Here’s a little demo of how I did the 4-way splices in my hatch wiring. The 3-way, or tap in T-splices were done similarly. I don’t know if this is the “best” way, and you may want to do your own research on wiring, but this is how I did mine.
Two wires to be joined and my super-duper-double-throw-down wire strippers.
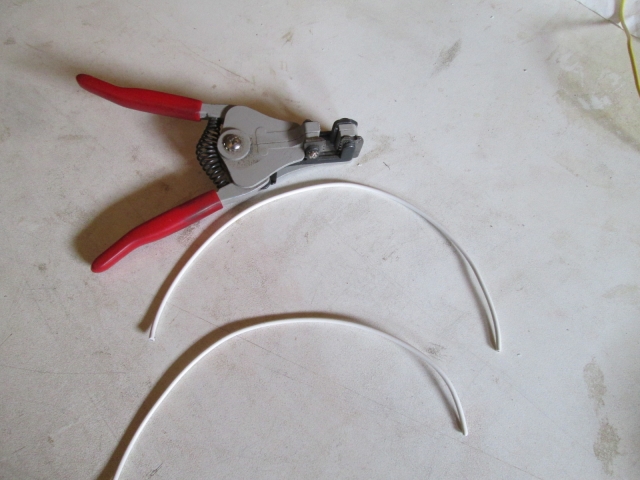
The strippers have different size knife stations for the different gauge wire sizes. There is a double action where the cutter side jaws come down first and the clamp side comes down second.
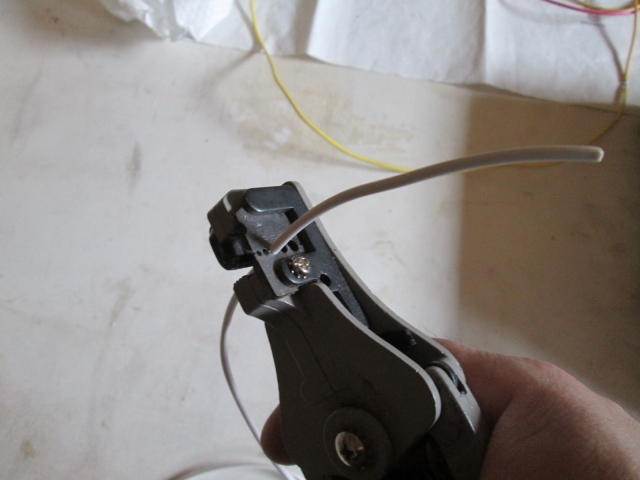
Once the jaws close down the plier action strips the insulation…
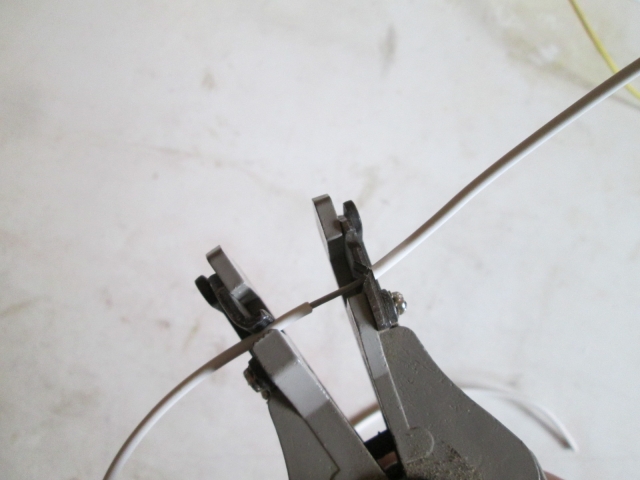
… leaving a bare spot. For a 3-way tap in the strip on the second wire would be at the end.
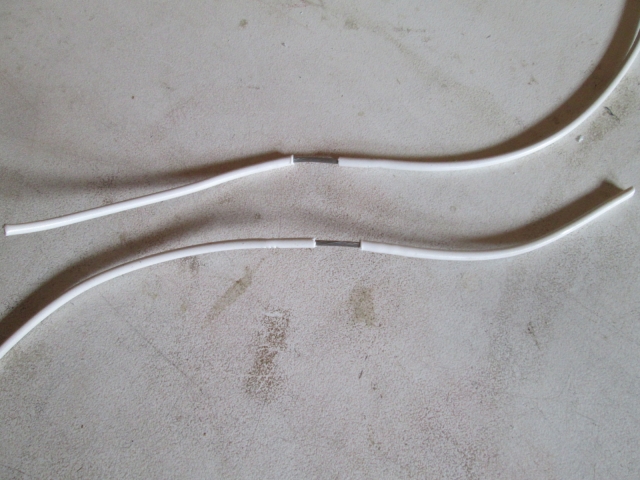
“Cross the beams, Egon”.
