So, it’s been a while. Life changes.
And some actual build progress.
Not sure if I’ve mentioned that the black Jeep and the Ford have been sold. I had been thinking about selling the Ford before things started going wrong with it… then, a month later, things went wrong with it. Electronic steering assist went out and, with some other upkeep issues, basically cost what it was worth to fix.
Since Yvette and I had been sharing the 2016 Hard Rock and enjoying it, I figured, why not get another one?
Dueling Hard Rocks.
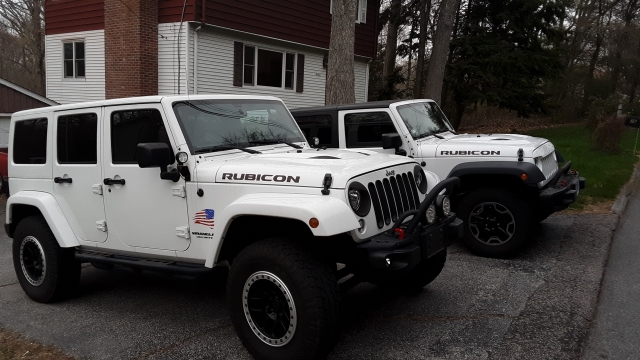
It’s a 2017 Jeep Wrangler Unlimited Rubicon Hard Rock Edition. Loaded with similar features and add on extras like the 2016. It’s an automatic with the semi-auto manual override feature (i.e. a slap shift feature that holds gears when in manual mode). It has larger than stock tires (285/75-17, equivalent to 33.8 inch tall) on MOPAR “Bead Lock Ready” wheels (the trim rings can be replaced with proper bead lock flanges). It also came with a full set of five of the factory wheels (which is how I found the for sale ad; I was looking for take off wheels to match the camper to the 2016). This one has the factory head unit with built in GPS (but no backup camera… will have to add one on). Has body color fenders and Freedom hard top, and came with the soft top new in box, never installed. Already has a receiver hitch and 4-wire trailer hookup installed. Anyway.
On the camper, last year at about this time I tried to get active again, attempting to address the blisters on the street side wall. I had some success, but not enough to fully quell my discouragement.
In the next pic, looking from the top of the wall with the edge of the galley to the left, you can see the lighter patch to the left, surrounded by yellowish/clear epoxy. This is one of the “original” blisters that I fixed by drilling a series of holes thru the outer FG skin using a drill stop; then hand twisting the bit in each hole down thru the foam until I reached the inner plywood skin; then syringed neat epoxy into the holes, palpitating to move the epoxy around; then weighed down a flat board with packing tape release. The excess epoxy oozed out of most of the holes (resulting in the yellowish/clear cured layer), but not all of the holes stayed full. The whiter colored patch is the result of skimming with epoxy fairing compound and sanding back.
While sanding this back, the two areas circled with red sharpie were discovered. More blisters. Now I can’t be sure if I just hadn’t noticed these before (? seems unlikely), or if they were newly developed. One concern was that they could be cropping up from the pressure of sanding somehow causing delaminations; but that doesn’t track when you consider that some of these blisters were springy/spongy before I drilled them, and then weren’t afterwards (as if some gas build up was making them puff out. In the pic you can see the circled area to the left that has been drilled, and the one near the batten yet to be drilled. The batten is aligned between the running light wire way at the base of the wall (top of pic) and the clearance light wire way at the top (bottom of pic), showing the wire path between them and where not to drill.
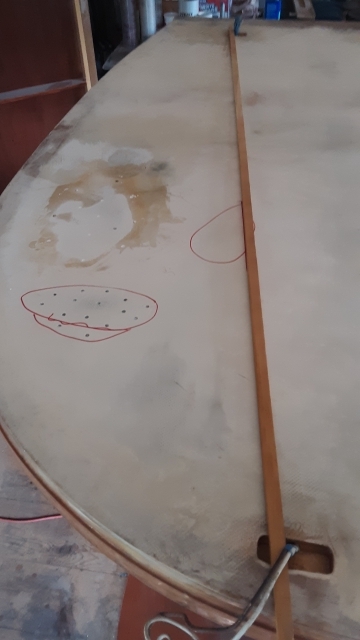
In this pic looking back the other way, with the sun, you can see how horrible the body work appeared at that time.
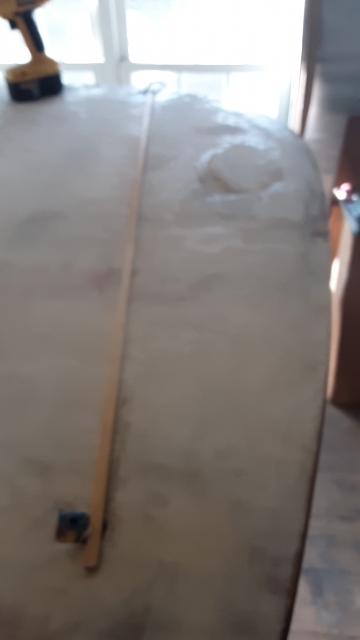
Here are the boards with weights trying to keep the blisters flat while the injected epoxy cures. Not totally successful, some oozed out and settled under the slightly warped board creating more opportunities to sand (will this ever end?)
