Here's how I reckon it's done:
You make the frame, then glue and screw the plywood to it.
So, you screw up into the floor frame through the bottom plywood.
You should seal your timber anyway, so your screws should seal up at the same time.
Then the whole lot is through bolted to the chassis.
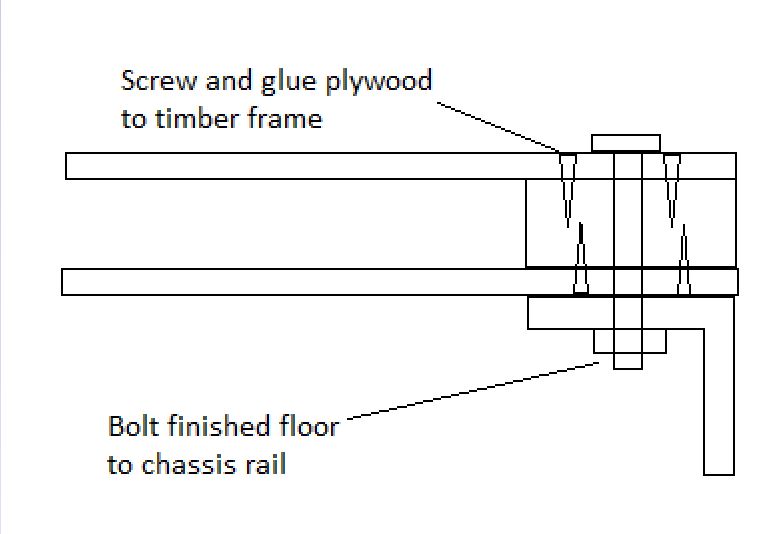
- Conventional floor assembly.JPG (40.69 KiB) Viewed 696 times
2 x 4's are pretty darn big though. I'm assuming it's under that size slightly?
e.g. we get a timber size which is 90mm x 45mm.
That equates to about 3 1/2 inches by 1 3/4 inches.
Basically off the saw it'd be 4 x2, but it is then dressed all round (DAR) to 3.5 x 1.75.
Going by what I've read in the generic Benroy plans, I'm talking about "dimensional lumber".
That would be a big timber for that job. Way oversize for a conventional 8 x4 or 8x5 teardrop in my semi-informed, but worth no more than anyone else's, opinion.
Especially with 1/2 inch plywood top and bottom. Unless this thing is a monster off-road ready beast, I think it would be much much stronger than necessary.
The next size timber down here in Oz is 70 x 35. That's roughly 2 3/4 x 1 1/2 inches.
It would be a 3 x2 off saw, the DAR to 2.75 x 1.5
That is what I used for the floor frame for #2, wide face vertical, with a single top layer of 1/2 inch hardwood marine ply. It's not going anywhere, and it does not sag when I get my 6 feet tall son to sit in the doorway area. If I were double skinning the floor, I'd probably try for even smaller timber and at least thinner ply on the bottom.
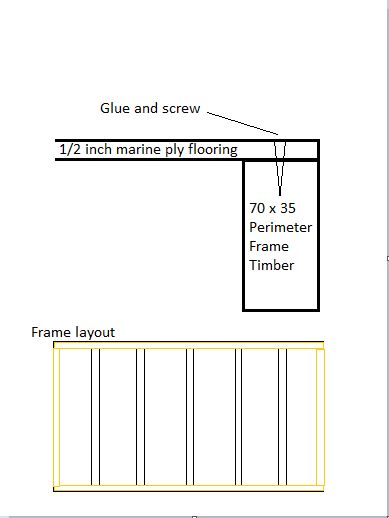
- Floor #2 build.JPG (27.21 KiB) Viewed 696 times
Of course, the only real reason to say your floor timbers are on the big side is the weight consideration. If the chassis is strong and the outfit has brakes, that's no biggie really.