So it#s been 4 months since the last post and here's what has happened:
Now that the trailer bed is ready I could finally concentrate on the side walls that i had already assembled about 5 years ago. Time has not been kind to them and a lot needed re-doing, mainly because only one skin side had been mounted and they were still fragile in this condition. So I reinforced the frame, especially at the bottom where it would sit on the trailer bed, and around the door opening, reglued some of the interior skin, then laid both walls on top of each other on several supports and sanded down the outer edge to have two completely identically sized and shaped walls (I wouldn't want to think what might happen to the roof skin if one side was higher than the other...). Then I bought 11 sheets of 4mm (1/8th inch) luan and shipped them back on my flatbed trailer (probably the last time I can use it for that purpose...)
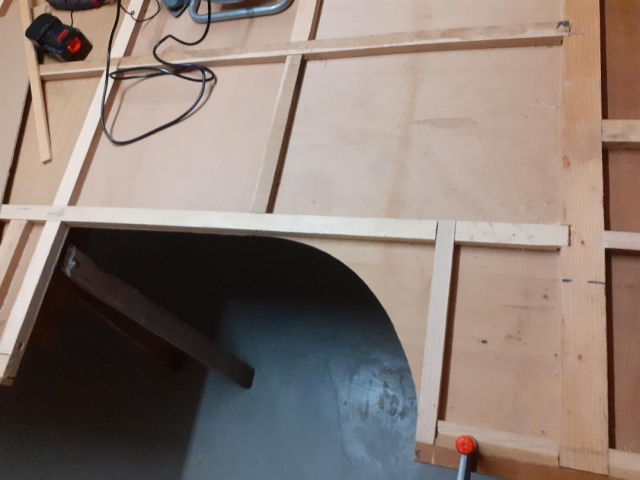
This is what the wall looked like when I put it on supports. The wheel well shape wasn't yet fully defined. The rather strange positioning of the frame member at the very left of the pic is due to necessary support for the screws that will hold the eyeplate to hook up the clamping screw to hold the whole body down on the flatbed. Won't be seen once the outer skin is on, but rather useful, I dare say.
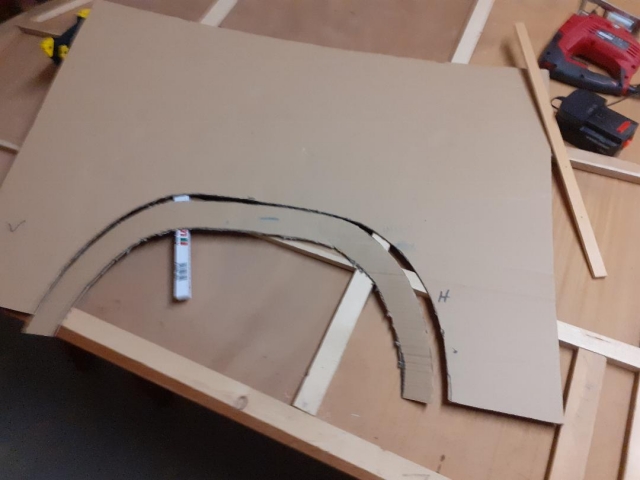
With this model I will shape the wheel well cut-out. Now for some explaining: the wheels are currently under a black plastic fender that reached out up to the side limits of the flatbed. It will stay in place once the trailer body is mounted. So the frame must accommodate the shape of the fender, but the outer skin will cover both the body frame and the fender (which has a downward-bent outer part). That's why the size of the wheel well cut-out has to be different for inner and outer skin, and here's the model for it.
