aggie79 wrote:As far as your layout table, two thoughts come to mind. First, is the melamine on both sides of the sheet goods? If not a single ply can cause an imbalance. Second, you really don't need truss joists to build a flat table. If you build a stress skin or torsion box and then install the melamine on top of it, you'll have nice flat surface.
Ah, that makes sense. One would assume I would have thought of that after spending so many hours contemplating the floor construction.
aggie79 wrote:What did you use for the core of the floor"
The core is Divinycell H45 (3lb PVC foam)
Here's a chart for the floor sandwich, based on 144 lbs/sf loading (1psi). The core fails at approx the same time as the skins will.
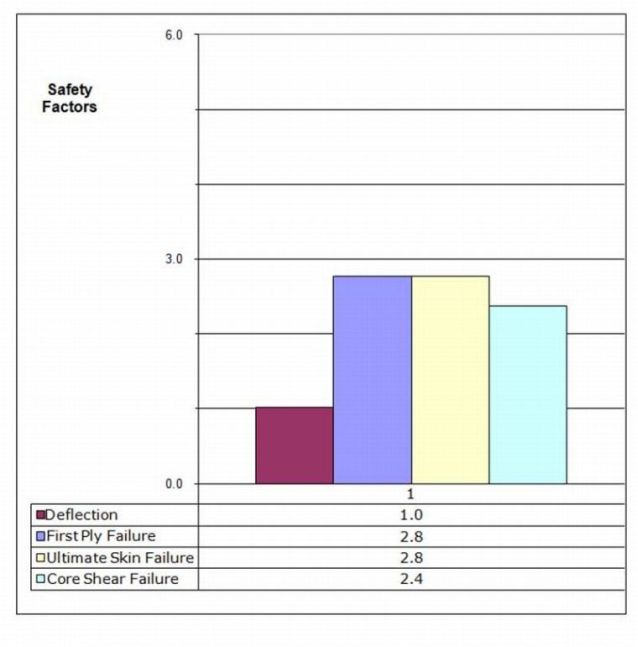
StandUpGuy wrote:2.5 gallons of resin just for the floor panel? I understand it is light weight and strong but exactly how expensive is it to do this floor panel? That is like a $100 of resin in the floor alone. Not to mention the infills and the cloth. Yikes! It is really turning out very nice, your floor panel by the way. I am just freaking out about the cost.
Well, is was only $80 for the resin.
The real cost is in the foam and the fabric.
There is no doubt that this is an expensive way to make a teardrop, however, it will last forever stored outside.
I'm shooting for
0% wood.
We've all seen the threads where people are encapsulating the plywood in epoxy and fiberglass. This is doing the same thing, just without the wood.
Oh, and there will be no frame under it, the axle will bolt directly to the floor panel with an "A" frame tongue.
So that is a $$ saver there too.
Trust me, the cost of these things keeps me up at night.
I'm always trying to find a better, cheaper way to do it, without compromising.
ohbugger wrote:Wow! Nice work on the fiberglass molds! All that work and materials for a plug, then a mold, then finally a usable part. No doubt the end product will be strong, light and it will look professional! Good work!
Thank you for your kind words!
I'm on a journey right now, and sometimes the road is hard to travel.
Everybody's complements and comments mean a lot to me.
More later,
Lee