Mel, I do use a bit more tape than some, but it really does help keep the glue from going where I don’t want it to. I hate it when the stain won’t take because of glue sealing the wood. Also, with the contrasting stains it makes more sense to apply the finishes before final assembly. I also don’t like it when the clear coat gets cloudy due to glue haze after wiping squeeze out. I’m pretty sure I am not the king of tape use. Maybe Aggie Tom’s Silver Beatle build is a contender for that title?
I was out to Mecca by 10am, but seemed to get a slow start. The front cabinet and shelf panels need another coat of poly on one side, but I like to leave that until the end of a work session so that I don’t have to worry about kicking up dust while I work on other things.
So I thought I could start working on dry fitting the galley shelves and counter first, leaving time to do the poly later in the day. Makes sense to start with the shelves so that the counter isn’t in the way while I work (same as in home kitchen). I hadn’t bought any maple to make ledgers for the upper shelves, and I had no confidence in the new table saw to accurately cut the grooves.
It made the most sense to work from the bulkhead mounted shelf ledgers out to the face frame. The ledgers against the bulkhead that will support the shelf panels will be interrupted by the chases for the hatch actuators, so I did some math and a little sketch to figure out the cut lengths and how much stock I would need. This is looking down on one of the chases.
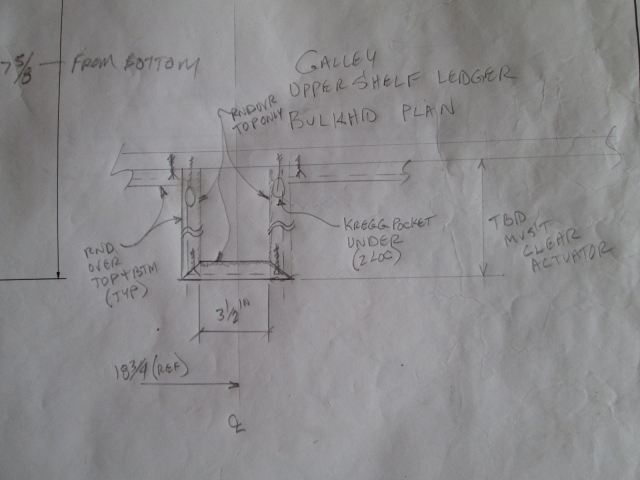
I did have a couple of pieces of pine drops that were close to the right dimension, so just ripped a skim cut on the saw to get them ready. The blade misalignment to the table is just bad enough that the rip fence cannot quite be forced to align to the blade. What a waste of my time and money. Might be good for building a garden shed or playhouse for the kids, but absolute junk for finish carpentry. I wasted two of the shorter pieces of pine trying to get it to run the slots (not sure I wanted to use pine anyway). Both pieces were about 2 ft long. I “set the fence” (a long tedious process of measuring many times between both edges of the blade and the fence, horsing the fence skewed to match the blade, clamping it, and then seeing how far off it was before repeating) and then ran the piece thru twice flipping it in between to make sure the groove was centered. The grooves were not bad at one end, much too wide in the middle of each piece, and again oversize at the other end. I gave up on the saw… again.
Next I tried a 1/4 inch straight cutter in the router, which gave much more consistent results, but was still an oversize slot for the 5mm (3/16 inch) ply. Karl has a short 3/16 dia x 1/4 shank end mill cutter, but it has a rounded end; might not matter but it could cause the panels to either float too much in the groove, or pinch. It might have worked, but I no longer had enough of the pine to finish the job. I thought about running out for maple and taking it to work to use the saw there, but that would take time and more money. Looked at the excess cedar, but was reluctant to change themes in midstream, and it would have to be ripped. Reluctant to waste anymore wood on this saw.
Other options: I had the rough edges that were ripped off of the Red Grandis used to make the hatch ribs. And I have tons of the small 1/4 round maple trim that I made earlier and have not used. So if I switch to cleats underneath (like the under counter cleats I showed earlier) instead of the grooved ledgers, and use the 1/4 round maple trim on top, the different species won’t be too obvious, and I can avoid using a table saw.
