We have our gas struts in!
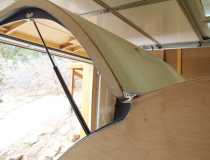
Really should have designed all this before starting the build, but I didn't, and after considering the problem, decided "reverse" struts" (where the attachment to the galley walls is above the hatch, when closed) works best for our design.
For mounting on the hatch, I picked the wide part of the gussets
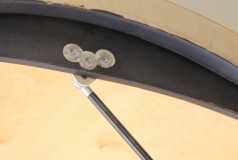
Only problem there is that I could have done a much neater job insetting the T nuts before building the hatch, when I could have used the drill press with a Forstner bit. As it was, I did the job with the Forstner bit and a hand drill, trying to hold it perpendicular to the gusset. Might have also made a jig. In any case, we plan to fill in around the nut with black epoxy. I also used some scrap 1/8 inch Baltic Birch to align the balls with those on the galley walls.
On the galley walls, the issue was that I didn't originally plan for hard points when I made the foam-sandwich walls. Solved that by running oak boards right to the bulkhead, and putting the screws where there is 3/4" plywood in the walls. I countersunk the screws far enough that I can add oak buttons later, although I realize that several would interfere with the gas cylinder. So...since these flip over from open to closed, can I assume the hatch will be open most of the time, and by flipping them over I'm really saving our seals?

This also gives us some hard points for the rear running lights to tie through the wall to, and the right one will give Shelly some wood to screw in hooks for hanging things.
On the left, I'll build our electrical box to fit between the oak and the counter top. Looks just right for the PD4045, a 120 vac outlet, 12 vdc outlet, USB outlet, battery switch, and meter. Inside the box there will be lots of terminal strips. I have yet to design this in detail.
To find the required strength of the gas struts, I modified (reverse engineered) Dan Lott's calculator. Instead of setting the prop stick near the center of the hatch, I set it a little further back, but I think I understand moment arms and correctly adjusted for that in the calculations. Then I reversed the measurements I used for the distance from the hinge center to the attachment points, since the short length is now to the galley wall, while the longer one is to the hatch. Anyway, I came up with only 35 lbs required per strut, with safety factor. Quite a bit less than would be required the other way around! But the lowest force I could find on struts in our length requirements (and budget) were 50 lb struts. So that's what we have.
They hold the hatch closed admirably. They do seem a bit weak holding it up, however. The next size up is 100 lbs, so we may try those, and send back whichever pair we don't want. So what happened? I'm speculating that it might be the fact that our struts are not nearly vertical when the hatch is open. For us mechanical engineering fakers, I think the missing quantity is a "cosine factor". Oh well, we'll get it right!
Tom