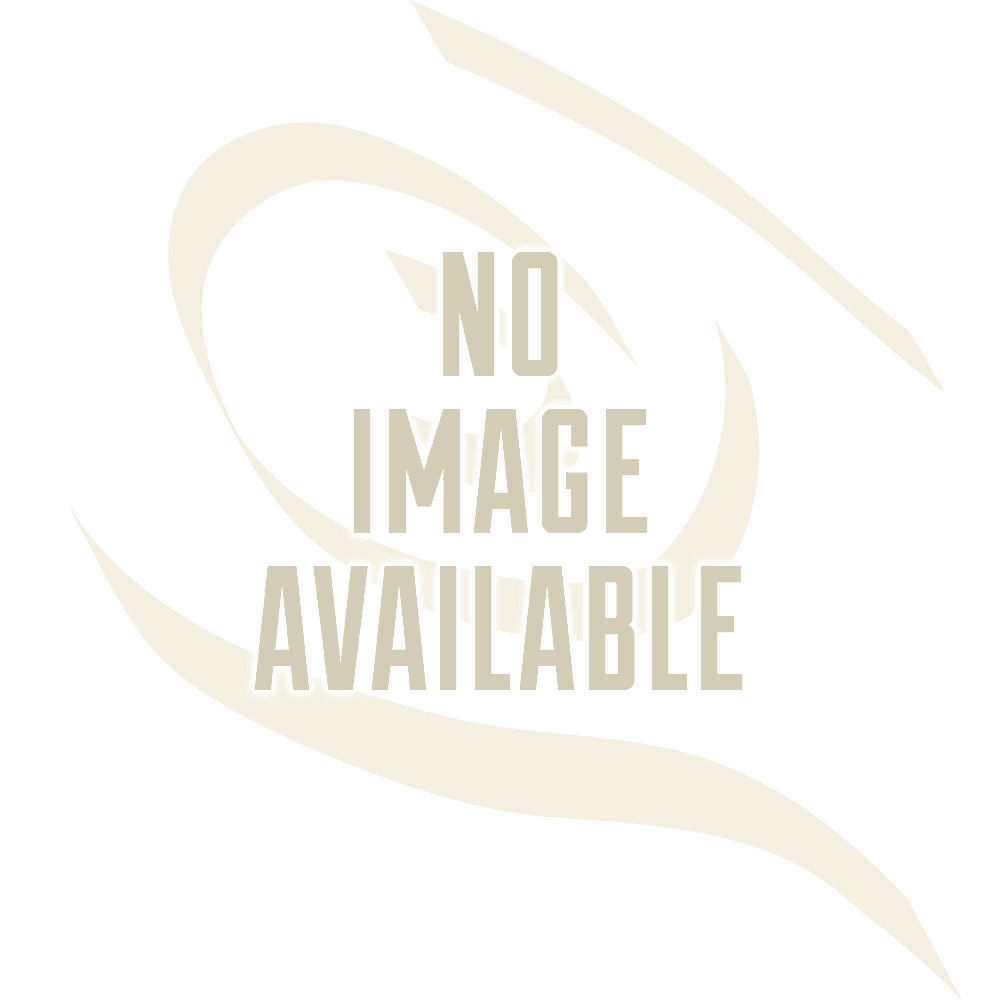
We purchased 1/4 inch router bits with a ball bearing end for this but the two we tried failed almost immediately. Seems like those teeny tiny balls and races just cant handle the loads.
Maybe somebody sells a good one but I couldn't find it. So we used the Freud with a plain end.
I found the technique nerve wracking. We had so much time invested into the wall panels with the embedded door parts it was a bit terrifying to think about losing it all and starting over.
But we did it and it worked. Twice. Notice the perfect grain match between door and wall, it's the same piece of wood. Notice that funny little squiggle at upper right, the door frames had that corner shape and the router bit followed it . Also notice the small defect at the 1 o'clock position. The fixed side of the door frame had a little gap between pieces of oak, and the router bit went into the gap and back out as we cut. We added angle trim later, that little notch is now hidden. The second trailer was skinned with prepainted aluminum, the router cut right trough it giving the same results as for the marine plywood.
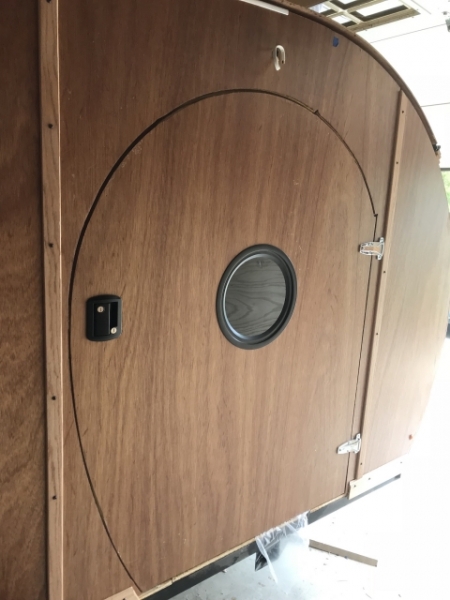