Okay, about 6 hrs in today and it feels like I got more done, or at least answered some questions so that I can move on.
First I trimmed up the hatch edge test piece and washed off the amine. Then I back gouged along the lip where the 6oz glass was wrapped around the foam side. I tried the Dremel with the conical burr, but that didn’t work well; the tip speed is next to nothing because the radius of the cutter is also close to nothing. Tried to score the ply with the utility knife, but that was tedious and nonproductive. Then I switched to the rotary cutter plunging down next to the glass and that went much faster; but the lip of the glass seemed fragile and I fragged it in a couple of spots. Next another pass with the rotary cutter at an angle to back bevel the gouge, then switched to the cutoff stone (actually 2 stacked) used as a sanding disc to clean the back side of the glass lip. This beat the edge of the glass up some more. (Also note the flexible cable drive attachment for the Dremel that makes doing detail work that much easier; less weight to wield.)
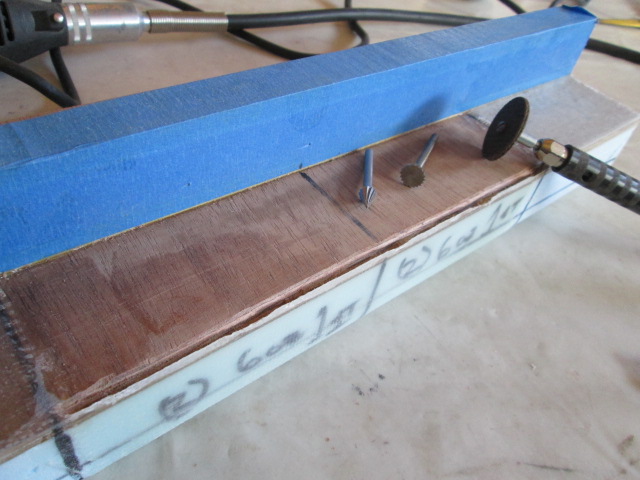
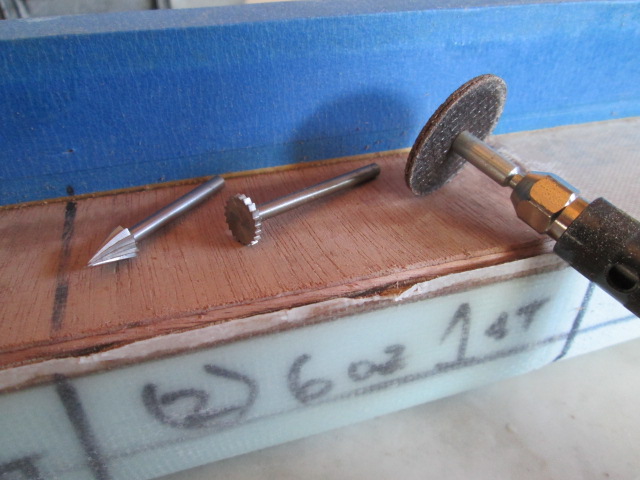
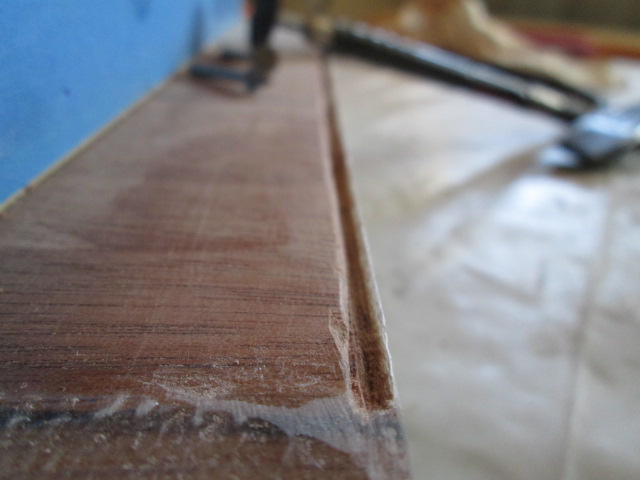
I’m not sure how much of this rough going was part of the learning curve and how much to attribute to the glass/plywood orientation, but the next area with the 6oz on the plywood lip went much better despite slipping onto the foam with the cutter in a couple of places (I hadn’t bothered to secure the test piece and was just holding it with my opposite hand, so I think I will do even better on the hatch that has a lot more mass and won’t jump around so much while working on it). Plunging down into the second ply of the plywood made it easy to follow the line of the ply for the first cut.
