It seems the black cloud of tool problems remains. That's ok, though. Just another challenge. Thought I'd share the laugh with all.
Yesterday I made a cardboard template, then transferred that to masonite for a cutting template for my hatch ribs. With a 73 inch wide galley, I decided I would want 7 full-width (3") ribs and 2 more for spacers which I will modify. No interior liner. My plan is a combination of the Steve Frederick and Roly design (as used on his 1/4 Nelson, with the outside "ribs" extending beyond the sidewall).
My plan today was to cut the ribs for the hatch using the router technique as described by Aggie79. Thanks Tom!
I secured the masonite template to the plywood and cut out the first rib. Tested it for fit, made adjustments and used that rib as my new template. I then secured the ply template to the plywood sheet with screws, flush with the surface. Using my top-bearing flush trim bit I began cutting with the bit set at half the finished depth. Two passes were planned.
First, a little background on my Craftsman router. It has a plastic "triangle" knob that's used to tighten the base to the motor once depth has been selected via rotation of the motor in the base. Standard set-up. But, it doesn't hold the position for long, depth increasing with travel. Usually not a problem with soft woods but hardwoods or plywood cause it to loosen no matter how hard I crank it down. Even when taking shallow passes, I have to stop about every foot and re-adjust. Frustrating but ok when using a trim bit as depth increase is tolerable.
Â
After cutting 3 ribs, I notice that the bearing spacer is moving while I'm cutting. That's not right. Turns out that the set screw has vibrated out and is now missing. So, I stop the router and lower the bit, fully seated. Normally, I don't fully seat the bit as it's not recommended and also makes it hard to get out of the collet. But, I have no other choice. I finish the rest of that rib and start on another. As I'm readjusting the depth for the bazillionth time, I notice a piece of metal on the plywood. Inspecting it, I see that part of the cutting edge has broken off from one flute.  It's a two-fluted bit, so I press on. It's not cabinet work after all. It's cutting ok but the sound isn't smooth. After about 8 more inches of cut, the bit breaks completely off from the shaft. Nice!
Â
The options now are to completely stop, order another bit and wait for 3-4 days for it to arrive.  The big box stores don't sell this type of bit. Or, come up with another plan. I decide to use a straight bit and use the shaft of the bit as a substitute "bearing", aligning the shaft of the straight bit with the template. That works ok for another rib and then as I'm tightening the depth knob,,, part of the knob breaks off. It becomes laughable at this point!
Using pliers, I'm able to tighten what's left of the knob and press on. But, that's short-lived. The bit becomes dull and starts smoking. I have another straight bit, use that and create two more ribs before it also craps out. Now,, the only option is to order another trim flush bit so I can finish the remaining two ribs. I got 7 cut out, need 9 total.Â
I've located a bit with a lifetime guarantee and will order that tonight. Wish I had started with that one. 7 ribs in 9 hours. Fun, fun!
Here they are prior to dressing with the belt sander:
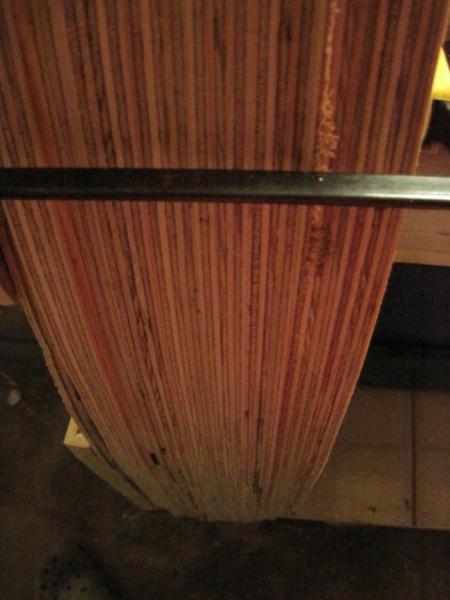