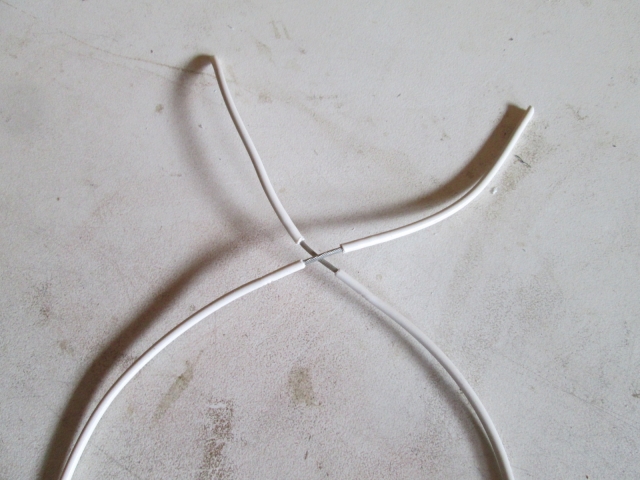
Twist and shout.
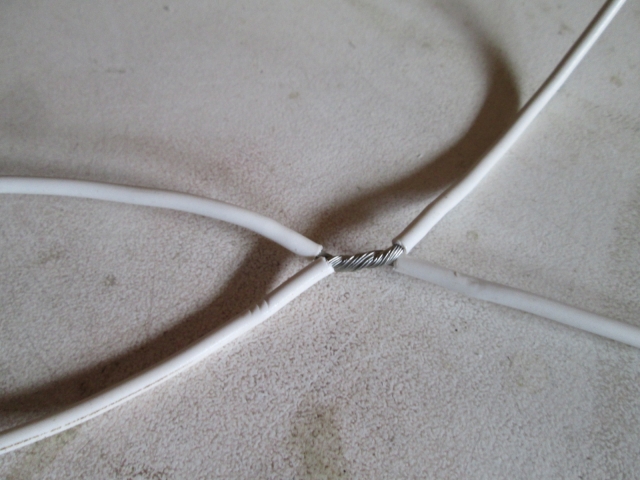
Solder the wires. I have this big honking hot iron that I inherited from Yvette’s father. I like it because I can get in and get out quickly. It is kind of clunky and does not fit your typical soldering iron stand/holder, so I use the metal paint roller tray as a multi-tasker; as a holder to lay the hot iron in, as a drip catcher, and as a catchall for all of the little bits of wire insulation and clippings (… it can also be used to roll paint or glue). The regular wire strippers are just weighing the wire pair down to the rim of the paint tray to keep it from moving around.
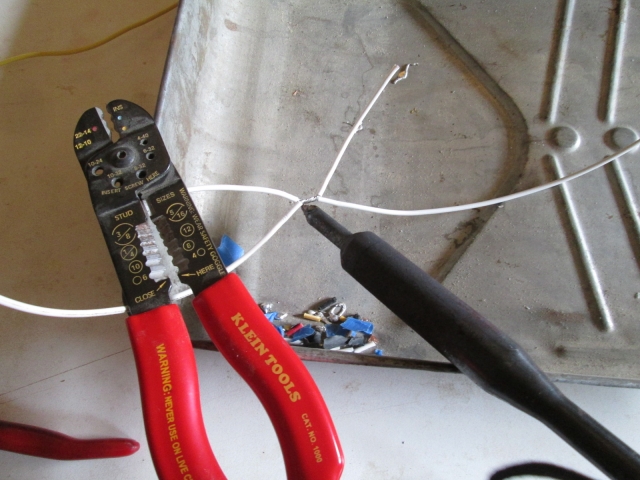
Just enough solder to get the job done. You don’t want to pour solder down the wires to the point where it is a big glob or is sucking back up inside of the insulation making the wire stiff.