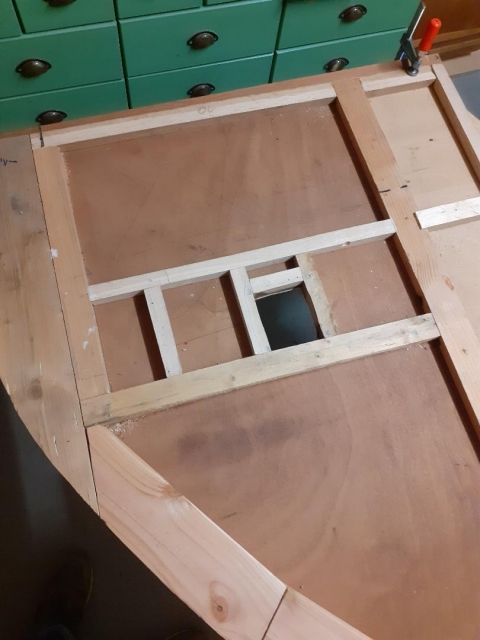
Another thing I needed to prepare for was the connection to shore electricity. This trailer is not meant to be off-gridded, so I am only installing 230V electricity (with the help of my electrician son), and this is where the connector socket comes in, it is near the rear underneath the kitchen workbench on the driver's side. The fuse box will be mounted to the left from the inner wall, so there has to be an additional vertical member to receive the screws
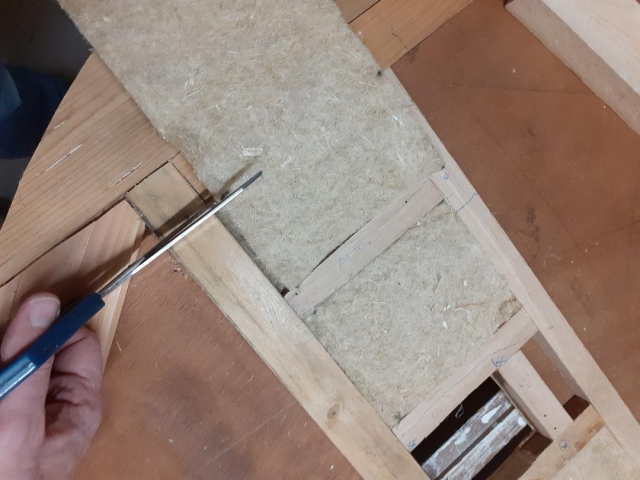
Now for the fun part: Insulation!! I am a big fan of renewable building materials (having used them when I restored an early 20th century house), so I opted for sheets of woven hemp fibers. They come as a roll of 1 m width, 10m length and a thickness of 1cm (2/5th inch). Since the inner frame is 2 cm (4/5th inch) deep, I am cutting the mat twice and layer both bits on top of each other. This material is quite flexible and can be pushed and pried into shape no problem, and cutting with regular sharp scissors is quite easy.
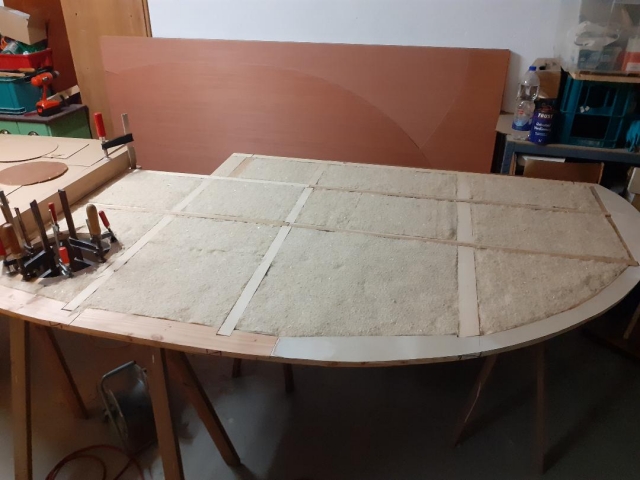
Here the insulation is almost complete, and the outer skin parts can be glued down. One thing that was still missing is...#

...the subframe for the single window (porthole) that will be mounted on the driver's side wall. I got a 12" diameter porthole from a RV supplier here, which unfortunately came without mounting instructions. So I looked at the window seal profile and decided to add 1.5cm to the diameter of the wall hole, shaped the inner frame accordingly and glued that in. Right now with winter time, glue takes over night to set, so work is rather slow...