So first I used a straight cutter in the router to skim the rough edges down true, making 2 pieces 1/2 x 3/4 actual size. Then switched to the 1/4 inch radius bit to round over one corner (shown upside down here).
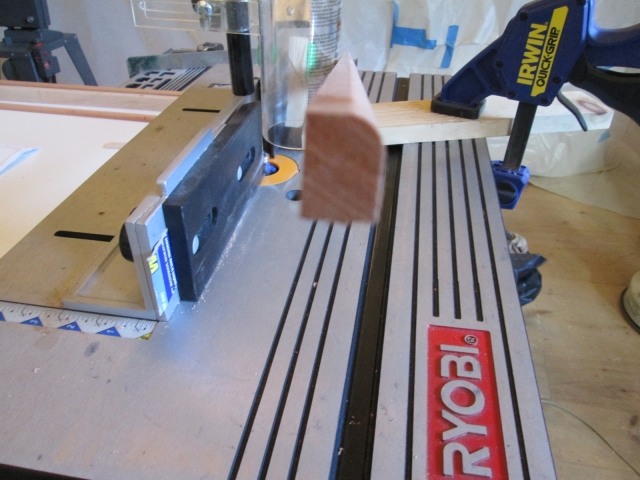
Here is a mockup giving a better idea of what I am on about. The first pic is looking at a cross section of the shelf face frame railing as if looking toward the side wall of the galley. To the right is the maple piece representing the shelf front rail. Underneath the thin ply is the cleat stock 3/4 inch tall. On top is the small maple 1/4 round (white).
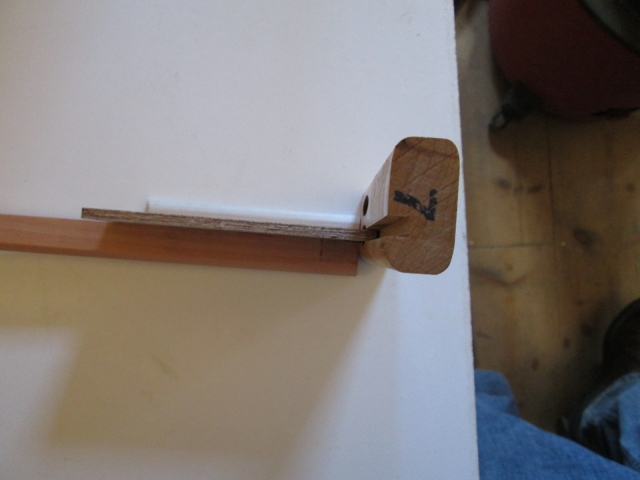
You can see that the cleat hangs below the lower edge of the rail, but I will deal with that in a minute.
Here is the same thing without the rail.
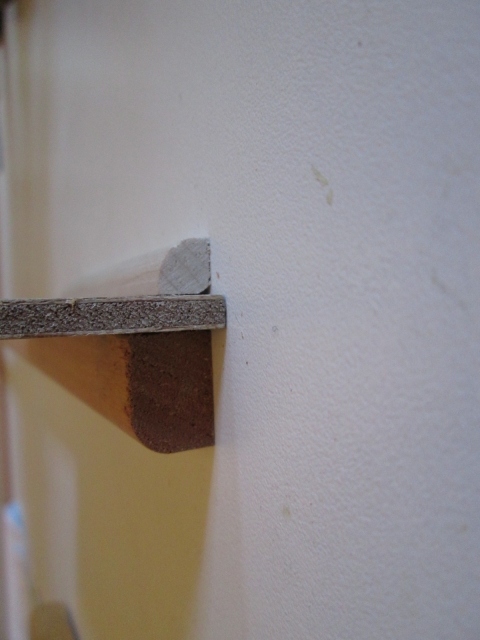
Back to the mismatch between the cleat and rail. Plan ‘A’ was to radius the end of the cleat where it meets the back of the rail so that it turns up and dives into the back of the rail. So I set up the 3/4 radius cutter (bought to put the roof edge radius on the roof spars) and ran some scraps.