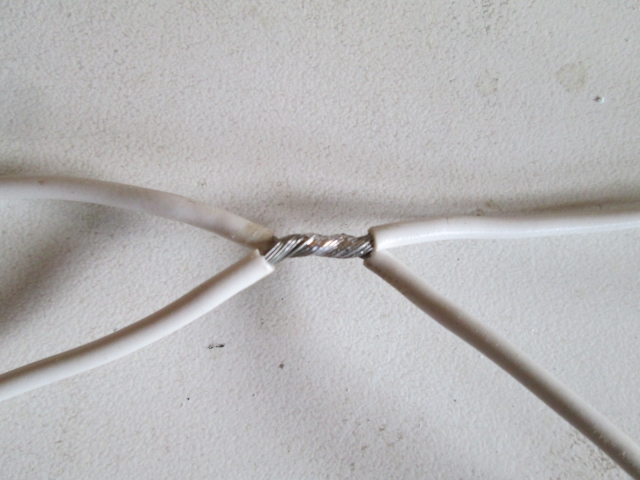
Slide the shrink wrap on (shown in progress) and center it over the splice. I like to have at least 3/8 inch overlap between the wrap and insulation after it is shrunk. The shrink wrap will only shrink about 1/2 of its starting size, so it is good to have a variety of sizes on hand.
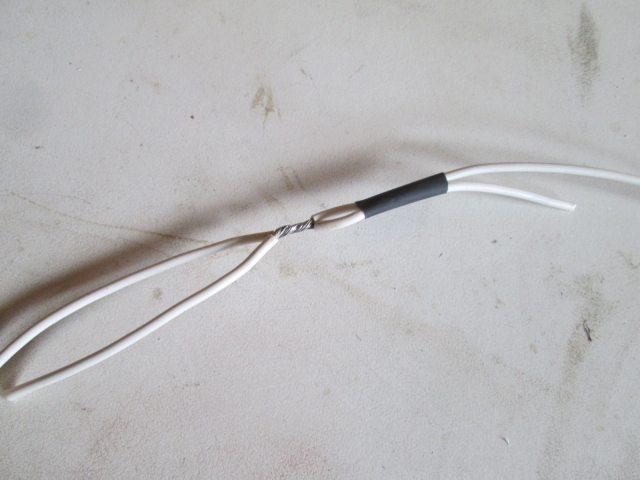
Last step is to shrink the shrink wrap. You can use a lighter or the side of the iron, just be sure to keep the heat moving around all sides and don’t overdo it or you will melt thru the wrap and have to try again.
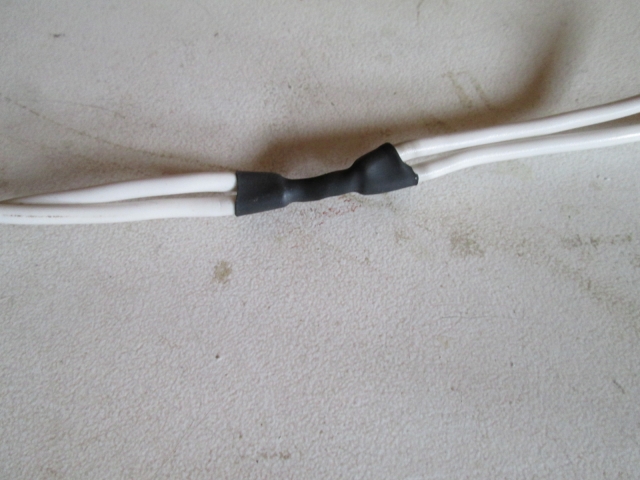
Next I laid in the yellow left turn/stop wire and extended the galley light wires. I fiddled around doing some test pulls to see if I could get the galley light wires to make the turn thru the fixture mounting block, and to make sure that I could get all of the wires thru the hatch “grommet”. I ended up drilling both of these holes a little larger and re-contouring the lead ins to them to suit. I’m currently leaning toward laying the wires in place before adding the 2nd layer of foam.
Time to start dry fitting the second layer of foam on the hatch. So up on the roof I have quite a bit of flexibility with my cuts and yield because the spaces between spars are relatively narrow, but on the hatch it will take just over three full 2 ft wide panels, with seams that will be in your face, and I would like to minimize the amount of work I have to do to make those seams fair. Also, it would be nice if the seams in the top layer of foam don’t land on the seams in the bottom layer.
