Our teardrop has about 20,000 miles on it now & has had
no problems structurally so far. The inner 1/8" Baltic birch skins were glued in place on a flat bench first, then stained & coated with urethane, prior to standing them up on rabbet joints along the floor panel's edges (with glue & drywall screws from the bottom & sides). The individual framing members along the side panels are used as "hard points" for attaching the cabinets, which were fastened from the outside with long drywall screws & glue, prior to skinning. The 1/4" galley bulkhead slides into a dado in the walls & floor (glue & screws again) and provides shear resistance from racking, as the hatch provides little resistance against twisting at the back of the box. The raw canvas covered headliner sits in a rabbet joint, then has the spars screwed in from the outside. The spars are glued in place against the top of the headliner, no nails needed here with enough glue. Red oak spars were used at the points where the solar panel & the hatch attach with screws, for better holding power than the poplar.
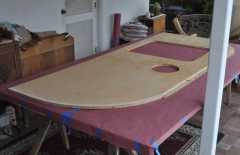
Once all of the interior assembly was done with drywall screws (headboard, footboard/entertainment cabinet, upper galley, counter, lower galley cabinet) wiring was run & foam insulation was fitted into all voids, walls & roof. Next the outer 1/8" Baltic birch skins were glued & stapled in place to finish the structural part of the walls & added to the roof spars to fully encapsulate the box's structure. If I were adding a roof tent, there would be more "hard points" in the roof structure, to accommodate loads (both static & dynamic) & distribute them down & into the floor & trailer frame. A walking surface needs more beef for tromping around up there, but it's easy enough to do.
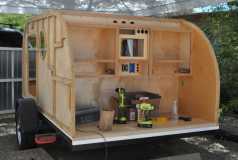
I think where people make mistakes in scantlings on a teardrop build, come from a lack of understanding in the strength of materials & how forces travel through members as loads are applied. A 3/4" plywood frame with inner & outer skins can be extremely strong, if it is glued together well & fastened at the edges into a strong structural box. Forces are moving into & out of the skins, through the center webs, & out to the other side continually. You can't see this, but it's happening every time a load is applied (wind from moving, bumps from rocks, leaning against a side, sitting on the floor as you enter, etc). A simple rabbet joint at the roof & floor allows for good glue bonding & solid mechanical fastenings from 2 different directions.
A roof truss system in a house can use 2x4's which are 2' apart for the top chords, with 1/2" plywood as the outside skin for walking around. This can be reduced to 3/4" trusses placed 1' on center with 1/4" roof sheathing (never done in a typical building, this is just an example). I guess you could use 3/8" trusses on 6" centers & 1/8" Baltic birch for the skins for walking around on the roof if you wanted. Remember, there are wind loads, snow loads & mechanical loads all applied to the individual members which make up the house frame. This is a weird example, but it's making the point that if things are done correctly, you can use less material & save weight to have a strong box to sleep in & tow behind a vehicle.
My point is that the 3/4" plywood frame with 1/8" skins is plenty strong for a regular teardrop if attention to fastenings & details are done properly. A roof tent is just another load to be figured out, but we already have roof vents, solar panels & other stuff attached to a teardrop, so why not one more thing?
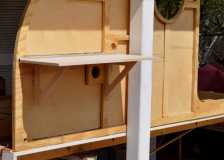
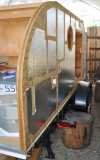