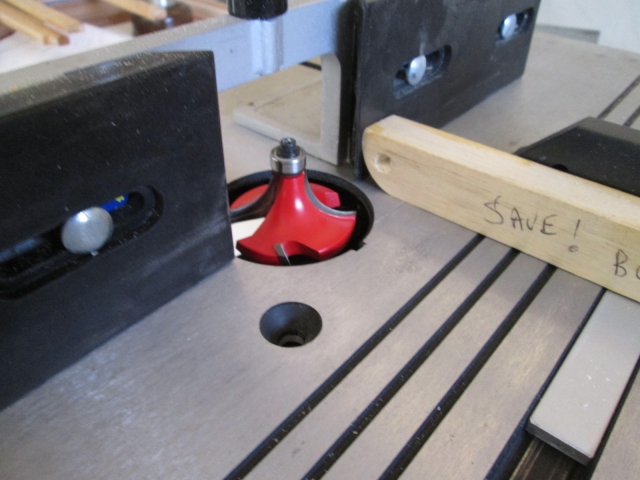
Even though they are not the same height, referencing the bottom to the pencil mark I tried to get the radius to end at the mark.

Not 100/ct happy, I kept going. Made a simple stop fixture for the miter saw. By clamping the 1x3 to the fence with its end under the saw, I could trim the end of the fence off cleanly making the perfect zero reference, while also supporting the back of the work piece from blowout (which the grandis tends to do). (Speaking of cheap box store lumber, this 1x3 was only 11/16 thk!)
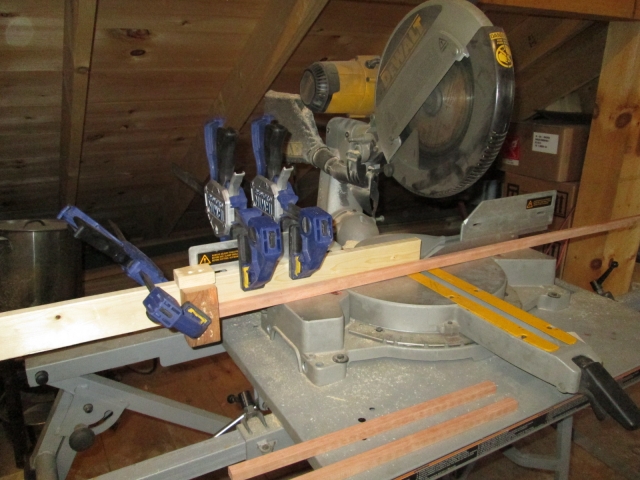
The little block screwed to the top of the stop block makes it easier to hang on the wood fence extension resulting in less juggling while applying the clamp.
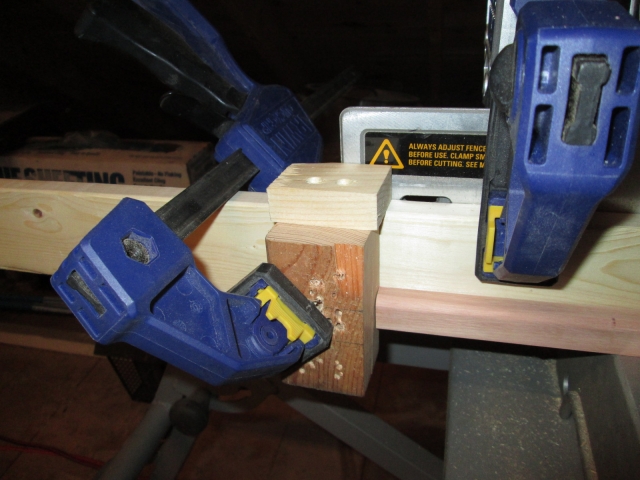
Quick and accurate repeat cuts. These are the four cleats for the ends of the upper and lower shelf panels that will be attached to the bulkhead to the outsides of the actuator chases (the actuators will be located inboard centered under the two middle hatch ribs, four ribs total).