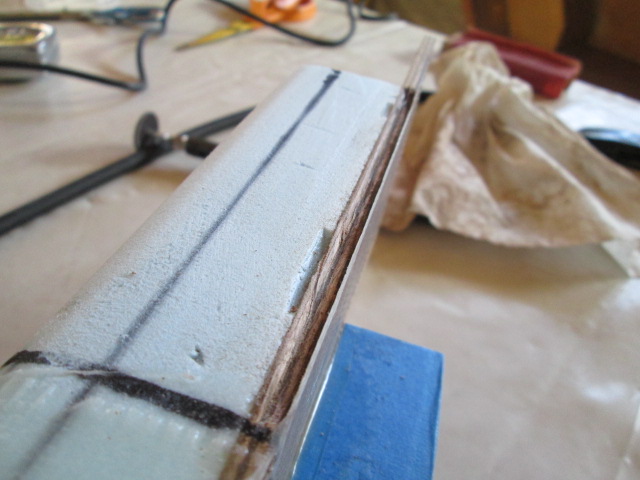
After the bevel cut and switching to the abrasive disc, looking from this angle made it easy to see when the wood had been sanded away and the glass was clean; it turned white.
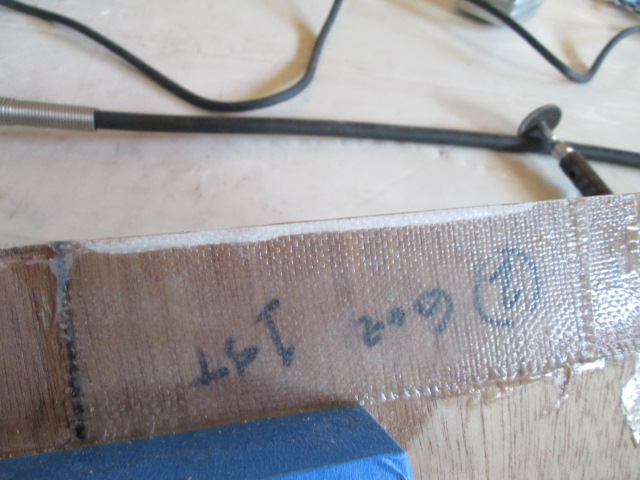
The lip of glass still seemed a little vulnerable, but either I had done better or it had a bit more structure being supported by the plywood instead of mostly foam.
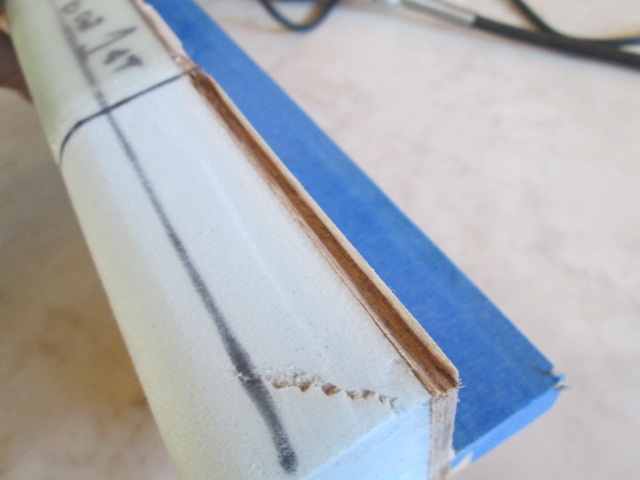
I just looked up the spec’s on the glass tape as I write this. It’s MIL-C-20079 (glass cloth, textile glass tape, and glass and wire reinforced glass thread) Type 2 (tape), Class 1 (untreated). A closer look at the spec revealed that it is in fact 5.80 oz/yd (although very different from the other cloth of similar weight… call me skeptical… will have to weigh a sample next time), with a thickness of 0.007 inch, 42 warp ends or wales per inch and 32 filling picks or courses per inch, and an average fiber diameter of 0.00036 inch.
