Thanks Garth, hope you two are enjoying your build!
Mike,
Sorry for not being clear.
I have a friend that has a cabinet shop. I left a 16 foot by 12” by 2” piece of mahogany (plus a few remnants) with him over the winter along with my Template. He did all the milling and planing to get the thicknesses we needed.
1/2 inch thick by 1 1/2” wide pieces for the side radiuses along the roof line (see them taped to the edge in the one photo (there is a lot of waste when cutting the curves into a plank).
Then he found a thickness that would bend along the top edge of the template without breaking. That was 1/8” thick (It is important to have the grain running lengthwise on these strips).
He cut those 2 1/2” wide.
I epoxied the side pieces to the roofline and clamped them in position being sure they were at the peak or a touch proud. Once the resin hardened I sanded everything flush to the roofline.
I have a rock guard that extends about 24” up on the front of the TD. I started at that point for the pieces on the roof (see the hook on the ratchet strap at the front. I buttered them up then worked with the stack from the forward end as each travels a different length along the curve. I needed to use blocks of wood to force the end of the strips tight to the front wall). I staggered the length of those so the bitter ends fell in different locations and then the second stack was cut flush with the hurricane hinge.
Those pieces were 2 1/2” wide by 1/8” thick. 4 pieces tall and flush to the outside of the side molding raised the side molding to 2”
I hope I didn’t make this sound elementary as I know your work.
I should have included this photo…
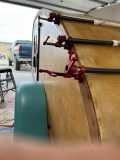