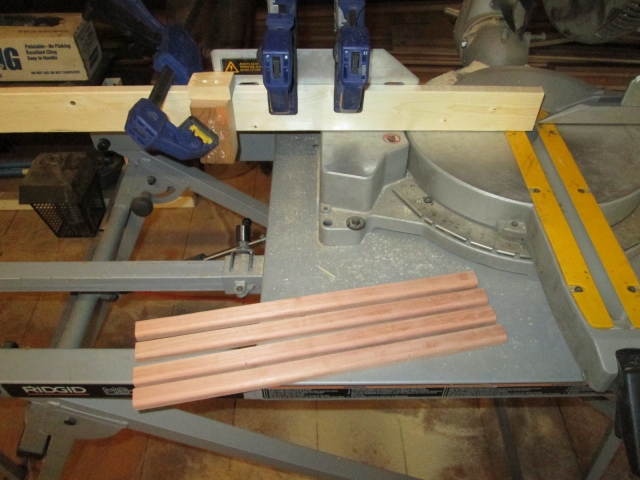
I put little strips of blue tape on the bulkhead at each end of the cleats so that I could measure up from the floor and mark the locations of the tops of the cleats on the tape. The piece in the middle with rounded corners is just a piece of ply that I used as a straight edge to confirm alignment between the cleats.
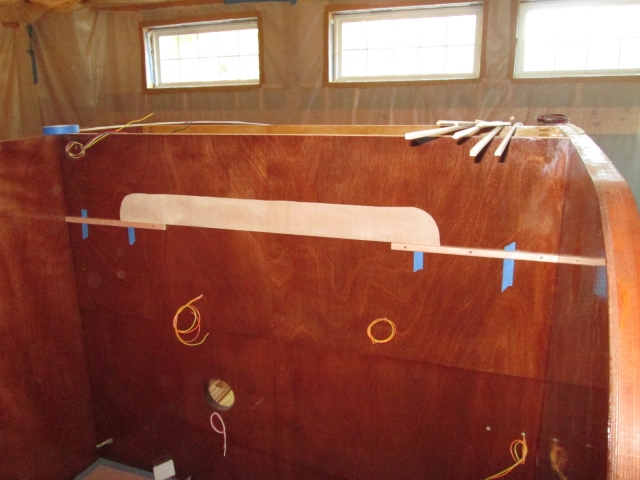
Here’s a close up of one of the cleats with predrilled screw placement. Just dry fit for now, still needs stain and finish.
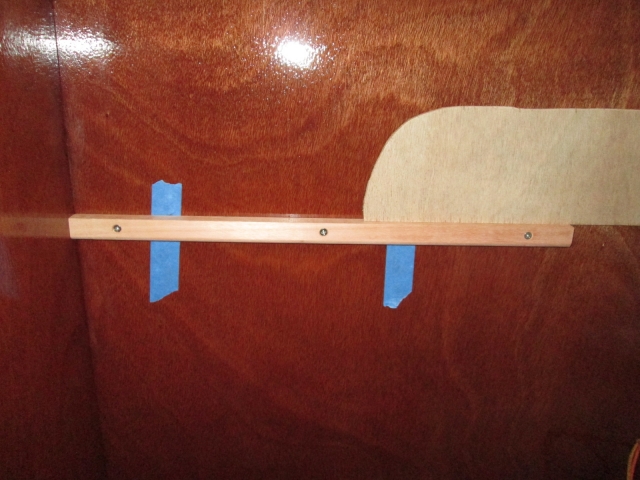
All four outer cleats placed on bulkhead. Eventually I will add two more cleats in the middle in between the actuator chases.