The four plies, although slightly white in appearance, seemed to have set up hard, and were much more rigid (compared to the previous sections) once back gouged.
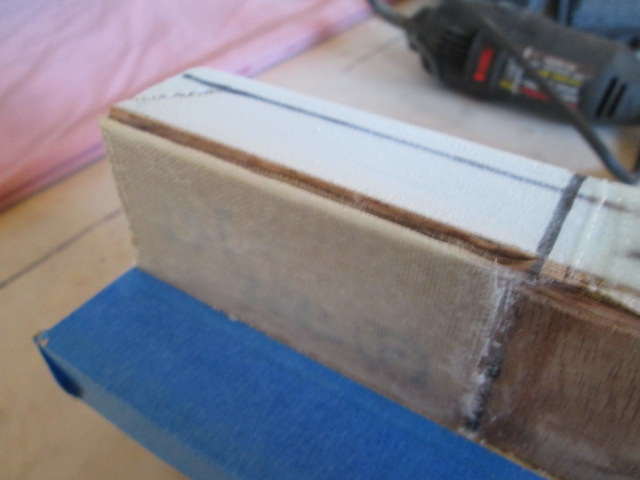
This got me thinking that 3 plies of the regular 6oz cloth cut into strips laid along the underside of the hatch seal lips would be about ideal. The extra ply would also help stabilize the seal lip, so that would also be a good thing. So while the convenience of the tape form is appealing, the performance of the cloth is more familiar and apparent, so I will stick with it.
With the fine weave of the glass tape I daubed on the wet epoxy judiciously. When it came time to pull the masking tape, a simple light score with the utility knife along the base of the ‘rib’ was all it took to help peel a nice clean release.
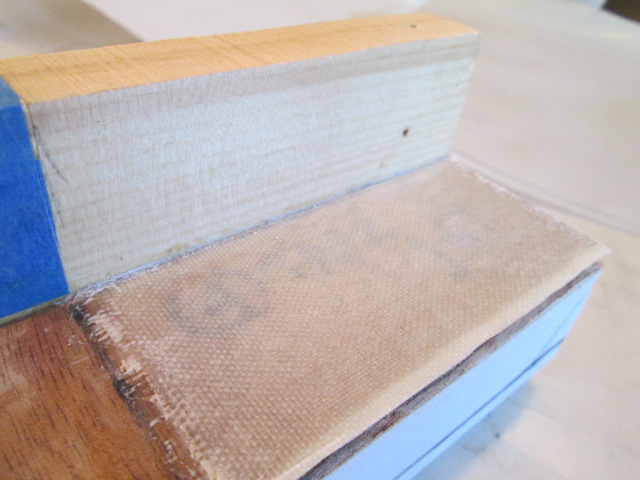
On the cloth side there was a bit more pooling at the bottom of the rib that took a few more, and heavier scores, plus a bit of picking to remove the masking. But still nothing that won’t be touched up when the seal lips get painted up to the base of the ribs.