The factory edges of the foam are bead and cove, and for some reason they all have one edge or the other that have been crimped or bent. Not sure if this is from handling at the factory while it was still hot from the extrusion process, or from banding and settling during shipment. On the ones where the beaded edges are affected they are just sort of bent, not crushed, and the cove end is fine.
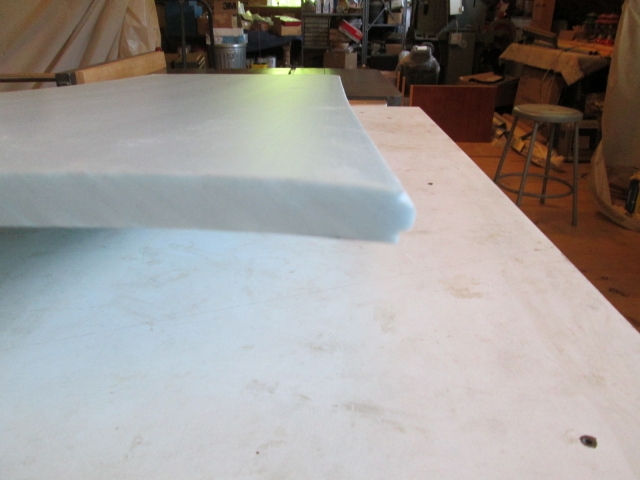
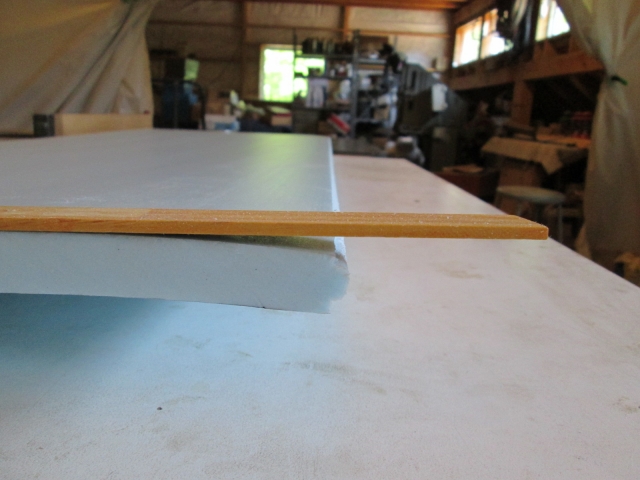
On the ones where the bead end is good the cove end is crushed on one side.
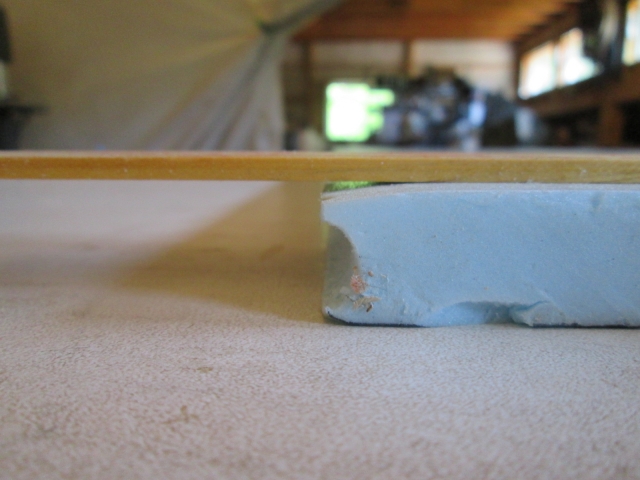
So I culled thru my pile of foam and picked out the better pieces for the hatch.
Rather than have a small filler strip at one end or the other and have the seams stack up on each other, it made more sense to split the difference and have about a 1 foot wide starter strip with a corresponding half panel at the top. But let’s not waste any foam either, so after ripping the gimpy crushed bit off, I took a little more than half the panel to use in the widest bay up on the roof, just behind the roof vent fan (shown here dry fit).
