No, GPW, it's 20 sheets of thin plywood, 5 mm or 3/16 inch. Sorry to jump back and forth talking about how easy the foam was to figure and how tricky the ply would (pun?) be. The foam is only 7 sheets of 1-1/2 thk 4x8 plus 1 sheet of 2x8; and 1 sheet of 3/4 thk 4x8, as mentioned previously. I think I can squeeze the plywood down some.
The problem with the plywood is that I have so many pieces that are over 60 inches long by over 1/2 a sheet wide, and all of the shelf/cabinet bottoms are long, too. I'm going to go and split the lengths of the shelves and cabinet bottoms in half (plus a bit for scarf joints... or maybe just in half for a fiberglass/epoxy reinforced butt joint), let the grain fall where it may on these pieces, and see if that utilizes more of the 43% waste that Max Cut said I would have.
I did rummage around in the Max Cut software some more this evening and found the "reports", or print out section. That makes it a lot simpler to figure out than the initial optimizer screen shot. Each different sheet layout (there are 12 of them) is depicted with the name of each piece in situ on the diagram and a table listing the sizes for each piece by name; how many sheets that particular diagram applies to (some layouts repeat for multiples), etc. You can even print labels to apply to the actual parts so that they're much easier to keep track of after cutting. Let me see if I can include an image...
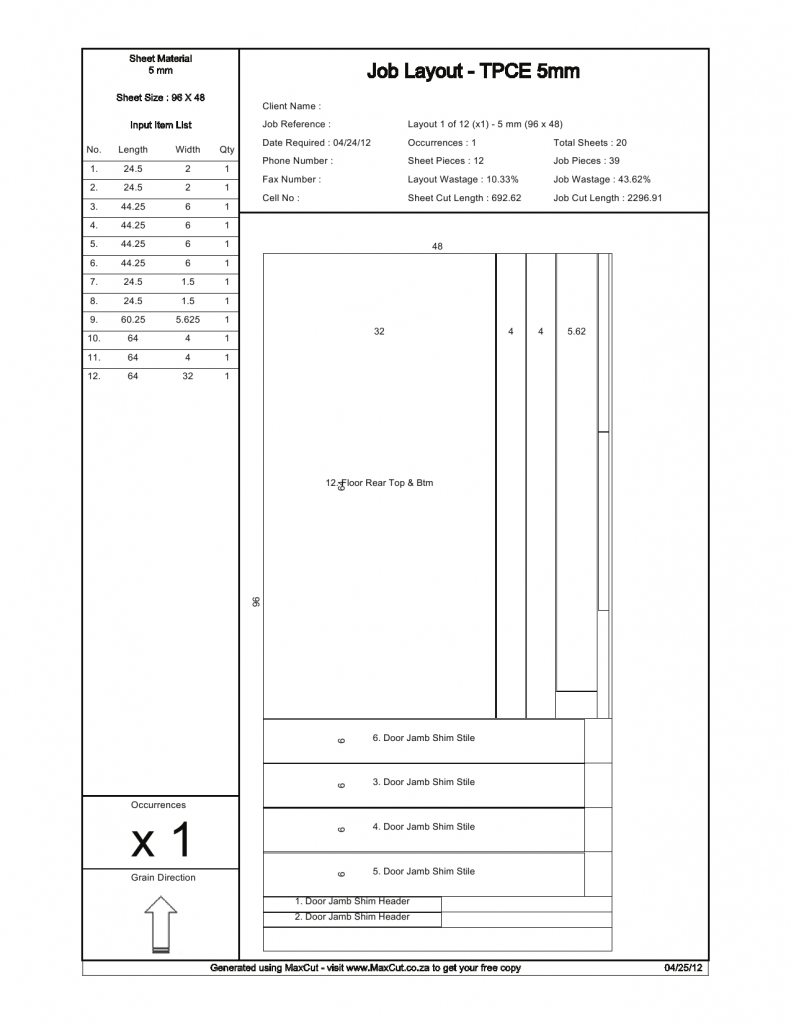
It worked.
This one isn't too bad. Most of this sheet is used, but there are only so many of the little pieces and every big piece needs another sheet. I want the grain of my walls to run vertical, but that isn't so much of an issue as all of the floor, front, ceiling and hatch pieces that have to span over 60 inches. There are at least eleven (11) of those that need to start with a full sheet. I was trying to avoid scarfing, but may have to take another look at that.
Hmm, maybe I can get "Rover" Mike to get one of his guys to push all of this stuff through his nice commercial table saw. That would make my time on his project worth it!
absolutsnwbrdr wrote:If I haven't said it before, you're fabrication skills are top notch!! Wish I knew my way around a metal shop even half as good as you
Thanks, Zach. I've been forcing my will on metal for at least 30 years now (damn, that makes me sound old

). Every time someone pays me a wonderful compliment I am left wondering about the skills that they possess and I don't. Everyone has the ability to be good at something! One thing I have always said is, "If you can show me how to do something, then I must be able to do it, too!"
eaglesdare wrote:I can't wait til the shell starts. Great job so far!
Eagle, me too! Thanks.