I guess the other thing is that, if that table came out of an 8' camper (a few pages back), there certainly
should be room for it. I haven't built anything inside yet but I'm already thinking that I'm running out of space!
I want to get the sidewall sections taped in this week, and maybe get going on the bed platform while the next two wall sections are curing. I'll lose this weekend for building because of a family reunion/Thanksgiving dinner (Canada). I have a big extended family and, oddly enough, we're all friends...
EDIT:
Sidewall section are glued to the floor framing so once the foam has done expanding I can trim it, sand it and glass it. For the moment, the sidewalls are getting glassed with only the first (8") layer of tape. Once all the wall sections are in, I'll run the a 19" width of cloth (half the roll width) down the entire side. That will keep the long fibers continuous rather than having a seam in both layers of tape every 38". It's not as critical with glass as it is with...say...canvas because the tensile strength of two overlapping epoxied glass fibers is actually stronger than a single fiber. What I'm avoiding is having ALL the seams line up at the section joints, especially since those section seams are symmetrical from one side to the other.
I will be putting some sort of paneling inside, so if the taped seams are a bit bulky it won't show the way it would through paint because the paneling will float over it. That said, a couple extra layers of 6oz cloth are of insignificant thickness.
I switched my pumps over to the new resin & hardener jugs and propped up the old ones to drain every last precious drop...
Tomorrow night, it's a couple strips of tape and cutting out one of the last two wall sections. The rest of the shell (basically the nose) will be done as a single piece...probably in place on the trailer. Before then I'll need more cloth: I'm buying it in 25yd lengths -that's the minimum for a price break. So far my usage has been right where I figured once I allow for the extra wide tape on the rear floor.
That's the thing about glassing: get
ALL the prep work done ahead of time because it's always right after you mix the resin (starting the countdown) that you realize what you forgot to do.
Some gratuitous (and marginally relevant) foam porn:
The strips are screwed in to gently clamp the styrofoam under the potential pressure of the canned foam (on the inside as well)
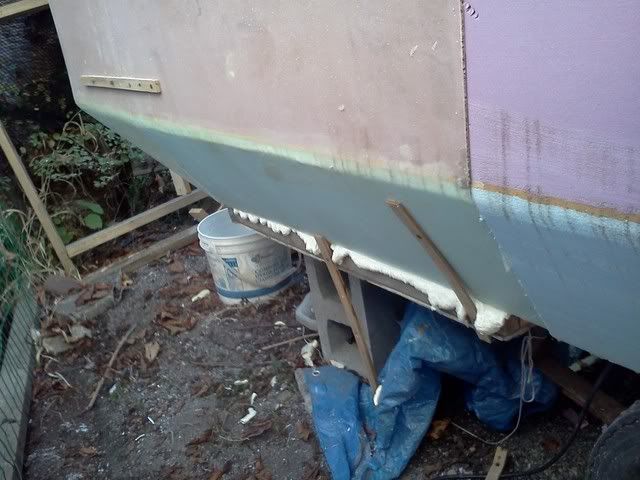
Here you can really see the standoff 'legs' I was talking about to hold most of the joint up off the framing to make room for the foam to expand and still maintain the same outside dimensions. I'll go back and sand out those areas so I can get foam in there too: that's one of those things you don't want to forget until after you've mixed the resin !
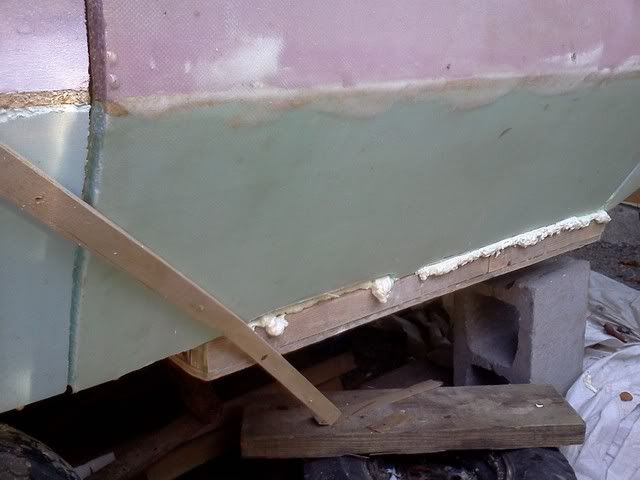
Once again, I gotta say how impressed I am with canned foam's value as an adhesive. When you build any kind of a shell, you go from a bunch of flimsy parts and, as those parts get locked together, the shell gets stronger exponentially. I'm seeing that already just from the foam. I think it was Louella (?) who posted the link to the Halloween Lady's video of glue testing ?
After seeing that, I did a couple test pieces and I was sold. One place it excels is in panel bonding (which makes sense since it's essentially super-expanding PU glue) as long as you control the expansion. I used concrete pavers and it worked like a charm...though I was testing it against cheap luan ply that delams when you look at it...
Still, the foam-on-foam bond wound up breaking the foam before the bond: what more can you ask for ?
It's also a fraction of the cost of GG.