I needed to recess the windows into the foam a bit, since I can't mount them on a 1" wall. The first thing I tried was a $20 hot knife from amazon, the kind that looks like a sodering iron. That worked. Really badly. The blade gets too hot where it joins the handle, and not hot enough out at the tip. You could probably cut 1/4" foam with it, but it's no use for cuts this deep.
Take 2. I tried one of these, cheap chinese foam cutter, $27:
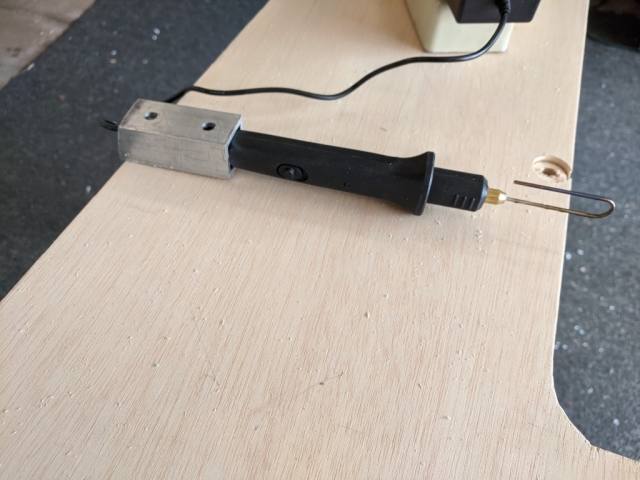
It has a straight long tip, and also a fork attachment with a wire strung between the forks. But this strange tip worked well for what I needed. Viola! Window recesses:
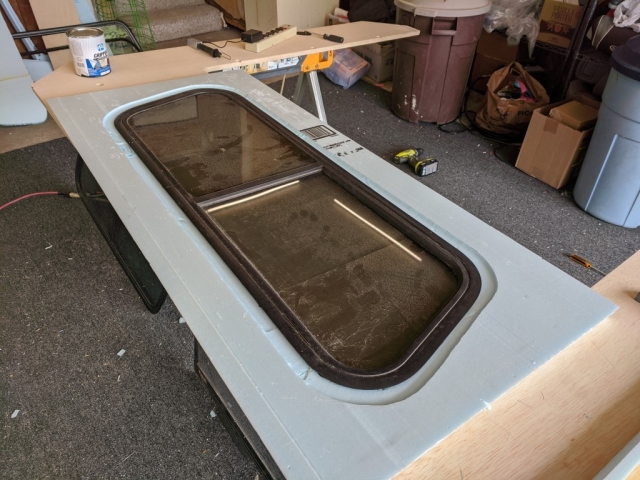
They were pretty good, but there were some issues that required some kind of filler.
What followed after this was a comedy of errors. First, I had bought some PL300 foam adhesive. I tried filling gaps with that. Although I had read somewhere that this stuff sanded like foam, I found that to not be true at all. It sands horribly. Here's where I tried to fix a nasty area from the first hot knife fiasco. This goopyness was impossible to sand down. It started coming loose, and I pulled it all out:
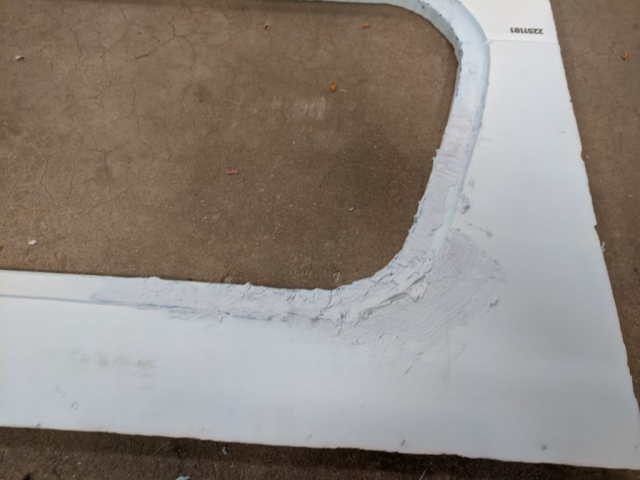
Next I read in a boat-building forum that dap spackle adheres fairly well to foam, and is easy to sand. So I tried using that:
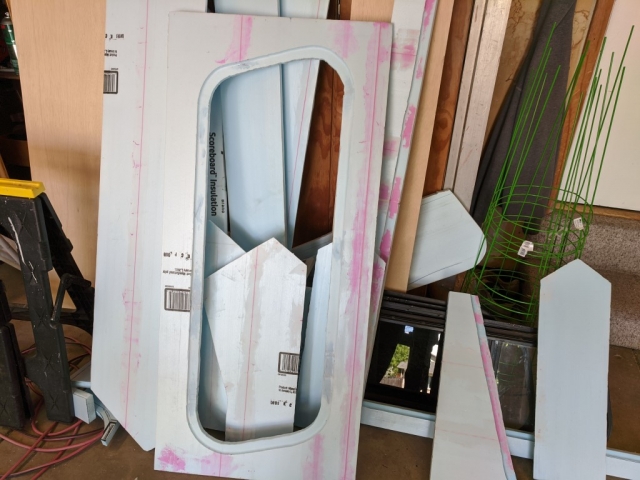
But as I was sanding it back, two things occurred to me. First, I can't imagine that the epoxy/spackle bond is going to have much resistance to delamination. Second, those lovely sharp recessed curves are nothing that fiberglass cloth is going to want to go around. So I needed to sand back the edges big-time.