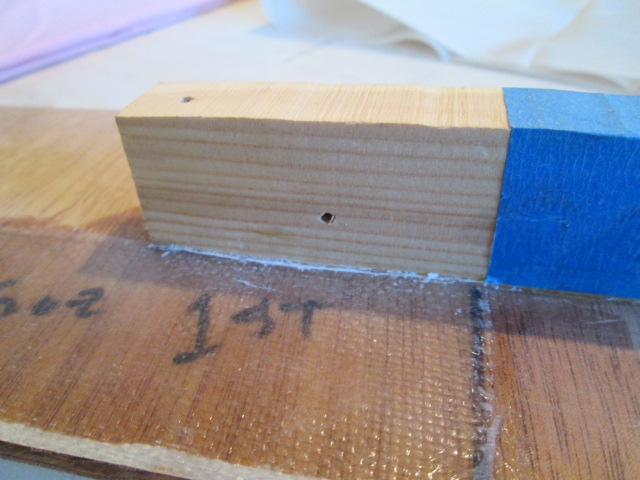
Setting that aside to give the wood a chance to dry up from the amine wash, and wanting to get some more things done before getting out the epoxy, I switched gears and sanded the filler test on the back of the TB. A fresh piece of 100 grit on the hand block did okay, but if I had much more to do I think it would be time to get the palm sander out. Not much to be seen in a pic, so none taken.
Then I started preparing poor man’s pre-pregs (PMPP) for the hatch bumper wrap and the side seal lips.
I used a scrap of the rosin paper to wrap and gauge from the base of the sill (on the inside of the hatch) up to the seam between the bumper and the sill on the outside. That way the seam between the bumper wrap and the outer glass skin will land on wood, not foam, making any future fairing to be done a little less risky for the adjacent foam.
Since the bumper wrap is essentially a long narrow rectangle, I didn’t bother with a full pattern; I just laid out the dimensions directly on the PMPP plastic (no pic). I pieced the 2 plies for the bumper wrap out of bias clippings and the last bit of the small 60 inch wide cloth I had bought for the TB. I numbered these carefully and oriented the lengths of the top and bottom plies so that the angled seams don’t overlap and are opposed between layers; similar to how I did the rim on the TB.
Similarly, the strips for the side lips needed to be about 79 inches long, so I had to butt strips together and stagger them between plies. It was a little easier here because these didn’t need to be on the bias, but I used up a bunch of my saved clippings for most of these slender strips. I did both sides of the hatch as one PMPP, one wetting, with a common cut line down the middle to get two strips. To get the third ply I had to get out the big roll of 60 inch cloth that I haven’t touched yet, but felt okay just taking a narrow strip with plenty of margin for the bigger cabin pieces to come later.
None of this is anything new, so I didn’t take pictures of much of it, but here are the PMPP’s all rolled up and staged at the ready.
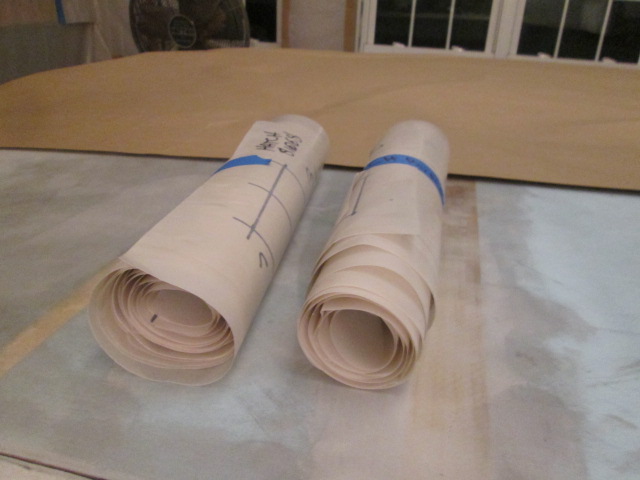
While I had the big roll out… and that was no small feat getting it out of the packing paper overwrap with the hatch taking up most of the bench, shown here pushed to where it was resting near the very far edge of the bench… I decided to go ahead and cut some strips to glass the hatch hinge location. Two at 4 inches wide and two at 5 inches wide, so that I can stagger the plies at the seams with the rest of the cabin and hatch glass; plus another at 5 inches wide to make up the ends, the difference between the 60 wide cloth and the cabin width, plus wrapping at the sides.