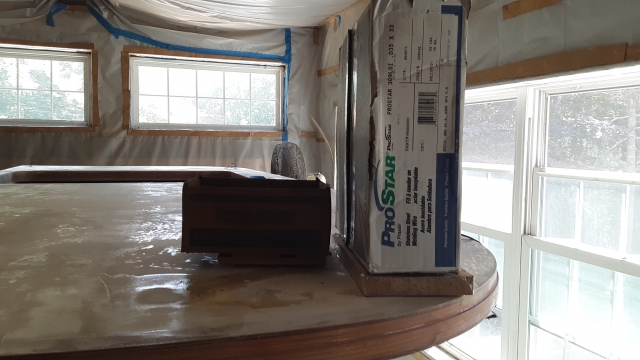
So while sanding that back fair and the rest of this general area, I found an area in the middle of one of the previously “fixed” areas, and another adjacent area, that were still soft/sticking up. You can’t just sand these areas because the blisters stick up; when you sand it the skin gets thin and you still haven’t sanded and faired the surrounding area. Discouraging.
I have a bunch of PTO (personal time off) saved up at my day job, so I decided to take a week off and just work on the camper, trying to get back into it and get “over the hump”, so to speak.
In the meantime I have continued to watch various Youtube channels of interest. One of which is “Tips from a Shipwright”. This old codger makes pretty good quality videos of his wooden boat building efforts. He uses a combination of traditional materials, including hand selected timber and custom mill work, as well as more modern materials and methods. One of the products he
demonstrated recently was Total Boat’s Total Fair epoxy fairing compound used to fill FG weave (at about 5:30 min into the video linky < ). This seemed like it might be a much better solution than the 410 filled West System that I have been using. Just mix the yellow part A equally with the blue part B until it turns green, then spread. Seems very forgiving on mix ratio… just eyeball it… is purported to adhere in all orientations without sagging (which is not true for the 410), and is supposed to sand easily (but they all say that).
Okay, I’ll bite. What else can I “load my gun with” for success? Many have advised that I use steel plaster spreaders. And, instead of hand sanding, switch to a pneumatic long board, referred to as a “file” in tha’ bis-ness.
So I got these.
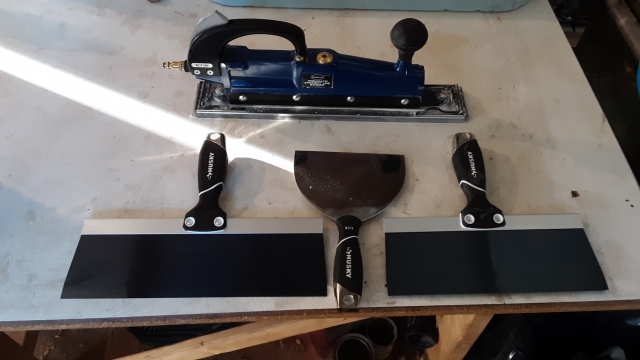
Strung two 50 ft air hoses together from downstairs and got set up this morning.
Now, most of the roof and the area behind the door on the street side have already been mostly done with the 410; and Karl and I had already laid the cabin over on its side to try and mitigate the sagging issue. In fact I was considering mixing a much thinner batch of the 410 in the hopes of it being self leveling. But I figured the hatch (which is curvy and not possible to orient with the whole surface horizontal) and the front wall with front roof radius (that can’t be turned up enough to lay flat) would be good areas for the Total Fair. If I like it I can use it on the curb side wall, too.
Anyway, rather than mix epoxy and try to fix the two small areas, then have to wait til it cured, I decided to try out the air file on the rest of the rear portion of the wall. Hard to see, but after just a few minutes work it was already looking, and feeling, much better.
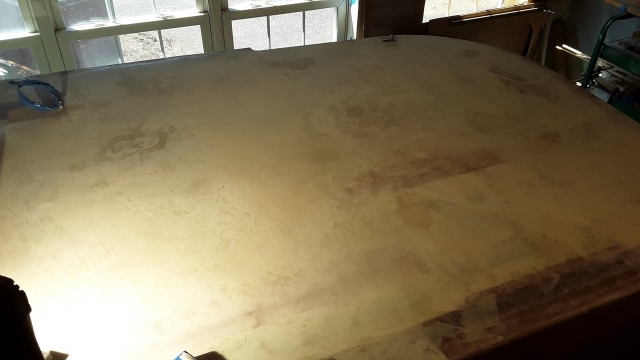
With the two tub vacuum setup I was able to put the separator tub up on the scaffold with me, but the power unit had to stay on the floor. After climbing up and down a few times to turn the vacuum on and off, that got tired; so I got smart and used a stick to reach the switch.