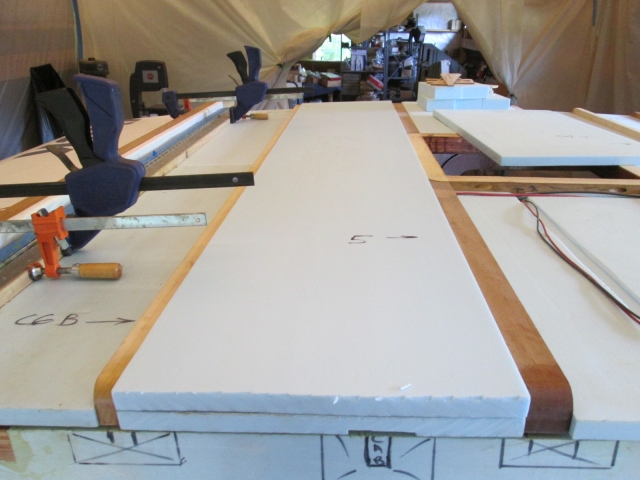
That left about a 10-1/2 inch wide starter piece with a bead on top for the hatch. Here I have cut out the notch to clear the ‘would be’ hatch handle blocking.
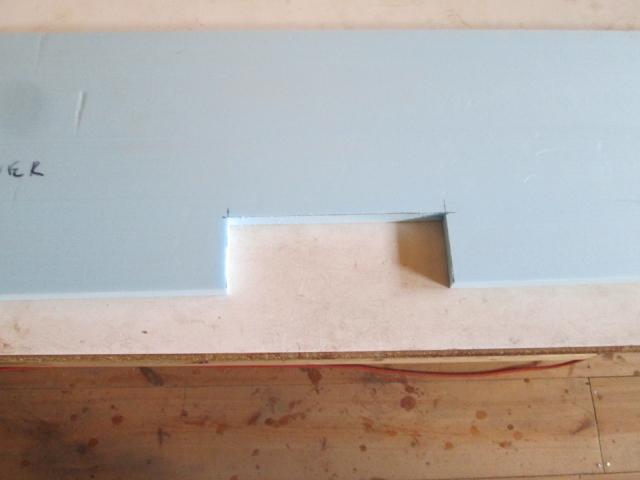
… and dry fit.
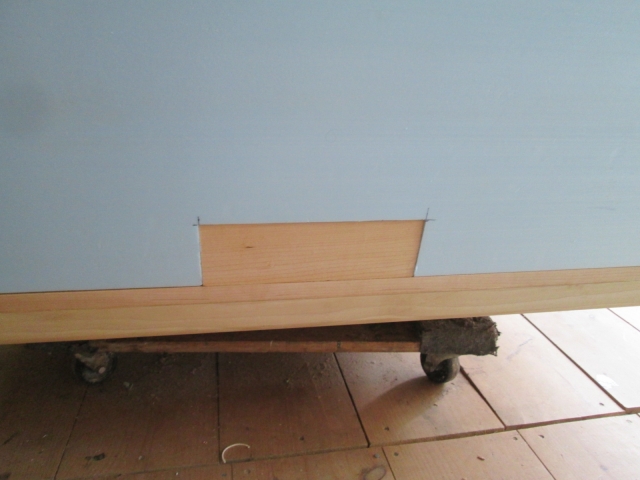
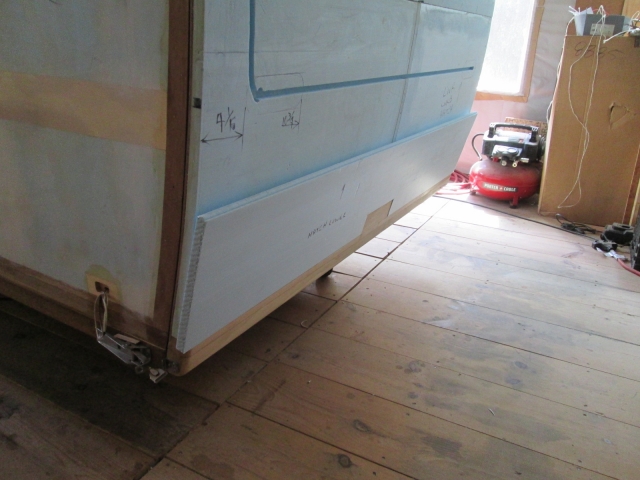
Laid flat again on the bench, I found that my somewhat arbitrary method of sizing the starter strip put the license plate mount (governed by the location of the marker light and wireway in the next panel) across the seam. The license plate mount location is shown traced out here.