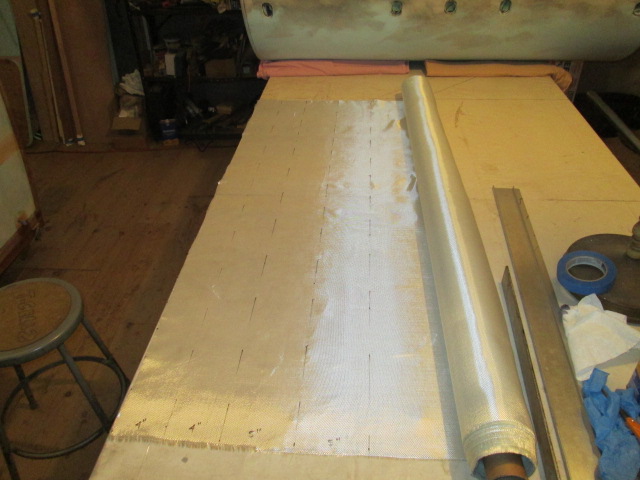
Once I had the roll of cloth wrapped back up and put away, I mixed up a single pump batch of epoxy and thickened it with some of the 403 microfiber filler (I’m calling this flox, although I can’t say for sure that the 403 has cotton fibers, it sure behaves that way). In hindsight I probably should have brushed some wet into the gouges first, but I didn’t think of that at the time, and it will be fine, I’m sure. Here’s the 6oz over wood section.
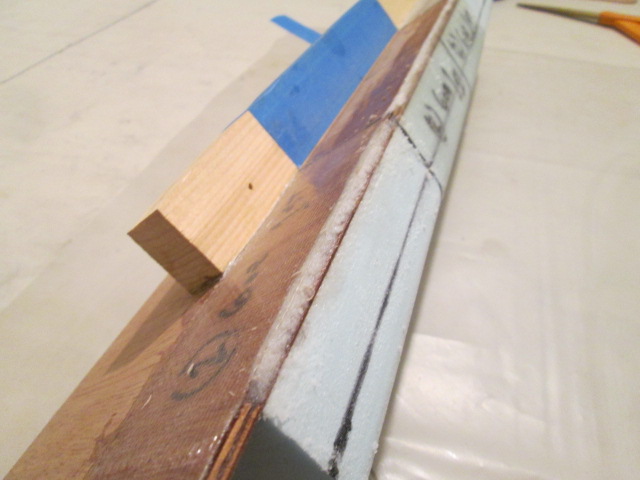
And the section with the 6oz wrapped up from the foam side. Had to work this a little more with the credit card squeegee due to the blowouts in the glass lip.
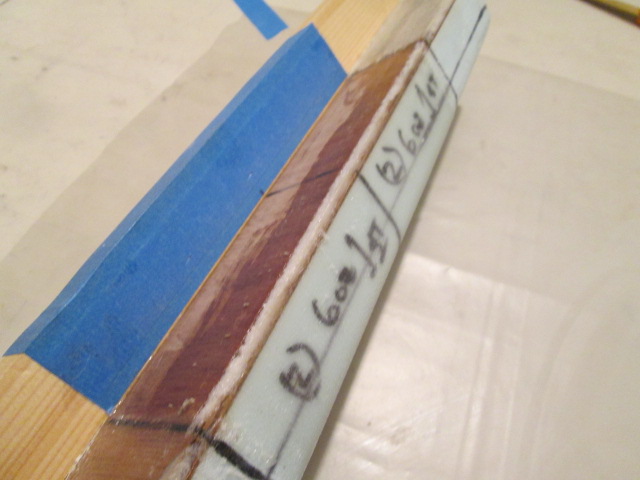
And the section with the tape over the wood.
