I was hoping to wait until the hatch was actually finished and installed (which I had thought would have happened by now) before I posted an update, but completion has been pushed out a bit because of the problems I am having with the fit.
The last time I wrote about the hatch I was attempting to correct the tweak in the frame. In order to straighten it out I clamped it into straight position in the teardrop (clamps on left side, and across the bottom) and then screwed a scrap of 1/8” plywood over the center span to hold it in that shape until I could get the interior skin on.
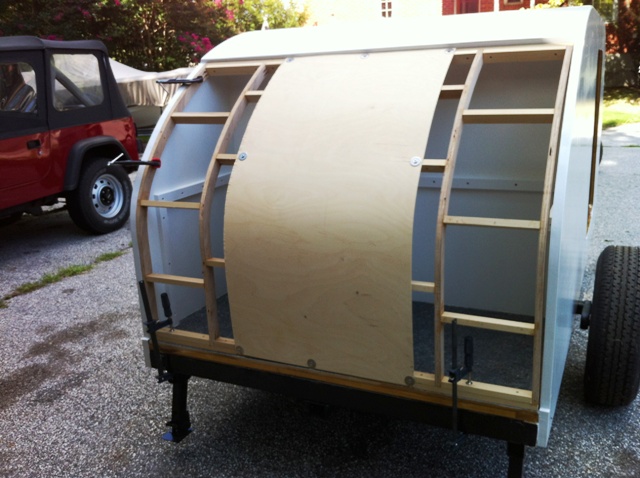
The interior skin went on fairly easily. Piling all that weight into the curve held it down nicely until I could get all the clamps in place. No fasteners were needed for the interior skin at all.
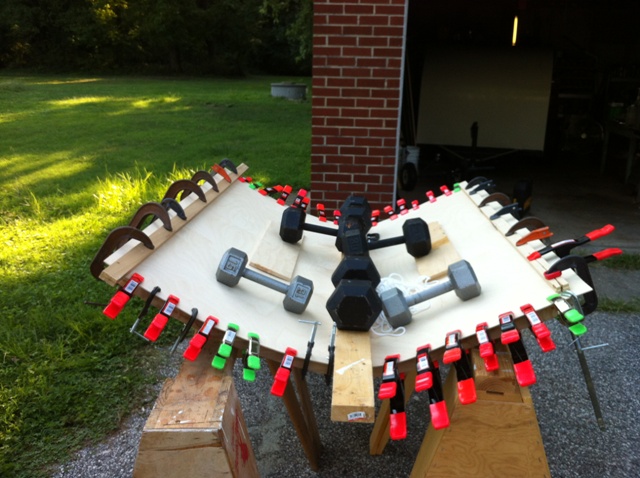
The skin was then routed flush and glassed with 6 oz. cloth. This seemed to work very well and the hatch fit much better at this point.

Insulation was added.
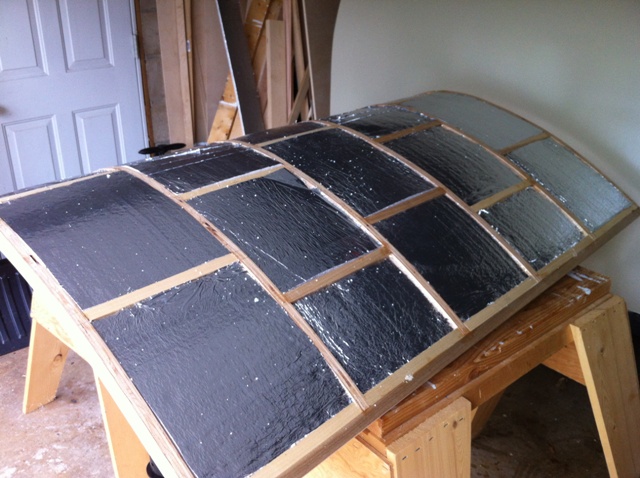
And then the trouble began when I got to the outer skin. Despite all the care and advance planning I did, it was a huge cluster from the very beginning.
