For those of you interested in the door frame construction, here's the info. I get 16ga. sheet metal bent into a Z shape, I buy 3 6' pieces. The drop will be used to alter the hinge for the screen. It has a 1" outer flange, 2.25" deep inside, and 1/2" inner lip. How deep you make it depends on just how much door you want to put into it. The latch I'm using takes a minimum of 1.25" thickness, my screen door 3/4", tears wouldn't need to be so thick as the typical latch/ handles can be put into just about any thickness. You have to include thickness of the outer door, screen door, and enough room to squish the bulb weather seal. The Nomad required me to do some routing on the screen door to make it fit, so on this one I went deeper. On a standy, the advantage of the 1/2" inner lip is that it keeps water from rolling in from under the door due to excessive road splash. I just miter the corners and weld it up to fit the opening. Large flange to the outside, small inner flange on the inside, just keep it square.
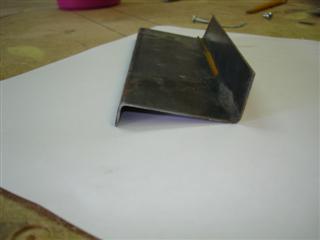
I then take the outer door and mate it to the inner door. Both doors are made on the table in a jig I make up so they are identical in size. Cut 1 side of the hinge on an odd number of knuckles so that you have 3 flaps that are independent of 1 side of the hinge. I cut up some of the door jamb drop and weld it to the hinge flap so that it captures the screen. To attach the screen, I use some small screws through the door, not just a wood screw to hold it in place.
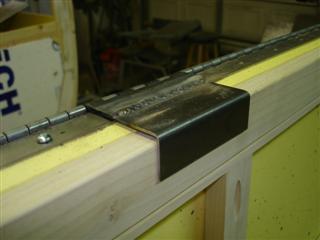
Once I figured out that my eye glass prescription had changed and the progressive lenses weren't working to weld...I put on the lined bi-focals and my welds came out cleaner. At any rate...I grind them smooth and hit them with a shot of bondo so they really look nice.
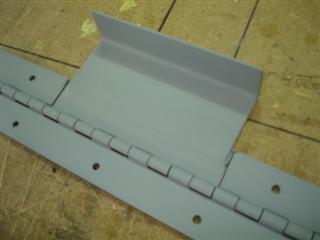
Full length hinge:
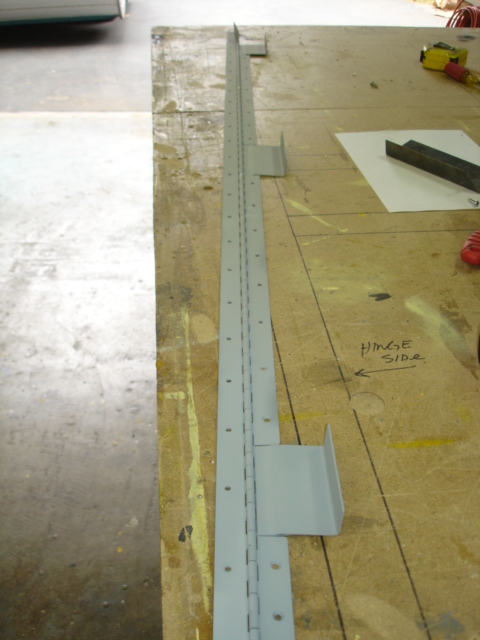
The outer door will be skinned in aluminum, then centered in the jamb, allowing some space for weatherstripping, then I attach the hinge to the jamb with a series of screws. I only do a couple first to make sure it's going to work before I blow a ton of holes in the jamb. I trim out the door with 1.5" x 1/8" aluminum strap and allow it to overhang the opening with enough overhang to take a small bulb seal for weatherstripping. Once fit up...then mark the jamb for the latch and deadbolt. Once marked, I drill them out and work them with a metal blade in the scroll saw and a file, kind of a pain. No pics...I'm not there yet.
Stuff to watch out for...remember which side is up and inside on the doors. The screen door needs to be built so that when you mate the 2 doors together, that the latch fits completely in the screen door opening with the slider on it. Typically, you will need to relieve some material on the screen vertical to allow for the latch. Also...I've found it's a good idea on a scratch built screen door to beef up the bottom and top of the slider in case you try to shut the outer door when the slider door is shut. I found out the hard way. I use poplar for the screen and outer door construction. It works easily, takes paint/ screws great and is less prone to warping. I tend to make my doors beefy as they get used a lot and I've seen tons of older trailers with "floppy" doors. The same process can be done in aluminum, but I'm not set up to do the aluminum welding anymore. I'd imagine that the same process could be done with any thickness door combination, but this is what I'm doing.
Hope this is what you wanted. Doug