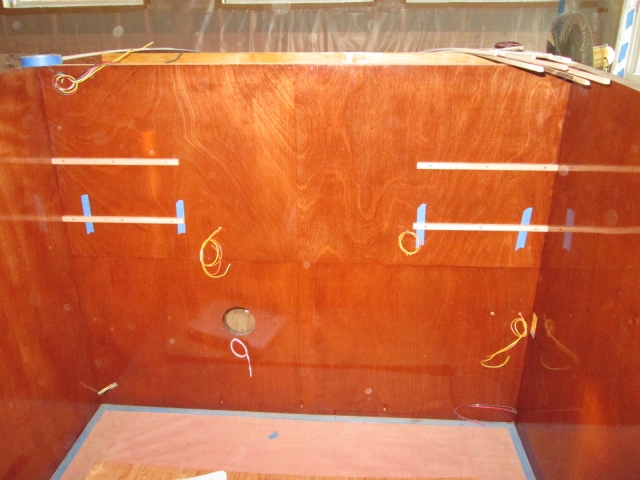
Detail looking at the end of the street side cleats.
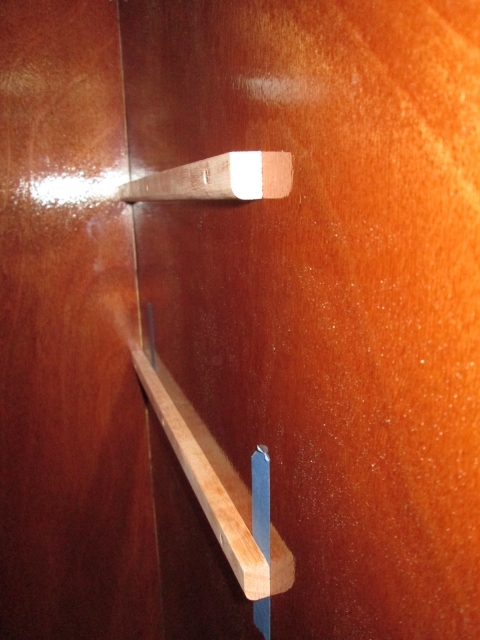
These are the similar cleats that will support the sides of the shelf panels between the bulkhead cleats and the grooves in the backs of the face frame rails.
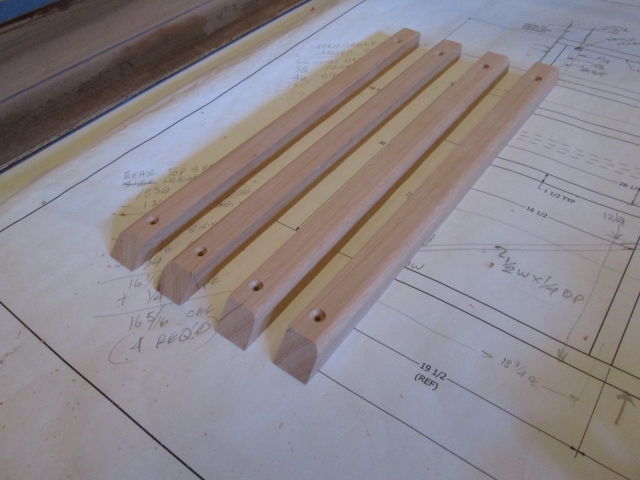
I thought it might be easier to miter the ends where they will be coped. Here I have rubbed a pencil on the edge of the miter cut to act as a visual aid while coping.

Here you can see how I nibbled away up to the line on the bandsaw. This is the end where it meets in the corner by the bulkhead.

A little cleanup work using the hard block and some 100 grit.

Next was dealing with the fit at the back of the face frame rail. Here I have stacked a piece of the rail stock on top of the cleat using a scrap of ply as a key to aid in alignment, and traced the detail onto the cleat.
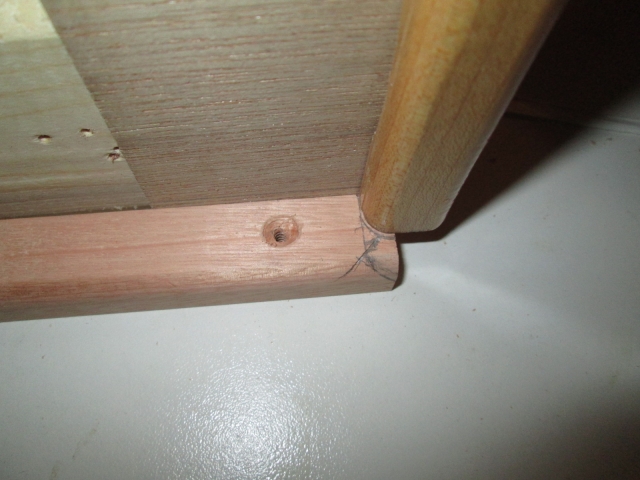
Mitered the lower part so that it tapers up to the back of the rail.