See all my clamps and weights all organized and ready(??), so I could move quickly once the glue was on. Because the interior worked so well, I fully expected the exterior to go just as smoothly.
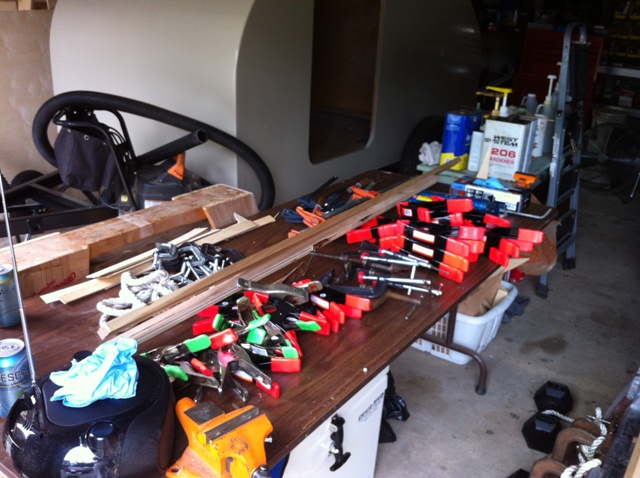
I got it bent into place, glued, weighted down and clamped…..
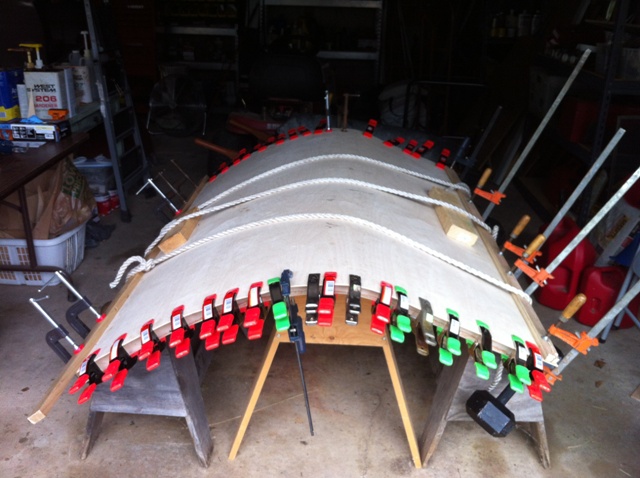
And then sat down in a chair next to it to enjoy a cold drink and admire my work. And while I was sitting there gazing lovingly at it I saw that there were big gaps between the skin and the frame in the area of the curve. I moved the big C clamps to that area but no amount of clamping was going to close the gap. Fortunately the glue was not fully cured yet so I worked quickly and got the skin back off. All that glue had to be scraped and sanded from the frame and the skin. Ugh.
(My thanks to Lance for doing that for me!!) It turned out to be a mixed blessing though, because once I had the skin off I realized that I had forgotten to add in blocks in the areas where I needed to put the lifting handle and the supports. So I numbered all the insulation pieces and removed them and installed the extra blocking I needed using thickened epoxy as the adhesive.
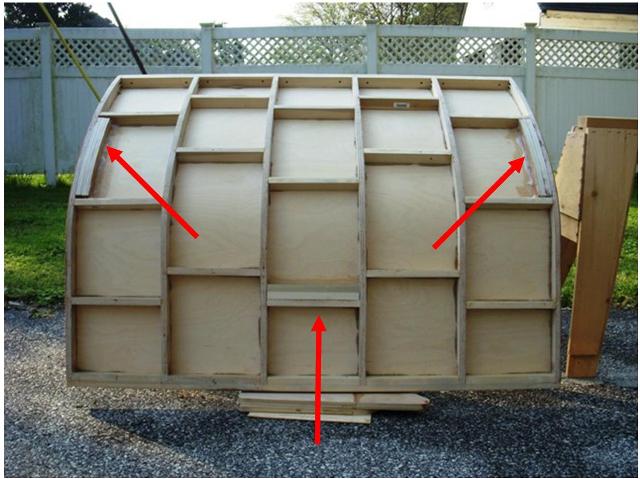
Insulation put back in and brace myself for another try. This time I decided to put the skin on ½ at a time. So I started at the bottom edge and applied glue only up to the very beginning of the curve. I had marked the location of all the frames on the outside of the skin and since I was dealing with just a flat area it was easy to get fastened it down with my pneumatic stapler. So far, so good. Now the remaining problem is only half as big. Divide and conquer.