So first I took the panels out to the backyard and hosed off all the spackle. Then I made a crude rounded sanding block out of a piece of 5" diameter pvc and started sanding back:
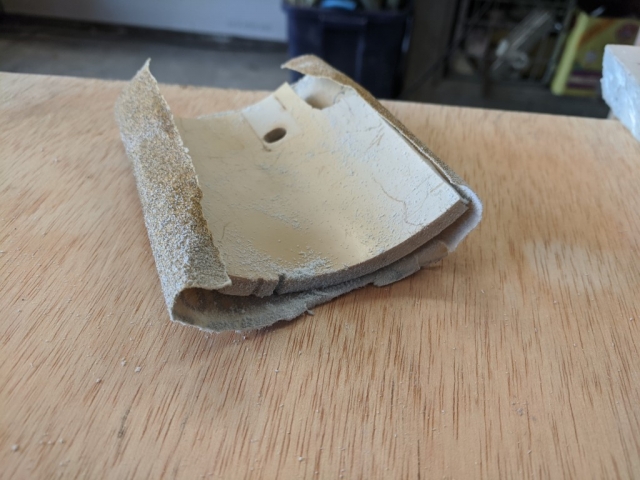
Although this was slow, and created a lot of dust (I spent more time vacuuming than sanding, just to be able to see what I was doing) it ended up sanding out most of the problem areas caused by the hot knife cutting. What I'm left with now is mostly pretty good, except for a few bad gouges.
Now for the gouges, I found a suggestion of mixing spackle with Gorilla glue. So I tried a test of a tiny bit of it. It expands like crazy, but it sticks really well, and it sands well too:
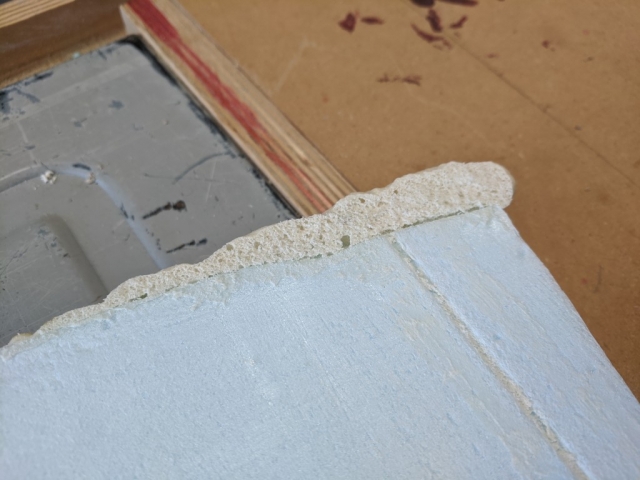
It looks pretty porous, so I'm thinking it might absorb a lot of epoxy, but at least that should make it adhere well.
