jerryf wrote:angib wrote:You're quite right, Jerry, that's a grey area. The 3/4" ply that forms the core of the sidewall sits on top of the edge of the floor and #8x1-1/2 woodscrews are driven up through the floor into (predrilled holes in) the sidewall.
Thanks Andrew. Well at least I read the design correctly. I usually try to avoid screwing into the face edge of plywood....but....OK, I could do that as described... if that's what Grant does, it gives me some confidence. Maybe I could add some glue might help too a little.
Hi, Jerry!
Looks like Andrew got you pointed in the right direction, but yeah ...
definitely add glue to the wall/floor/skirt joints! I use
Titebond II, but you might like something just as well or better. I do like Andrew's suggestion of using pocketscrews to help attach the skirts (finally, a place
I can use a pocketscrew jig in
my construction ...

...!)
jerryf wrote:angib wrote:Remember there is still an outer skin (ply, alum, Filon) to go over the joint.
I'll probably glue ply skin on the outside so that will help to strengthen it as well as hide the joint.
Yes, this design specs an overlay of 1/4" plywood that also covers the wall/floor/skirt joints, and yes the plywood should be glued on with an extra bit of glue over the wall/floor/skirt joints.
For the naysayers: I've been building teardrops like this for over 20 years, and have
never had a problem with the wall/floor/skirt joints (or any other joints for that matter) ... these puppies are rock solid! The icing on the cake is that the method is stone simple ...
jerryf wrote:Speaking of the 1/2" space between the metal trailer frame and the plywood sidewall, there is very little space between the outside of the tire sidewall and the plywood side wall in the wheel well. I don't know how much, but looking at your drawing, it appears to be 1/4" or 1/2". Isn't this a bit risky? Of course, I could cut it out and put a narrow and cool looking fender over it.
The wheelwell opening is one of those places where you are required to use your own "artistic license", as no specific wheel/tire combo is suggested ... you'll need to adjust as your choice in wheels/tires dictates. In the pictures, my "former associate" has used negative-offset wheels and shows a good portion of the tire outside the wall ... if he had used a more typical wheel with, say, a 6" wide with a 3-3/4" to 4" backspace (slightly positive offset), then the wheel & tire would have tucked inside the wheelwell quite nicely ...
Remember, these plans are simply guidelines with some specific shapes and dimensions ... the rest is open to interpretation and customization ...!
Good Luck on the build, Jerry! Remember, too ... you can always e-mail me, directly, with specific questions or comments about this design! As always, my friend ...
CHEERS!
Grant
Celebrating
Retirement after over
32 Years of Building, Promoting, Supporting, Supplying, Living the Lifestyle, and Loving
Teardrop Trailers!"Life Moves a Little Slower When You're On Teardrop Time"The nature of Life, itself, is change ...
"Those who matter, don't mind, and those who mind, don't matter." 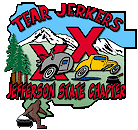