I happened to be home alone the day I was working on this, so if I screamed for help there was no one to hear me. Also, thankfully, there was also no one to SEE me. If what followed had been caught on tape it could have easily gotten me a prize from America’s Funniest Home Videos.
It was easy enough to get the glue on the remainder of the frame under the skin, so I just need to bend it around that curve and get it stapled down. I laid a 50# bag of sand and 2 – 35# dumbbells on that curve to help hold it. Still it fights. I clamped the most severe part of the curve with C-Clamps side by side all the way around. Still it fights. And I laid across it while I put staples in (not as easy as it sounds, believe me). And I swear, STILL it fights. That thing fought me with all the power that the forest could bring to bear. And, yes, I had it turned the right way, I’m positive. I was sweating and exhausted by the time I finally got it stapled into place. Why was it so hard? I have no idea. You tell me.
But finally it was done, and for the MOST PART it fit.
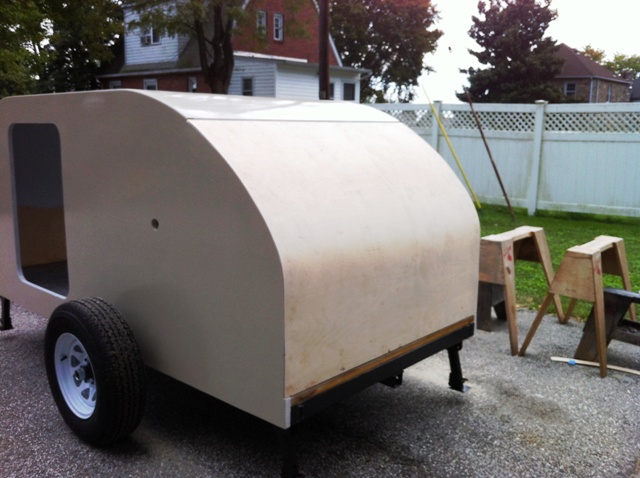
I glassed the outside with the same 12 oz. cloth that I used on the roof, but only one layer.
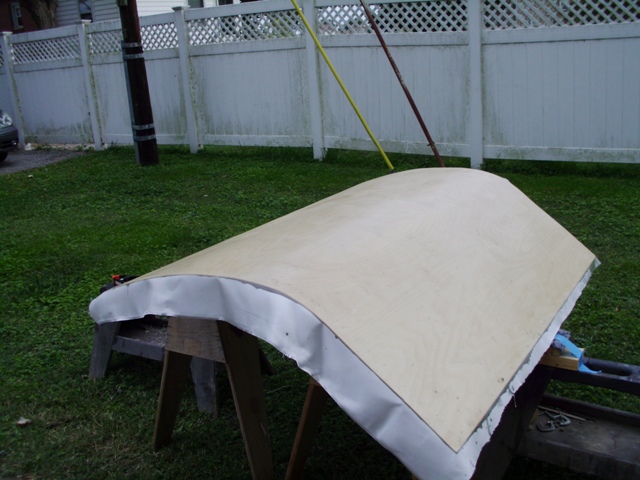
Next problem…(OF COURSE there’s a next problem…..) I cut the notch in my wall way too deep (I swear it didn’t look that wide when I was cutting it, and I measured it for 3/8" so have no idea what happened), but the gap between the wall and the hatch skin was a good ½”. No way could I ever seal that and get it waterproof, neither would the roof edge molding even conceal a gap that large. What to do…what to do…what to do.