So I mixed up a larger batch to do some filling. OOPS! Very exothermic reaction, and it set up before I could use a fraction of it. So I think I'm going to have to mix up TINY batches of this. Like enough glue to cover the bottom of a paper cup, and a 1/2 teaspoon of spackle. I did get a few things (over)filled:
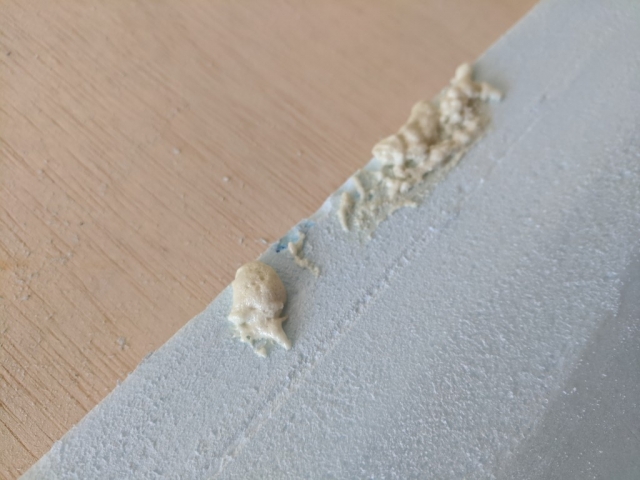
Which brings us up to the present. My current question is this. When I've been sanding around the corners of the window recesses, the foam has been pulling out like this:
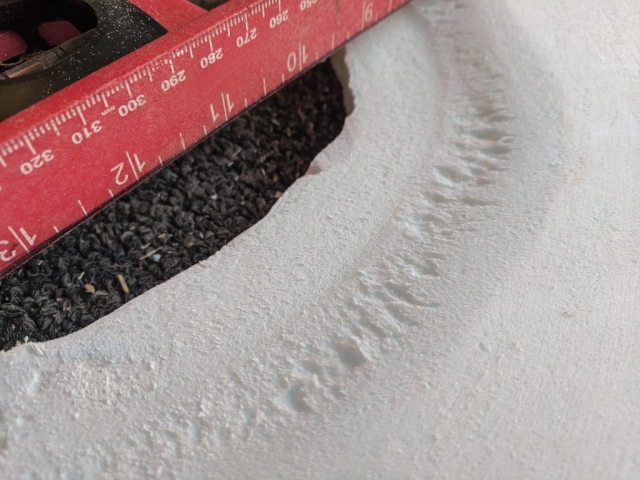
Who knew foam had so much grain?? but it really pulls apart around these curves.
Bearing in mind I will be doing surfboard-style hand layup of fiberglass here, should I be worrying about imperfections this size? The gorilla spackle works, but it expands so much there's still a lot of sanding left. And maybe these ripples will just help adhesion? I'm not nearly experienced enough to know.
And, even if these dips would show up in the FG surface, would it be easier to fair them after I apply the glass? (I'm hoping to get a weigh-in from some of the folks who have been around this block a few hundred times.... but otherwise, I'll go find the appropriate question forum and post there...)
A couple of other questions:
I have ordered 7.5 oz fiberglass fabric and Raka epoxy. I'm hoping to make do with a single layer inside and out, but could buy more and do another layer. Thoughts on the sturdyness of the resulting structure? I have also ordered some carbon fiber cloth. I read somewhere that it was actually more resistant to deflection than FG, and I thought of putting it on the roof, and the forward facing surfaces (instead of, not in addition to, the FG.) Anyone care to weigh in on that? It's not too late to change course at all...
My plan is to assemble first and then FG, since it's not just a panel with four sides. So I will have the issue of glassing a vertical surface. Any suggestions you can offer about working that way would be very welcome. I'm not sure whether to put a layer of resin on before putting the cloth on, and I'm also not sure whether it should be allowed to cure inbetween.... I've heard various things there. I am planning on building a tool to poke a bunch of wire nail holes all over it, to get better adhesion. I will also sand all the edges to be more rounded (and bullnose the bottom edge of the plywood with my router.)
Also, I've been trying to find some details about layup around windows. Wondering if I should just cut the FG off at the edge on the inside and outside, leaving open foam on the cutout edge, where it will be behind the window frames. Or should I try to get the FG to adhere to that inner edge by folding it around from the outside to the inside? And if so, should I round that edge too?
And of course, any other thoughts on the process would be most welcome. Thanks for reading this far!
cheers!
-eric