I haven't posted an update in a bit, but that doesn't mean I haven't been working...
Biggest developments include renting a U-Haul big enough to get my 5x10 sidewalls home. I figured as long I have the truck I might as well get my 4 sheets of .040"x5'x10' 5052 aluminum and any other 5' baltic birch I might need. So I made an afternoon out of it and got it done. I've kind of been dreading the handling of those big pieces so it's a relief to have everything safely in the garage.
My first stop was for 13 5x5 sheets of BB plywood - those would go on the bottom of the stack. Next stop was for the 5x10 CNC cut sidewalls (while precious - they didn't seem particularly fragile). And finally the 5x10 aluminum sheets would go on top of everything. Seemed like a foolproof plan...
The aluminum was pre-packaged on a skid or pallet - so I pointed out the plywood sidewalls and asked the operator to be careful when loading. Unfortunately (maybe he was distracted by my request), on the first attempt at loading the aluminum, the forklift operator bumped the corner of the stack on the back of the U-Haul. He proceeded to line it back up and start putting in the truck, but I quickly flagged him down and asked if I could inspect the sheets. As you could imagine, all 4 sheets were bent. I considered offering to take them at a discount, but unfortunately I have at least one area where I need a full 10' piece without interruption. Fortunately he went and grabbed me 4 fresh sheets without an issue. They were loaded "loose" with no pallet or skid. This made it easy to load and since I don't have a forklift at home was probably the best option for unloading.
While driving home, I started worrying about how I was going to unload the sheets without damaging them. I guess desperation breeds innovation (or whatever the saying is) and the idea of a simple cradle popped into my head. I made a quick stop at Home Depot to buy a few 10' sticks of lumber (another good use for the U-Haul). I thought I took some pictures of the cradle in use, but I don't seem to have them. Basically, it's a simple rectangular frame 10' long and 5.5' tall with a few cross-braces and a stop block on one end. I propped the frame on the bumper of the U-Haul and with the help of a neighbor we slid each piece of aluminum on the frame. Then I secured a couple of 2x4's on top of the frame to keep the aluminum from falling off when I propped the frame on it's side.
With all of that stuff safely unloaded I got to work on finishing up the tongue for the trailer. You can see in the pictures how I managed the tight welding access created by the composite A-frame tongue by adding a small wedge piece. This was actually cut from a scrap piece of 3x3x0.120 since the extra inch (all I had on hand was 2x3) gives a little more width for the MIG torch. I'm going to wait to do the final vertical welds in the narrow section until after I weld the tongue to the main part of the frame. Even though I had it clamped to the frame, it was already starting to pull the braces inward due to the heat from welding. Those inside corners are the worst for that phenomenon so I don't dare weld them until the braces are welded solid to the main frame.
I also added some tabs for mounting my battery box. I'll be using a somewhat unique approach to my battery and battery box... Hope it works!
-uberpixel
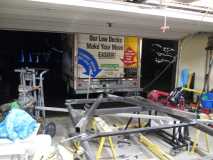
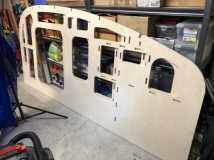
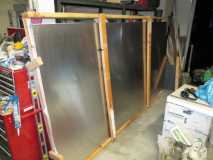
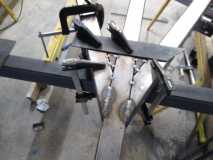
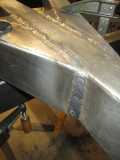
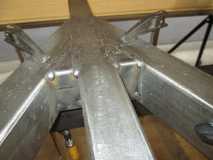
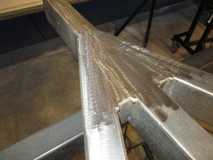
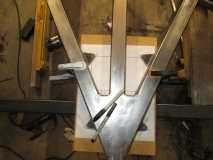
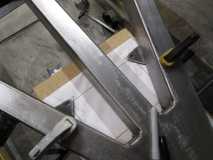