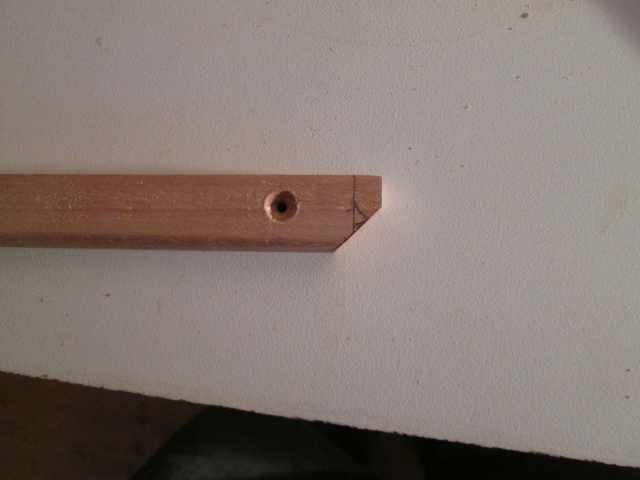
Then I nibbled the rest on the bandsaw.
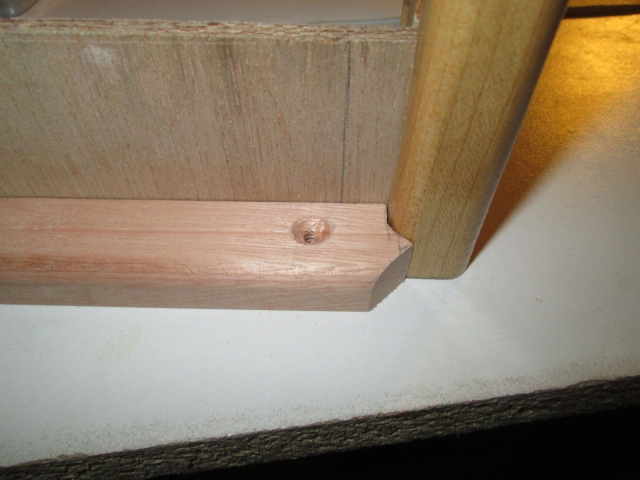
Transferred the first piece to the others and repeated 3 more times, then I sanded the upturn corners to round them over a bit.
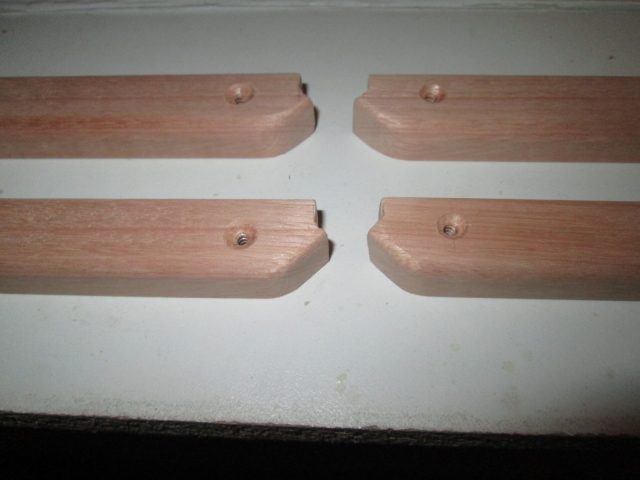
Well, like I said, it was a bit of a slow start, but I ended up getting on a roll by the end and completely lost track of the time. Ended up being 8pm, for a 10hr session and I never got the poly on the front panels.
...and now that I am writing this I realize that I didn't even consider adapting the side ledgers that I have already made and finished.
Oh well, I have to get to bed so I can go to work in the morning.