I had to sleep on that one. And a lot of possible solutions came to mind, but in the end it came back to my old standby, fiberglass. There’s more than one way to skin a teardrop, and I wasn’t tackling that hatch again, no way in hell. Anyway re-doing the hatch would not address the problem of the too-deep notch. So I decided to use fiberglass tape to build the wall back up to meet the hatch.
I started using 6 oz. cloth, 2” wide, but quickly realized that, because the cloth was so thin, it would take forever to build up any thickness.
Plus 2” tape left a big overhang to cut off. The more layers of cloth, the harder it is to trim it off, and I wanted to lay up a few layers at a time to get it done quicker. So I changed to 1” wide 9 oz tape which required no trimming and was much thicker to boot.
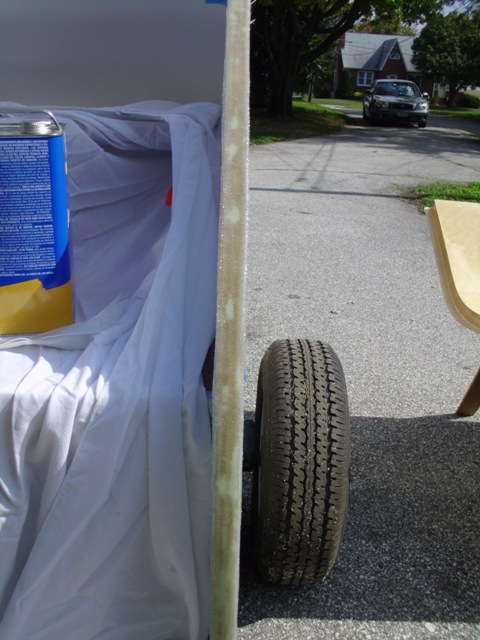
This is with 6 layers of tape along the entire edge.
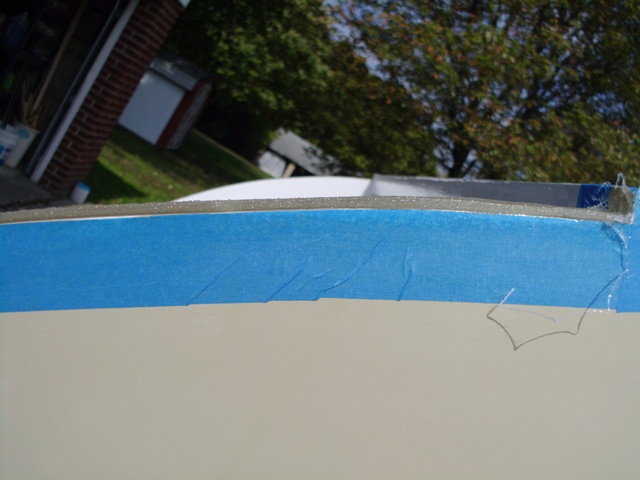
I have adequate thickness now over most of the area.
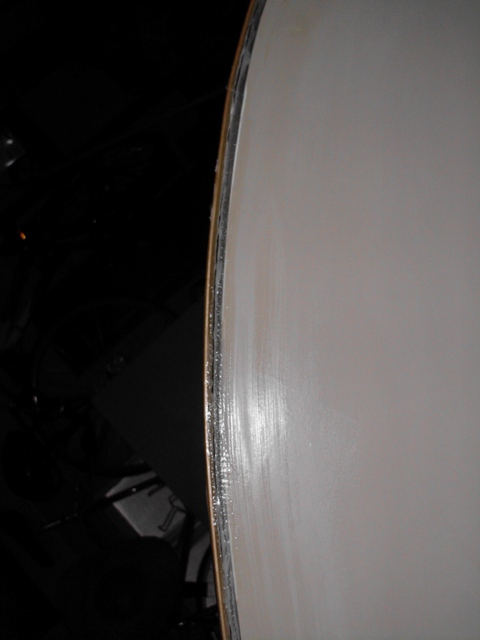
It looks like there is no room there at all for the galley wall cap molding or the rubber seal, but I still have to sand it smooth, and I also have to sand the inside edge of the hatch skin because I used a strip of glass tape in there also to reinforce that edge. I will be able to shape them however much I need to get the right amount of gap.