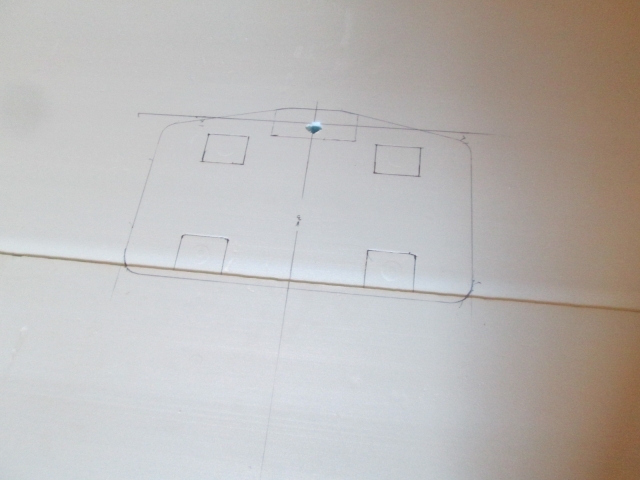
At this point I kind of got stuck in a do loop noodling over how I am going to sink the flat plate mount into the curved hatch, but eventually decided to shift the mount up slightly, fudging the hole for the wires, and letting the rest simmer on the back burner for now.

Cut some access holes for the taillights. Used a paper cup to trace round holes then just used the steak knife to cut the holes. They will be opened up later to match the taillight blisters.
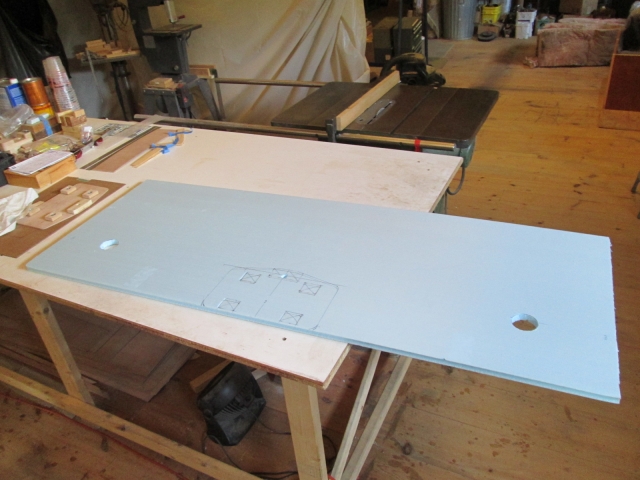
This piece also got a few kerfs at the top where it gets into the tighter part of the hatch radius.
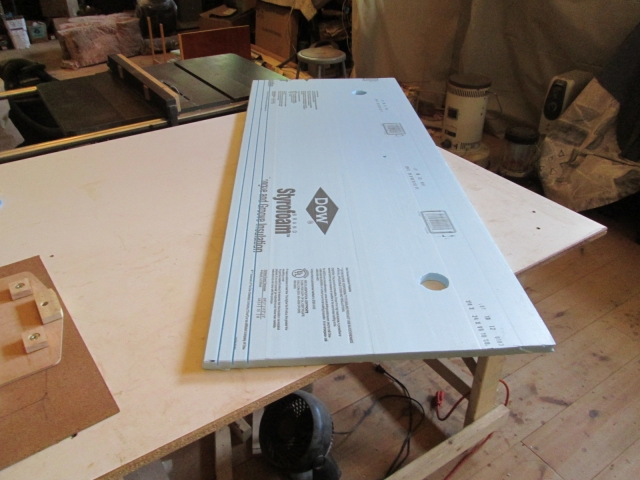
With the starter piece temporarily fixed with packing tape, I dry fit the taillight panel. You can see how the panel bends a little more sharply at the first kerf resulting in a bulge, so I think I need add at least one more kerf.