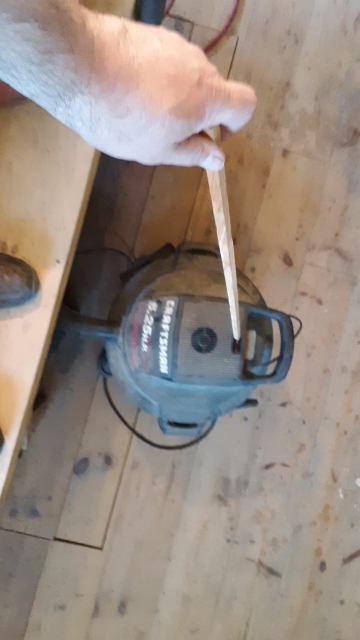
After a couple of sessions, only a few minutes each; followed by rest periods and vacuuming the dust (always wear respirator and goggles) it was already looking much much better.
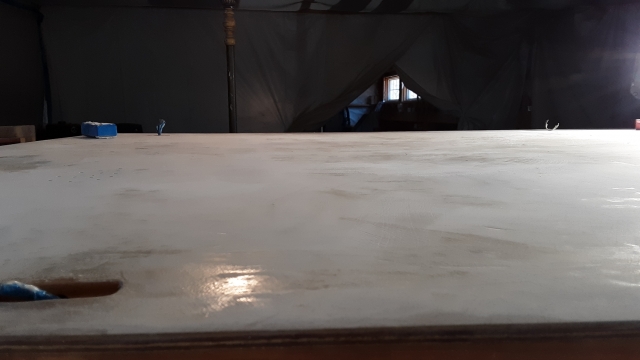
Prior to mixing epoxy, all of the low glassy areas of long cured epoxy would need to be scuffed up. I had a small square of that really course sanding belt (the fabric backed one that I got from Karl’s really big belt sander), but it was kind of stiff to just wrap around the small block, and my hands have gone soft from working a desk job, plus I needed a soft back to get down in the lows; so I wrapped a shop paper towel around, creased the piece of belt the best I could, and held it onto the block by wrapping it with masking tape.
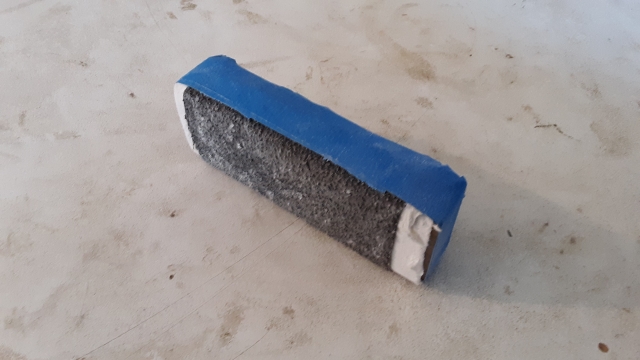
The shop had a visit from one of Karl’s customers. Karl helped
Tony Scalia develop a couple of his dress-up products for late model Dodge Chargers and Challengers. He drives a nice Hell Cat, worth a pic for those in the know.
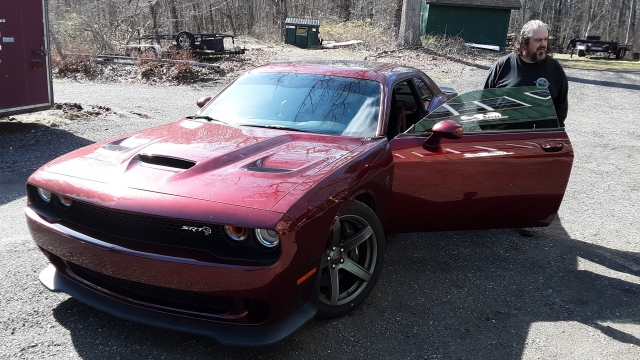
Karl got to go for a ride, but I was covered in white sanding dust and didn’t want to climb into the black interior. When they accelerated (hard) out on the main road (about a 1/4 mile away through woods) the thing sounded wicked! Karl said it was faster than anything he has owned, I presume including the Kawi 1100. He said it still spun tire even with the traction control on. Zowser. I looked it up, these are 10.8 second cars capable of top speeds over 200 mph. Double Zowser.
Anyway, I decided to try the “runny” 410 filler idea and, after squirting some neat into the new holes I drilled in the two small soft spots, I mixed up a few batches and spread it on using, mostly, the new 12 inch “knife”.
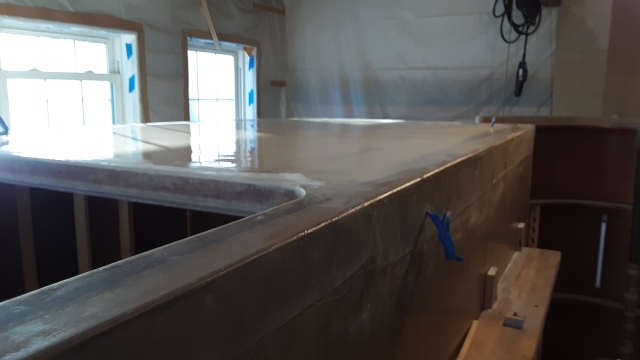
Tomorrow is another day.