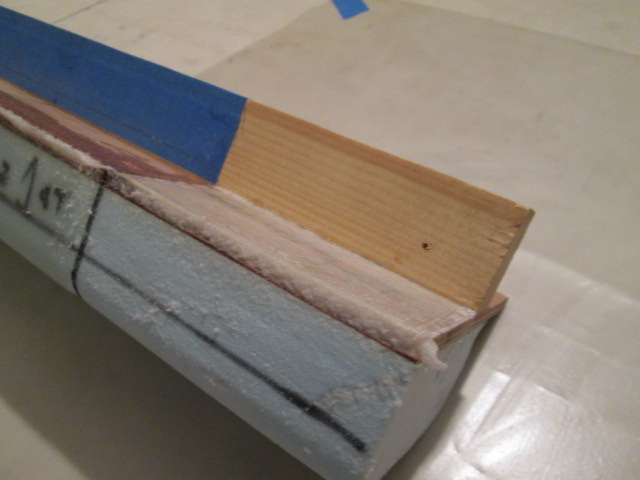
Since I had about twice as much flox as needed, I used a dab to fill those divots in the wire pull hole in the underside of the TB.
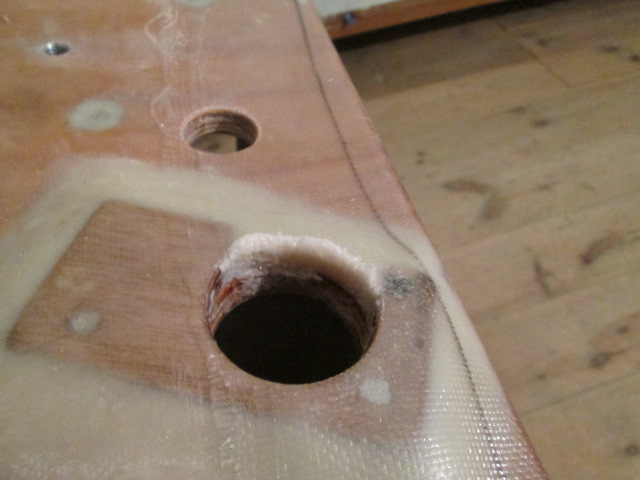
I wish I had been more mentally organized. I had a bit more flox (thick filler) left and I wished I had someplace to use it.
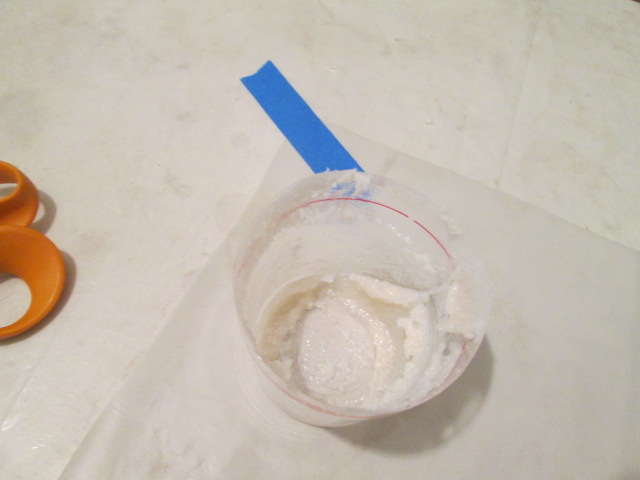
It wasn’t until I was on the ride home that I realized I could have used a dab where the hatch seal crosses from the inner skin ply to the hinge spar. There is a slight gap there at the back of the rabbet; and where I rounded the ends of the spar for the seal to roll up, at the transition between the radius and the square edge of the spar, I could have used a little fillet to help the glass transition. Oh well, I’ll get those areas with the next batch.
Anyway, despite already deciding on the method to use for the hatch edges, and proceeding to prep for that, I will continue and complete the test piece since it is helping with the learning curve and technique development. I had thought that I would use the flox corner technique around the side door jambs and doors, as well; but now I am thinking that I will just paint these areas with wet epoxy and not try to glass the jambs or edges of the doors. They have solid cedar framing and I’m thinking I will have my fill (no pun intended) of doing this before I am done with the hatch. We’ll see how tedious it becomes and how things develop at the doors when the time comes.
Felt like I got stuff done tonight and have made it past a big question mark in the build; how to keep a nice sharp panel line and still skin a corner.