I still have a couple of problem areas though. I apparently cut into the wall more at the top and I will need to build that up just a little bit more. I’m thinking maybe 3 or 4 more layers of cloth, tapering it down to the curve.
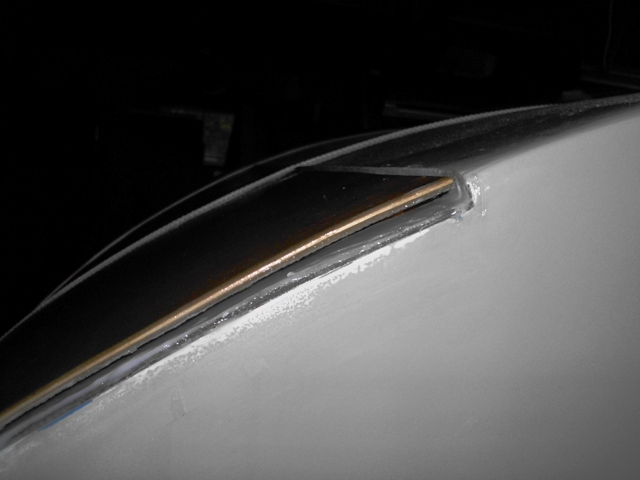
At least with this method, between laying up tape, and then sanding it, I can finesse the shape of the wall until I get it where it needs to be to match the shape of the hatch.
The last concern is, God only knows how, but it appears I have a tiny bit of springback at the bottom.
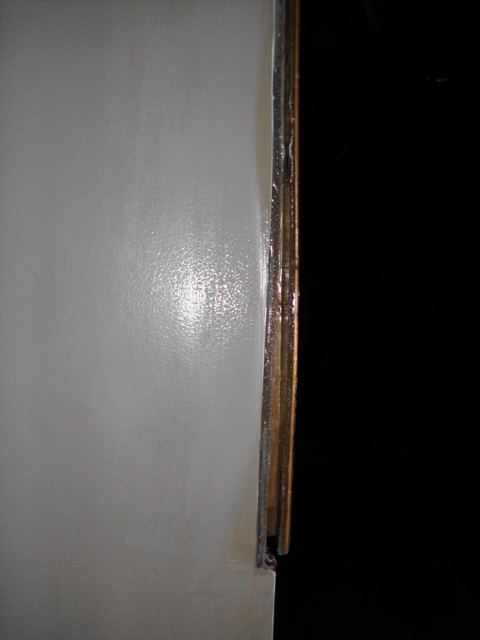
It’s not excessive though, so I am thinking that between building out the wall just a little, and using draw down latches (and maybe a piece of trim across the bottom of the tear below the hatch to bring it out a bit, if necessary) I can make it all fit somehow.
I know it seems like a long, slow, tedious, convoluted way to get the job done. I wish my skills were such that I didn’t make these mistakes in the first place. Or maybe if I had more woodworking experience I would have seen a simpler more effective solution. But with what I know and what I had to work with, I think this is the solution that will get it done for me. One great thing about fiberglass is you can really compensate for a lot of shortcomings in woodworking skill, and hide a lot of mistakes, because with enough fairing and sanding, after it is painted there will be no visible evidence that it ever happened.
The temperature dropped here 30 degrees between Saturday and Sunday. Now I just have to hope that I get a couple of more days warm enough to complete the rest of the fiberglass work and then get it all painted up. Once I get the hatch and the wall modifications primed, I am going to put one more fresh coat of paint on the whole thing with the sprayer. I would love to have that done before I have to button it up for the winter, but who knows.
I can at least get the interior of my cabin done over the winter.