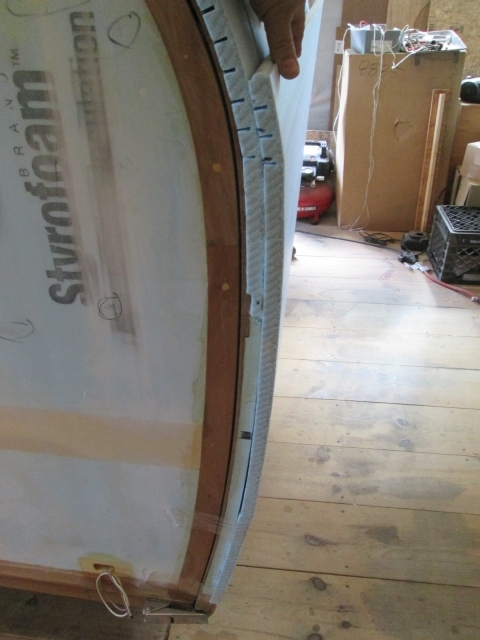
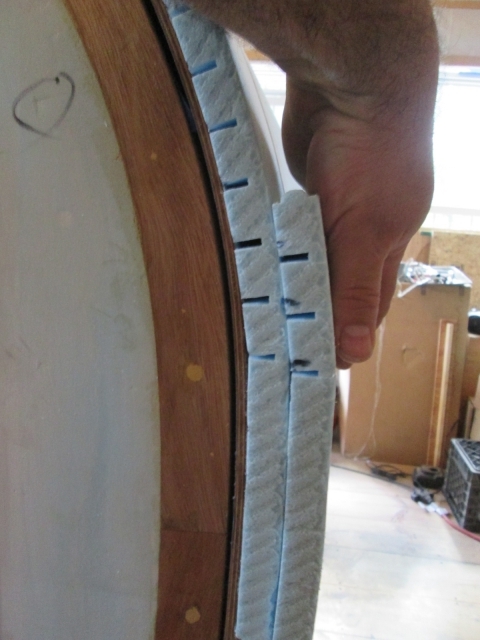
The taillight hole lined up with the wireway just fine.
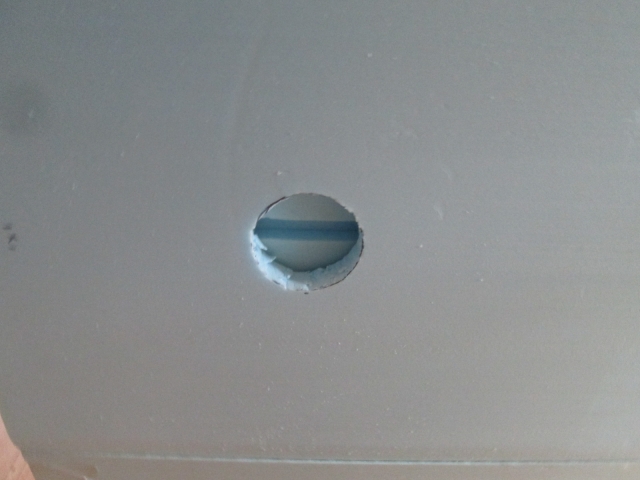
Confident with the dry fits I stuck the starter panel down with the PL300 and stretcher.
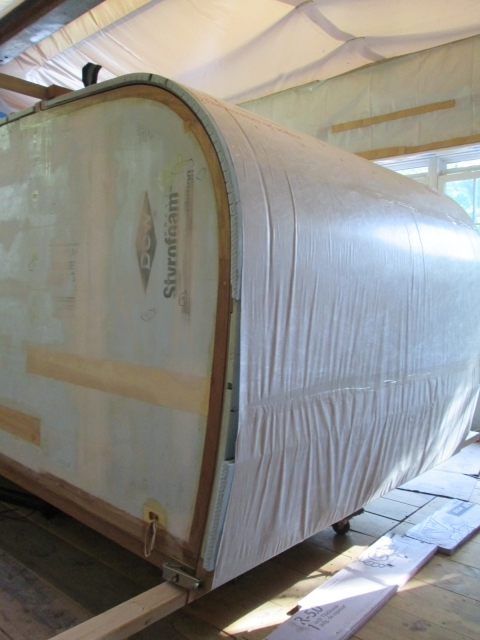
Here’s a tip: don’t keep your PL Premium and PL300 tubes in the same bin. About halfway thru the glue up I had to reach for a fresh tube. Cut the tip off, pierced the inner seal and it wasn’t until I started to wipe off the poker on the caulk gun that I realized I had just opened a tube of Premium. DOH. Oh well, I squeezed some up into the nozzle and stuck a screw in there and taped the end up (like I do between uses) to prevent it from kicking off.
So that was only about 11 hrs, total for the 3 day weekend. I need to stop slacking off so much.